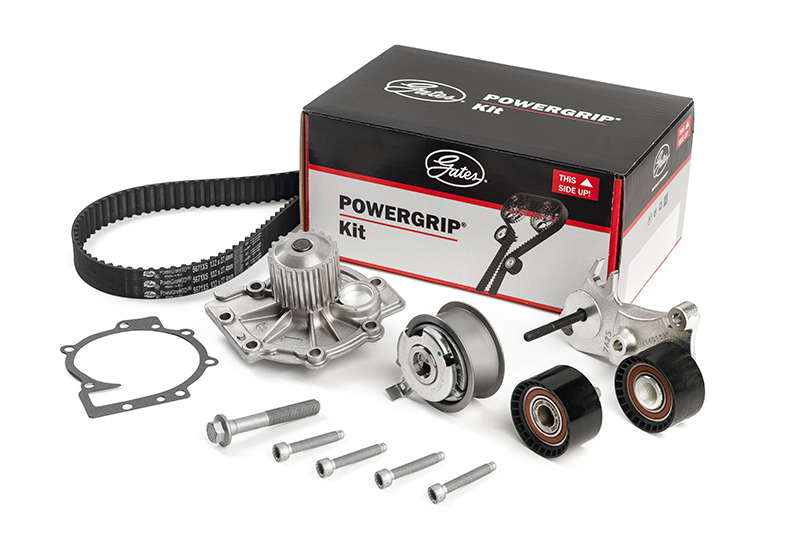
In this month’s Belt Focus, Gates explains how to avoid some common causes of premature drive system failure.
If the automotive drive belt system includes a water pump, it is good workshop practice to fit a new water pump whenever the belt is changed. That’s why Gates always recommends the fitting of a new water pump as part of a Gates belt kit at every scheduled replacement.
Analysis of claims data by Gates found 80% of claims related to water pumps were caused by failure to follow the recommended installation procedures. Over 50% of claims related to ‘coolant’ in general. Just under 30% were caused by improper use of sealant on water pumps already supplied with either a gasket or O-ring.
The common issue was consequential damage to the mechanical seal. Let’s examine how this contributes to premature water pump failure.
The mechanical seal
A mechanical seal generally consists of two seals/rings:
- Static seal/ring
- Dynamic seal/ring
The static seal assembly is fixed into the water pump housing and does not rotate (static). Spring pressure enables it to move along the axis of the bearing/impeller shaft. A combination of spring force and hydraulic pressure from the sealed coolant ensures the seal faces are pushed together. This prevents leakage between the shaft and the water pump housing. The dynamic seal assembly is secured to the shaft. Therefore, the dynamic seal rotates with the pulley-driven shaft.
The static and dynamic seal faces are precision machined to strict tolerances of ‘flatness’. Inside the assembly, both seal faces are pushed together, which means that if the seal faces rotate against each other in a dry condition – without any form of lubrication – the combination of face friction and heat generation will create wear. This leads to premature failure because once the seal face has been damaged, any score marks will act as ‘leakage paths’ for the coolant.
Protecting the mechanical seal
A film of coolant, introduced between the dynamic and static seal, prevents damage through face friction and heat generation. ‘Priming’ the mechanical seal in this way provides lubrication and allows cooling between the seal faces. This film creates a micro-gap, which is maintained by the spring and the hydraulic forces that push the seal faces together, while the pressure of the film of coolant between the seal faces acts to push them apart.
This combination ensures a perfect seal between the static and dynamic rings.
Priming a mechanical seal
Submerge the water pump, impeller-side downwards, into a clean container of coolant. Ensure the coolant has been recommended by the vehicle manufacturer (never re-use old coolant, as particles or contaminants in suspension will cause premature failure). Rotate the water pump pulley about 10 times by hand, to draw coolant between the faces of the mechanical seal. Alternatively, when fitting a new water pump to the engine, refill the cooling system with new coolant and rotate the water pump pulley about 10 times by hand. This draws coolant between the faces of the mechanical seal.
Weep hole leakage
The weep hole is a small, drilled hole, usually found at the lowest point on the water pump when in the mounted position. A small amount of leakage from the weep hole is normal, particularly at start up, following installation. Not all water pumps have a ‘weep hole chamber’, but if there is one, its role is to contain and evaporate the leaked coolant. Heavy leakage means an internal seal has failed.
Discolouration and bleed marks around the weep hole and/or on the water pump body itself are signs that the mechanical seal has failed through contamination.
Liquid sealant issues
A new water pump is usually supplied complete with a gasket, which may be paper, metal, composite or an O-ring. The gaskets supplied are designed to be the only seal between the water pump and the engine block. Never use a liquid sealant in addition to any of the provided gaskets. It is unnecessary and will infringe the terms of the warranty.
If use of sealant is recommended by the vehicle manufacturer, use only the recommended size of bead. Any excess may be sucked into the cooling system, causing premature water pump failure.
Once the cooling system has been flushed and the mechanical seal on the water pump has been successfully primed, installers can feel satisfied that several common causes of premature drive system failure have been avoided. Once the WP is fitted, the drive system can be re-built using the belt and any metal parts supplied as part of the Gates belt kit.
Good workshop practices
✓ DO flush the cooling system properly (a Gates Power Clean Flush Tool 91002 is ideal)
✗ DON’T rotate the water pump manually, in a dry condition
✓ DO prime the mechanical seal
✓ DO check expansion bottle and/or radiator for signs of contamination that could lead to blockages
✓ DO insist on the use of a good quality coolant as recommended by the vehicle manufacturer whenever the cooling system is being refilled
✗ DON’T mix different cooling technologies. It will cause a chemical reaction, destructive to the mechanical seal. It can also create gels, which coagulate and block the system
✗ DON’T use tap water as a coolant dilutant
✗ DON’T apply sealant to a water pump that’s supplied with either a gasket or an O-ring
New Gates Video
Gates has produced a new video entitled ‘How to Install a Water Pump Correctly’. It explains the role of the internal mechanical seal and highlights the reasons why its surfaces must be ‘primed’ by a thin film of coolant as part of the installation procedure.
Specifically designed for drive system professionals, this informative video is designed to help reduce the number of premature water pump failures caused by common installation errors.
It urges installers to resist any temptation to spin the water pump’s impeller, manually, once it’s been taken out of the box. Dry running leads to a damaged mechanical seal and premature water pump failure.
To watch the video, click here.