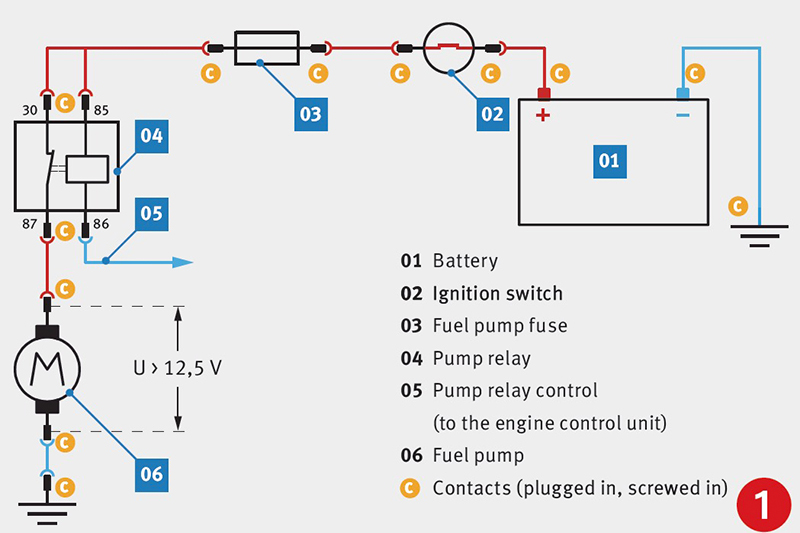
The technical team at MS Motorservice provides essential information to aid technicians faced with the possibility of a faulty fuel pump. Always check the contacts!
In the event of problems in the fuel system, the system pressure and volumetric flow of the fuel pump should be measured first.
If the measured values do not match the manufacturer’s specifications, it can sometimes be the case that the supposedly faulty fuel pump is replaced with a new one prematurely. Before you replace a pump, you should ensure that a corroded electrical connection does not cause a loss of power.
Depending on the flow rate and system pressure, the current consumption of a fuel pump is 5 to 8A or more. In the case of such high currents, clean and reliable contact points are important, since any type of corrosion or poor contact increases the ohmic resistance across the contact.
However, increased resistance necessarily means a voltage drop at the fuel pump.
The typical circuit of a fuel pump in Fig 1 shows a number of detachable connections due to screwed-in or plugged-in contacts. In addition, there are switching contacts within the ignition switch and the fuel pump relay as well as possible additional installations in the system, such as anti-theft devices.
Each of these contacts may have increased resistance due to oxidation, corrosion and an inadequate connection. This results in an undesirable drop in voltage in this circuit. A drop in voltage may result in a lack of performance by the fuel pump. The consequences are a reduction in pressure and flow rate.
It is worth noting that in modern vehicles, the fuel pump is located in the fuel tank and usually takes the form of a fuel delivery module. In this case, it is difficult to carry out measurements directly at the terminals of the fuel pump. However, it is necessary that the drop in voltage is measured as close as possible to the fuel pump. It is therefore recommended that the measurement is carried out at the electrical plug contacts, which are usually located in the cover of the fuel delivery module (Fig 2).
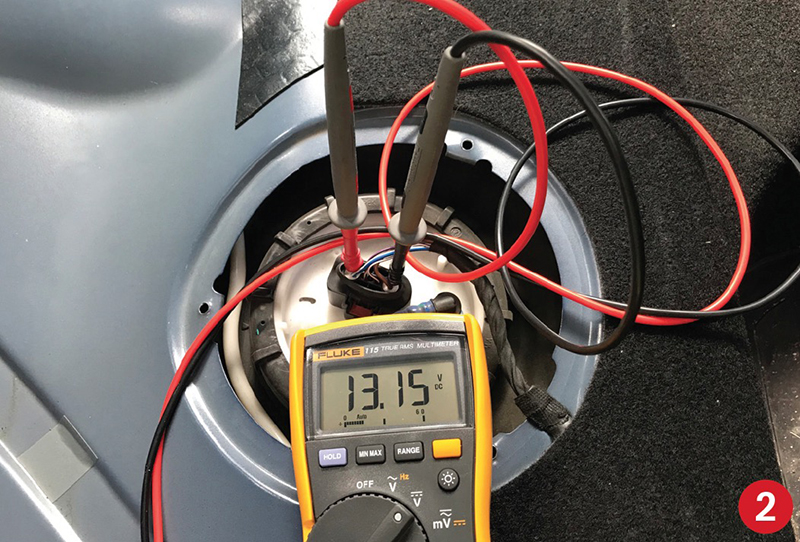
It is only possible to receive a correct result if the circuit is closed, i.e. if voltage is present. For this reason, you have to keep the engine running during measurements.
Loss at the contacts is unavoidable, even if the contacts are clean and tightly connected. The voltage at the terminals of the fuel pump is therefore always lower than the on-board voltage. The value should be as close as possible to the on-board voltage of the vehicle. However, the difference should not exceed 1 to 1.5V.
Recommended procedure
- Determine system pressure and flow rate
- Measure drop in voltage at the fuel pump. With the plug plugged in, connect the measuring instrument with the corresponding measuring tips to the rear of the plug (Fig 3). Never ‘puncture’ the cables (Fig 4)!
- A voltage of at least 12.5 to 13V must be present when the engine and pump are running
- If the measured voltage at the terminals or the plug of the pump is significantly lower than the on-board voltage, e.g. lower than 11V, there is a malfunction
- In this case, check the condition of all contacts in the circuit to see whether corrosion is present at the contacts (Fig 5)
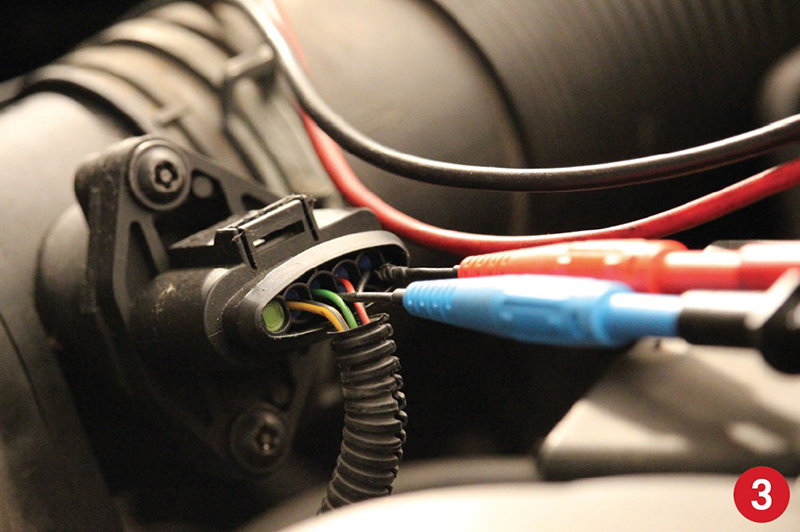
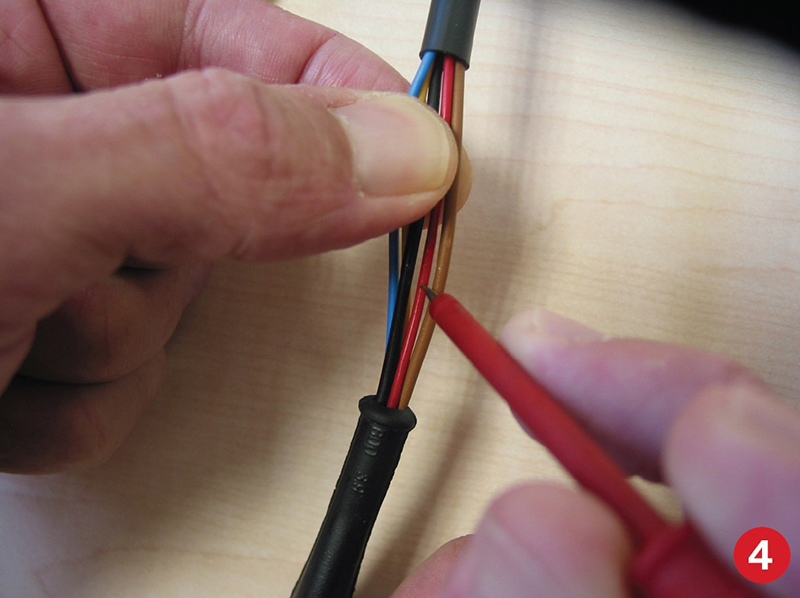
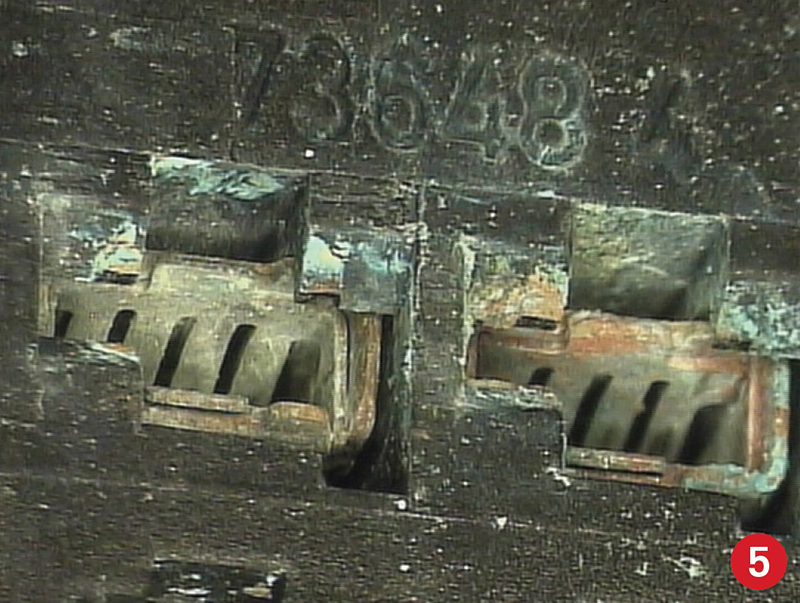
Note: In modern vehicles that are equipped with a ‘regulated’ or ‘demand-based’ fuel supply, the fuel pump is actuated by its own control unit with a pulse width modulation signal. A conventional digital multimeter is not sufficient to test these types of systems, as you simply measure the average voltage over a period here. In this case, you need an oscilloscope.