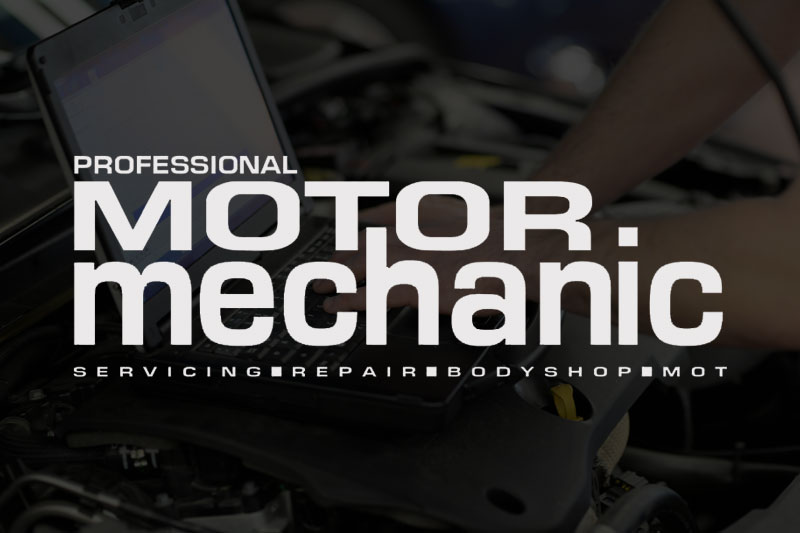
It goes without saying that continuing education is critical to success. Knowing the latest repair trends can help improve service turnaround, avoid comebacks and increase overall customer satisfaction and the same can be said for seemingly simple repairs. Whether complex or simple, maintaining best practices can help eliminate a potential mis-diagnosis or part failure.
Best practice tips
1: Compressor preparation prior to operation
Would you expect a rebuilt engine to run properly if it wasn’t ‘pre-lubed’ or only had one quart of oil in the crankcase on initial startup? Of course not. The same can be said for a compressor. In order for the compressor to operate correctly on startup, it must have the accurate amount of oil inside and be turned over, by hand, using the right compressor turning tool, so all the components inside are pre-lubed.
Failure to complete this pre-lubrication process prior to compressor operation can lead to noise complaints and premature failure. There are two types of compressors – one with oil and the other without. Compressors with oil (pre-lubed) need to have the new oil drained and the correct oil amount and type reinstalled. Dry compressors, or compressors without oil, need to have the correct amount and type of oil added prior to compressor operation. Regardless of compressor type, instructions included demonstrate how to correctly lubricate and rotate the compressor prior to operation.
2. Flushing the A/C system
When flushing the A/C system with chemicals ensure no residual flush is left behind. If there is, it could dilute and contaminate the compressor lubricant, leading to compressor noise and premature failure. If you are flushing an A/C system, it is critical you use the approved OEM equipment, flushes and procedures to help minimise concerns with potential residual flush.
3. Use recommended lubricant
It seems simple – you just use the lubricant type recommended in the instructions that come with the new compressor. Unfortunately too many compressors still fail every day by having the wrong lubricant.
Without the correct lubrication, the compressor has little or no chance of longterm stability. There are a number of lubricant types on the market depending on the A/C system with PAG oil the most common. It is important that high quality PAG oil is used and the technician follows the directions included with the new compressor so the correct type and amount of oil is utilised, and in the proper location.
Ester oils are also available, but we don’t recommend their use as they can break down under high heat conditions, resulting in lubrication and compressor failures.
Some examples for you
The picture below shows the rotating assembly of an A/C compressor, which was destroyed by lack of lubrication at start up. Notice the gun metal blue colour of parts which over-heated and seized, causing a catastrophic failure.
The image below shows a destroyed reciprocating assembly from a compressor that failed due to lack of lubrication. The lubricant removed from the compressor was thin (had poor viscosity) and had a chemical flush odour.
The image below shows the inside of a failed compressor, with lubrication that has become a thick, black sludge. Ester oils, not recommended for use in Delphi compressors, can experience thermal breakdown in high heat conditions, and form sludge like this.
When lubricating compressors with a crank case plug (like the one pictured below), be sure to remove and install all lubrication through this opening so the oil can get directly to the rotating assembly inside the compressor.
Why and when do you have to change the compressor?
■ Lack or excess of refrigerant oils
■ Internal corrosion
■ Lack of servicing (regular changing of receiver drier)
■ Circuit blocked – receiver drier clogged and/or expansion valve blocked
■ Incorrect or no flushing of system when fitting new compressor
■ Electrical problem in the clutch
Faulty compressor can mean:
■ A/C system does not operate at all
■ Potential damage to other A/C components