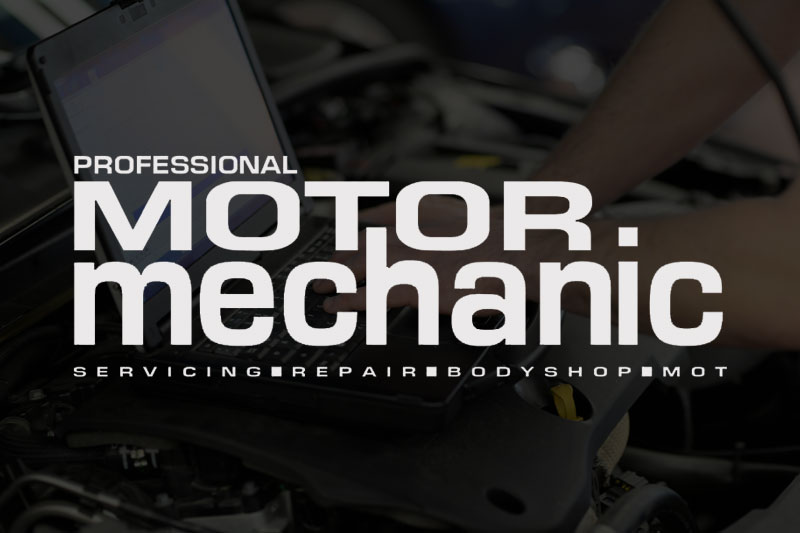
It used to be easy to work out which ABDS belt required replacement and which belt looked fine. When belts were made from a material known as chloroprene, it was relatively easy to identify wear from a visual check, based on the evidence of cracks on the grooved side of the belt.
Since 2005, Gates Micro-V® belts have been constructed from a material called ‘EPDM’ – well, that’s the abbreviated chemical name. The material used to make belts hard to change because today’s modern cars have more powerful engines, as well as extra components in the drive systems that make more demands on the belt.
EPDM is stronger, is suitable for a wider range of extreme temperatures (from -40°C to 140°C), and it is more durable at normal operating temperatures inside the engine. EPDM degrades and wears away gradually; it doesn’t crack. Therefore, an old belt looks very much like a new one these days, so the best way to estimate belt wear is to measure material ‘loss’.
Indicator assistance
The Gates ABDS Wear Indicator tool helps mechanics to gauge the level of wear on Gates EPDM belts. For example, if there is any side-to-side movement when the Wear Indicator is positioned inside the grooves, too much rubber compound has been lost and it’s time to replace the belt. Similarly, the tool can be used to gauge the level of wear on pulleys. Side-to-side movement indicates that it’s time to replace the pulley.
To continue this diagnosis support, Gates has developed a free App – ‘Pic-Gauge’ – that can be used to determine belt wear.
The garage scenario – noise abatement
Imagine a situation where the driver reports a noise from the Auxiliary Belt Drive System (ABDS) and it proves difficult to establish the source of the problem. The common causes of noise are misalignment in the drive system or incorrect tension. Alternative sources of noise include small foreign objects (dirt or road debris) that become lodged either in the grooves or on the back of the multi-ribbed belt. This can generate noise every time they make contact with the pulley.
Belt noise can also be caused by worn elements in the drive system and the best way to identify the source is to focus on the individual components. For example, the Torsional Vibration Damper is increasingly a feature of the modern ABDS.
Designed to compensate for crankshaft rotation speed fluctuations, they also dampen bell vibrations produced by a typical engine firing sequence. As TVD wear increases, so does belt vibration, belt noise and the potential for premature failure, which can even cause Synchronous Belt Drive System failure).
Ensure the noise is coming from the ABDS drive by removing the belt and the TVD. Start the engine without the ABDS belt – if the noise disappears, check each individual component.
Be aware
There is a rubber insert inside the TVD between the metal outer and inner ring. This damper operates under the resistance imposed by the belt. Never restart the engine without the ABDS bell in place, if the TVD is still fitted. A likely consequence is that the insert will shear-off, destroying the TVD. This is why TVDs must always be replaced if the belt has broken for any reason.
The ABDS wear indicator
All for one and one for all
The Overrunning Alternator Pulley (OAP) allows the alternator to “freewheel” or “overrun” every time the engine rotation speed decelerates. It compensates for engine speed fluctuations, while also providing the ABDS with a high degree of damping inside the system, so any loss of these damping qualities puts additional strain on the tensioner.
Typical signs of OAP wear include:
- A short ‘buzzing’ noise (1-5 seconds) from the alternator heard immediately after high revs (2,000 – 25,000 rpm)
- A short ‘chirp’ during engine start-up or shut down
ABDS belt failure due to cracking
A worn OAP performs like a solid tensioner: It has no damping capabilities and it causes the belt to slip across the surface of the pulley at any engine revolution speed change and the typical firingengine speed fluctuations. Once it has been established that the OAP is to be replaced it should be noted that:
a) Special tools are essential for the job
b) OAPs are not all purpose fit, but ‘tuned’ to a particular application
c) Never replace an OAP with a solid pulley
d) Never replace a solid pulley with a non-prescribed OAP
Finally, mechanics must consider the potential implications for wear to other components in the drive system. For example, the tensioner will have been working much harder to remove the additional vibrations caused by the failure of the OAP, but the length of time this process has been going on is unknown – as is the amount of damage that might have been caused. That’s why Gates always recommends a system overhaul, rather than the replacement of individual components.