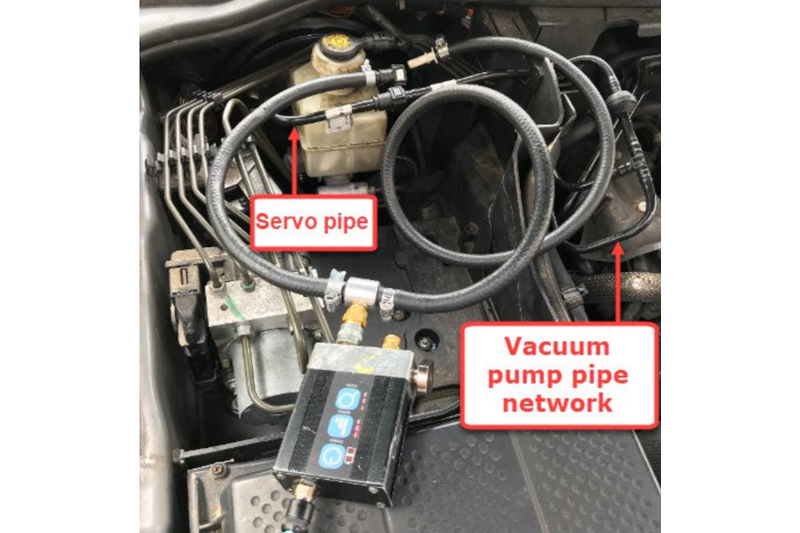
Technician Steve Smith looks at a brake booster failure on a 2007 Land Rover Range Rover Sport L320.
Customer’s description
When applying the footbrake, the brake pedal appears hard to press intermittently whereby more effort is needed in order to bring the vehicle to rest. Upon the next brake pedal use, the feel of the brake pedal and the effort required to stop the vehicle returns to normal. The symptom had been very intermittent regardless of temperature/road condition and had been evident for over two weeks.
Technical description
Although the symptom was described as “intermittent” by the customer, during my road-test I was alarmed at just how pronounced this symptom became!
When creeping (using the footbrake to hold the vehicle against the auto transmission) in slow moving traffic, I noticed the feel of the brake pedal became hard, with additional effort required to hold the vehicle stationary via the footbrake.
Whilst holding the vehicle stationary, I then noticed the vehicle begin to creep forward (even with the footbrake applied) where I then had to literally stand on the footbrake to stop the vehicle and switch off the engine! Here we suffered from a complete failure of engine assisted braking.
Ironically after restarting the engine the operation of the brake pedal returned to normal and I managed to limp back to the workshop. I think it goes without saying that the vehicle could not be driven until this fault had been rectified (much to the dismay of the customer!).
Diagnosis
With the customer complaint verified, the vehicle’s ID and specification were confirmed. The customer interview confirmed the vehicle had full service history with no accessories installed and no previously related repairs.
The basic inspection confirmed that visible brake servo pipework was secure and routed correctly, and that the brake fluid level was normal with no leaks. The engine oil level was also inspected and found to be normal. This may seem an odd inspection for brake assistance failure, however when we consider that the vacuum required for the brake servo is generated by an engine driven vacuum pump, it becomes quite relevant.
It is at this point we check for technical bulletins (software updates, initialisation, recalls and campaigns etc.). This is often a step in diagnosis that is missed, as it is very easy to get ahead of yourself during an investigation. On this occasion, we struck gold.
A little research soon revealed Land Rover had recalled a number of Range Rover Sport vehicles for the possibility of engine oil entering the brake servo or, sticking of the non-return valve in the closed position at the brake vacuum pump after a cold start.
Bulletins and known issues must be checked before diagnosis begins as it is mighty embarrassing to discover the fault you have been chasing for days is a known issue rectified by a software update or modified component (speaking from experience)!
Armed with this knowledge a quick check at our local Land Rover centre confirmed the recall mentioned above had been actioned and no further attention was required. We therefore must approach this concern as an unrelated fault following the necessary test procedures.
The description and operation data was referenced for in-depth knowledge of component functions. This knowledge is imperative when diagnosing any system and highlights the need for continual research and training.
Servo operation check
Following the typical operational check for a brake servo revealed an interesting result:
The usual test is to switch off the engine and drain the servo of any vacuum by repeatedly pressing the brake pedal until the pedal’s resistance increases and its travel is reduced. With the brake pedal pressed firmly down, re-start the engine and note how the pedal begins to creep or yield and pedal travel increases. This indicates normal servo operation, and for us this test was passed.
An additional test is to allow the servo to become fully primed with negative pressure, with the foot brake pressed switch off the engine. Maintain pressure on the brake pedal (applying a fixed pressure) and note any change in pedal travel. The pedal should remain fixed in this position if there are no vacuum leaks.
This test failed as the brake pedal began to return to the rest position, opposing the pressure I was applying requiring additional pressure from the driver (brake assistance was lost due to vacuum leakage).
The nature of such a safety related fault commands a thorough diagnostic approach where we can categorically confirm the component responsible for the failure whilst confirming other associated components remain serviceable.
Before diving in with this one I wondered how we could qualify what appeared to be a Servo failure using PicoScope. How about measuring Pressure against Time?
Luckily the Range Rover Sport utilises a quick-coupler within the relevant pipework between the servo and vacuum pump allowing for the insertion of the WPS500X pressure transducer.
Vacuum Pump Test
With the WPS500X inserted between the servo and vacuum pump the engine could be run to qualify not only peak vacuum (negative pressure), but also the time taken to acquire sufficient vacuum for brake assistance and the level of vacuum reserve during brake pedal operation. A concern with the servo efficiency was raised immediately:

With the servo drained of any vacuum, note how the peak negative pressure of -886 mbar was only achieved after 30 seconds of engine run time. Does this indicate an inefficient vacuum pump or a leak in the system?
My first thought here was to blame the measurement technique (which is good practice) as we must question our approach/connections etc. before confirming anomalies are real. All test hoses, couplers, the pressure tap and the pressure transducer were confirmed to be airtight using a hand-held vacuum pump, so qualifying our results above to be valid.
Clamping the test hose to the brake servo at approximately 55 seconds instantly improves our negative pressure by a further ‑126 mbar suggesting we have a leak in our servo. This also confirms our vacuum pump is capable of producing an awesome negative pressure of –1 bar.
Servo reserve vacuum testing
Given we suspect our servo to be leaking based on the vacuum pump test and operation check, further testing can be carried out to qualify the efficiency of the servo whilst measuring vacuum reserve. The waveform below now includes the brake servo vacuum level, brake pedal switch operation and a fuel injector to determine when the engine is running.
While peak negative pressure was only -682 mbar before the commencement of brake pedal activation, we can conclude that after only two pumps of the brake pedal our servo vacuum level is only measuring -177 mbar. This will manifest itself as very little brake pedal assistance for the driver during multiple brake applications in quick successions (stop/start driving or when manoeuvring).

Servo operation check
Test 1: Switch off engine, drain servo of vacuum, hold brake pedal pressed, start engine.
Test 2: With servo primed of vacuum, press and hold brake pedal and switch off engine while retaining fixed pressure on pedal.

Results
My apologies here as turning the engine off (and not switching ignition back on) results in a loss of the brake pedal signal. However brake pedal operation can be seen in the stepped look to the servo vacuum level.
Test 1 (Pass)
Here we can see how the servo vacuum improved slightly when the engine was started (after draining servo), but only to ‑184 mbar until the brake pedal is released. This gave a false ‘pass’ result as -184 mbar was sufficient to increase pedal travel, and give the impression the servo function and operation was correct!
Test 2 (Fail)
Here we have the application of the brake pedal with the engine on, followed by engine off. With the brake pedal held down the servo vacuum rapidly decays resulting in no brake assistance and opposition to the drivers input into the brake pedal.
Possible cause based on symptom and evaluations above is an internal leak within the brake servo, possibly via the diaphragm seam or internal valve assembly.
The action plan, based on initial evaluation, experience, and accessibility was to replace brake servo assembly (given no serviceable parts are available).
Confirmation of repair

Looking at the results above we can now confirm a satisfactory repair based on before and after results:
- Peak negative pressure of -859 mbar achieved within 16 seconds (before fix this was greater than 30 seconds).
- Our servo vacuum reserve was now -750 mbar instead of -177 mbar (with engine on).
- The servo now requires at least four pumps of the brake pedal instead of two in order to drain the servo of any vacuum (with engine off).
- Test 1 passed with exceptional servo vacuum (-750 mbar) with brake pedal on during engine restart.
- Test 2 passed with no vacuum decay (fixed at approximately -700 mbar) during brake on engine off.
Replacement of the above component confirmed a successful repair accompanied with the return of brake assistance under all driving conditions.
Additional comments
It occurred to me during the testing of this vehicle that brake assistance under single braking events was normal thanks to the efficiency of the vacuum pump.
The vacuum pump performance was sufficient to overcome the leakage and build vacuum within the servo during periods where there was no operation of the brake pedal. However the limitation of poor vacuum reserve revealed itself during periods of repeated braking such as creeping or manoeuvring the vehicle.
What concerned me with the symptoms above was how the servo ‘Operation Test 1’ resulted in a pass with just -184 mbar of vacuum/negative pressure available at the internal servo diaphragm!
Once again this confirms the need to carry out load tests in real-world environments while capturing live results that both qualify and confirm the test procedure.
There is a great feature within PicoScope that will help and protect all involved with such sensitive and safety related measurements, and it can be found under the Views menu tab.

When saving .psdata files (with your conclusive measurements and hard work) the time, date, PicoScope serial number and software version used to capture the data are also saved and can be viewed as follows:
With the .psdata file open, choose ‘Views > View properties’. The Properties view will now open alongside your waveforms displaying all the relevant capture information mentioned above, providing conclusive and documented evidence of diagnosis and repair.