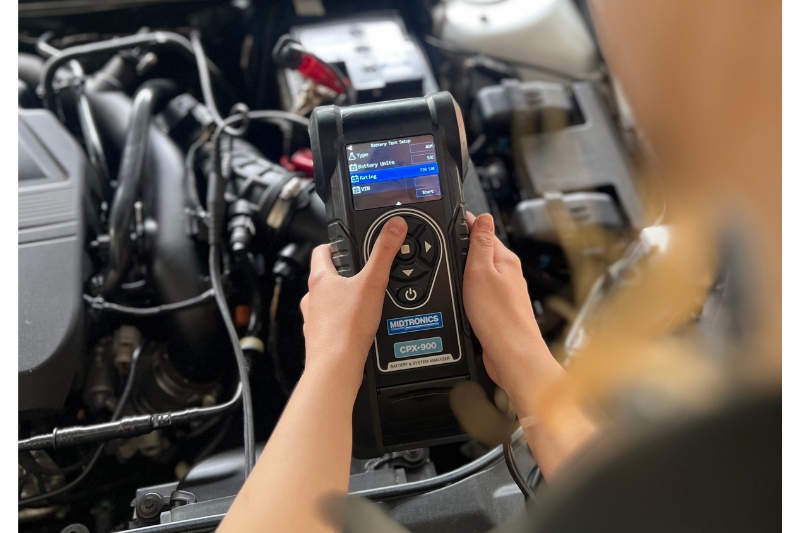
The winter can be a time when motorists fall foul of the increased risk of roadside breakdowns and battery related non-starts. As a result, independent workshops are inundated with car battery issues. Here, Rotronics offers some advice on what you can do for your customers.
The inevitable cold of this time of year will significantly affect a battery’s performance and, in extreme temperatures, this can mean as much as a 50 per cent dip.
There are increased power demands on a vehicle due to the darker nights; lighting, heating systems, electrics, heated seats and de-misting windows, all together, put an excessive drain on the vehicle’s battery, so charging is vital. In a routine service, the brakes, oil, tyres, exhaust and all fluid levels are checked as standard, but for some reason the battery is often overlooked yet it is arguably the single most important component in the vehicle.
A 12V battery is considered fully charged at around 12.7 Volts. In use voltage should always be above 12.4V to prevent sulphating of the cells (the most common cause of battery failure) reducing performance and serviceable life of the vehicle’s battery.
We recently undertook a survey at Mechanex Surrey where only two in 10 workshops routinely undertook a battery test, rising to 7 in 10 when a battery fault was suspected.
Traditionally the focus on the 12V battery has been its cold cranking (starting) performance but with most ICE vehicles having start stop-systems fitted combined with increasing electrical demands, the ability of the battery to handle loads when the alternator is not engaged is critical. The ability to check this ‘reserve capacity’ is a valuable addition and should be considered when investing in diagnostic battery testing equipment.
Test and charge
Rotronics, the UK partner for CTEK and Midtronics battery management technology, is an industry leader in battery maintenance and service solutions and our team always recommends that independent workshops offer a simple battery ‘Test & Charge’ service for every vehicle that enters their premises. You can then identify all opportunities in supporting your customers and their vehicles with just a few simple steps:
- Test every vehicle’s battery using a diagnostic battery tester, as part of your winter inspection programme.
- Notify the customer/owner of the outcome, stating that the battery is: a) Good – fully charged (no action required); b) Faulty and needs replacing (offer replacement).
Offering this service helps you to show your customer how to prevent an issue before they’re standing at the side of the road in the dark, the snow or rain. It also presents you with additional revenue potential by giving you the chance to identify a faulty battery and, more importantly, the opportunity of replacing it.
Rotronics works with independent workshops to deliver simple, effective battery and electrical system testing processes that integrate into every-day workshop practices. Payback can be demonstrated through the additional revenue earned from testing, charging and battery sales. Rotronics each workshop customer is given the expertise and know-how to maximise fault diagnosis and increase customer service within their own workshop.
The programmes are designed around each business’ individual requirements and Rotronics’ knowhow can help your business to extend the life of a customer’s battery, as well as identifying those batteries that are likely to fail during the winter. This enables technicians to accurately diagnose and proactively inform customers of any impending defect or failure before it impacts them in their daily lives.
Additionally, the unique ROBIS Rotronics Battery Management Programme (ROBIS) keeps a full record of use and allows workshop operators/owners to monitor and track opportunities and upselling potential as part of everyday service and inspection activities carried out by their technicians as well as enabling a full battery condition report to be generated and printed out or emailed to the customer – a major step forward in customer service.
Ken Clark, Managing Director at Rotronics, says: “Battery failures and nonstarts create very expensive, time-consuming inconvenience at this time of year. The majority of the issues faced can be prevented with a little care, maintenance, and preparation, however.
“Workshops can be preparing well in advance for the onslaught of the chilly weather and dark nights. The best time to prepare for the next winter’s battery problems is in the winter itself or straight afterwards when all the issues and costs are at the front of your mind.”
Four steps to success
The Battery Management Programme from Rotronics has some simple steps to help you and your workshop team cope with the effects of winter:
1. Inspect
Always check batteries for signs of damage. Look for signs of corrosion, excessive electrolyte staining and gassing. Make sure that the hold down clamps and terminals are secure and free from dirt or corrosion; in the unlikely event the battery is not maintenance free, make sure that the electrolyte levels are checked and maintained.
2. Test
- Every vehicle battery that enters the workshop should be tested including batteries that have been jump- started. A jump-start is only a temporary fix which, in many cases, is hiding an underlying problem.
- Use the best diagnostic tester you can afford. As a minimum you will need to be able to advise the cold cranking (starting) capability of the battery. Whether it is good, in need of charging or requires replacing. Ideally the tester should be able to provide a printout of results that can be shared with the customer.
- Reserve capacity (RC) performance of the battery is increasingly important. This is the ability of the battery to run electrical consumers when the alternator is not providing energy. This is relevant with start stop vehicles (and also EV auxiliary batteries). A tester that can provide a RC test is increasingly useful.
3. Charge
It is good practice to connect the vehicle battery to a charger during service. Not only will it charge and condition the battery but it will help compensate for battery drains encountered during service work from having ignition on or even opening and closing doors. Use a charger that is designed robustly for workshop use and has a sufficient power output. We would recommend a minimum of 25A for routine work. More if diagnostic work is planned.
4. Check
Once the battery is in a good, healthy, and charged condition, check that the charging system is also performing as it should.
- Ensure the starter system is working correctly.
- Check the alternator output.
- Ensure there are no excessive drains present, which can cause batteries to go flat very quickly.