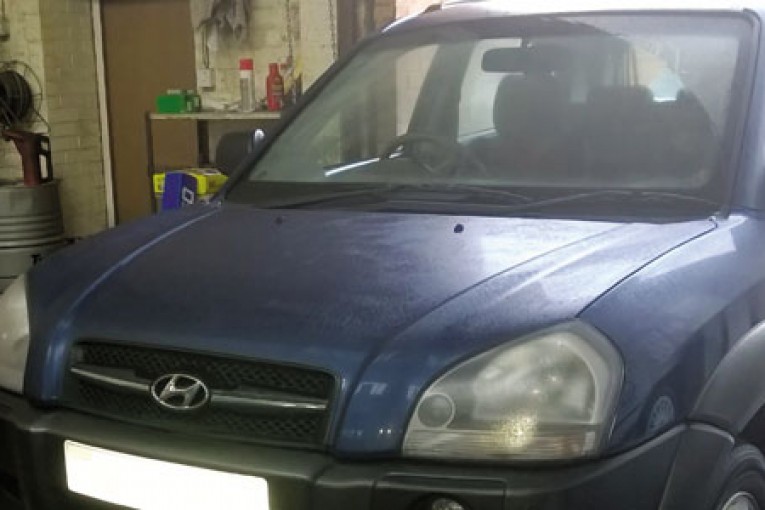
MODEL: Hyundai Tuscan 2.0 2WD Petrol; 2007
RECOMMENDED LABOUR TIME: 5 hours (Gearbox remove, clutch replaced, gearbox re-fitted)
“It’s important to ensure that the release bearing is always replaced if the clutch and/or DMF are worn out.”
The Hyundai Tucson has been around since 2004 and is now into its second generation. Since 2004 it has had minor trim improvements but in 2009 a completely new design was launched. It has various engine and transmission options and trim options to suit.
Compact SUVs are a popular choice of vehicle and the chance of one arriving at an independent workshop is highly likely. The vehicle may be fitted with alloy wheels so, before starting the repair, make sure that the locking wheel nut key is available. For this repair we used a two-post ramp, an engine support, two long axle stands and a transmission stand and cradle.
Open the bonnet and first remove the battery, stowing the battery cables safely. Once this has been done the battery tray can also be removed. Disconnect the air flow sensor cable and stow safely out of the way.
Disconnect the air duct and hose assembly and remove. Remove the air cleaner assembly which will expose the top of the gearbox. Disconnect the reverse light and speed sensor connectors and stow.
Remove the top nut holding the clutch release lever in position and remove the two bolts that hold the external slave cylinder in place on the top of the gearbox .
Stow the lever and slave cylinder safely out of the way.
Remove the clips that hold the gear linkage cables and pop them out of position. To make access a little easier to the top bell housing bolts, remove the horse shoe clip that holds both gear link cables into the retaining bracket and stow the cables safely. Remove the four top bell housing bolts, making sure you take note of the different sizes so they are installed correctly when refitting the gearbox. Install the engine support and then remove the top gearbox mounting bolts and mount. Raise the vehicle carefully.
Remove the plastic under-tray and drain the gearbox oil. Remove both front wheels and remove the N/S drive shaft nut. Remove the bolts from the N/S and O/S bottom ball joints and disconnect both of them from position. Remove the N/S drive shaft completely. The O/S drive shaft can just be removed from the gearbox side and supported safely by using bungee ties.
Support the steering rack using two bungee ties and remove the two bolts and bracket that hold the rack to the rear gearbox mount.
Support the sub-frame using the long axle stands and remove the subframe bolts. Remove the two centre bolts from the front and rear gear box mounts.
Carefully lower the sub-frame and move completely out of the way.
Support the gearbox using the transmission jack and cradle, making sure that all the wiring harness and pipes are clear from the gearbox. Remove the remaining bell housing bolts, separate the gearbox from the engine and carefully lower the gearbox to the floor. Remove the worn clutch and release bearing.
Check the flywheel for signs of heat stress or excessive wear. If the surface of the flywheel is to be skimmed, make sure that the same amount is taken from the clutch bolting surface. Failure to check and rectify these areas may cause the clutch to operate incorrectly. Clean the bell housing and remove any debris. If any oil leaks are visible then these must be repaired before refitting the gearbox. Before fitting the new clutch disc, make sure the input shaft is clean and free from any wear.
Put a small dab of high melting point grease (not a copper-based product) on the first motion shaft splines and make sure the new driven plate slides freely back and forth. This not only spreads the grease evenly but also makes sure you have the correct kit. Wipe away any excess grease from the shaft and driven plate hub. Using a universal alignment tool and checking the driven plate is the
correct way round (note “Getriebe Seite” is German for “Gearbox Side”), the clutch can be bolted to the flywheel evenly and sequentially.
Make sure any dowels have not become dislodged or damaged and replace any that have. Install the gearbox and make sure the bolts are secured and all mountings are refitted before removing the supporting transmission jacks. Refitting the remaining components is the reverse of removal.
For the latest in online support log on to www.repxpert.com.
DMF CHECKPOINT ARRIVES
To accurately check if a DMF needs replacing due to wear, mechanics need to be aware of the correct operating tolerances and bolt torque settings that are unique to each DMF. You can now simply enter a LuK DMF part number into the DMF CheckPoint App and instantly see all of the information you need to be aware of before carrying out a professional repair. This includes:
■ Maximum Freeplay using the DMF special tool (degrees)
■ Maximum Freeplay without using special tool (no. of ring gear teeth)
■ Maximum Rock with or without using the DMF special tool (mm)
■ Friction control device details
■ Do the bolts need replacing and are they included with the DMF?
■ DMF bolt torque settings
Available to download from iTunes for Apple devices and Google Play Store for Android, DMF CheckPoint is an invaluable tool for technicians who regularly service and repair modern clutch systems that include a DMF.