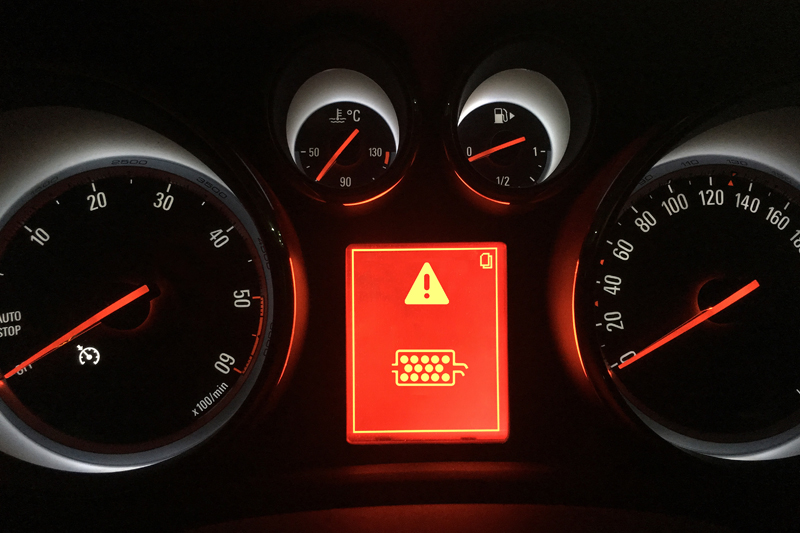
Ross Kemp of Scantec Automotive highlights a recent case where a DPF fault code turned out to be far more complicated than it first appeared.
We were recently tasked with investigating a DPF-related fault on a 2014 Seat Alhambra with a CFFB engine. The vehicle was brought to us by the owner via another workshop. The referring workshop had run some tests and advised the owner that the vehicle required a new DPF, but to have us at Scantec run some tests on the vehicle first to confirm the faults before going ahead with the replacement.
When the customer dropped the vehicle to us, they explained that they had an ongoing issue with exhaust smells inside the cabin and had previously had leaking exhaust gaskets replaced. Unfortunately, the smells continued with intermittent faults being logged relating to the DPF system.
Our initial fault analysis confirmed one fault code stored and present in the engine control module:
P246300 – Particulate Filter Restriction – Soot Accumulation.
Quick data checks/live data analysis suggested that the DPF pressure was around 30 mBar at idle and some 175 mBar at fast idle, confirming why the above fault code was being triggered. After checking the data further, there was the suggestion that the last DPF regeneration was only 7km ago, yet we had a calculated soot content of over 55g.
Out of sync sensors
After checking the pressures manually, we discovered that although the pressures were clearly too high, there was a clear difference between the pressures reported by the DPF pressure sensor and the actual/physical pressures measured at the sensor. This confirmed that the pressure sensor was not calibrated and required replacement.
Following the replacement of the DPF pressure sensor, we continued our testing routine by initially following the manufacturer’s test plan for fault P246300. However, on entering the test plan, the suggested course of action was to carry out a forced DPF regeneration.
Now, not being a fan of forced regenerations and knowing what we already knew regarding the soot content and pressures, it was highly unlikely that the test plan would lead us anywhere other than a recommendation to replace the DPF.
The road test
We decided at this stage to carry out an extended road test while monitoring the data to ascertain whether regeneration was attempted by the engine control system, and if so, then to what effect. Before a road test, we always carry out a quick vehicle check over. On this occasion, it paid off as we found that the engine oil was overfilled by approximately 1L. After checking the service history with the owner, we confirmed that the engine was in fact due an oil change, so for the owner’s sake and ours, we carried out a quick oil and filter change before proceeding with the road test.
During the road test, it was almost immediately apparent thanks to the data that the engine control system had requested and adopted a DPF regeneration strategy. This was clearly visible when monitoring exhaust gas temperatures, but we also quite clearly noted exhaust fumes inside the cabin, so much so that it was uncomfortable to drive. Despite this being uncomfortable, we were able to drive the vehicle for long enough to confirm that DPF regeneration was almost permanently active throughout the drive, yet it seemed to have little to no effect on the pressures and/or the soot calculations.
Regeneration game
Now, regardless of the science, myths or magic potions, DPF regeneration, the conversion of soot to ash, is achieved automatically/manually over a certain temperature. In this vehicle’s case, it was clear that the control system was achieving those required temperatures during the test drive as it should do.
So, why did the pressures not drop? Did we have a defective DPF in some way? Was the referring garage right to suggest the DPF required replacement? After all, we had no other faults being logged other than that of a DPF restriction, and the manufacturer test plan also suggested that we should replace the DPF.
Is the DPF the problem?
However, the above assumption is seriously flawed. An important factor to consider is that this vehicle’s engine control system does not utilise a DPF differential pressure sensor – it uses a single measurement pressure sensor. Therefore, the so-called ‘DPF pressure sensor’ in this case would be more aptly called an ‘exhaust pressure sensor’ as it is actually measuring the complete exhaust system pressure.
When you consider this and the fact that this vehicle also utilises an SCR Cat, it opens up the possibility that the pressures being seen by the pressure sensor could technically be anywhere in the system and not in fact due to a DPF-related issue at all. Opening up the exhaust system and carrying out further pressure tests and borescope inspections confirmed nearly all of the pressure identified was actually due to a failed/blocked SCR Cat.
After replacing the SCR Cat, resetting all systems and retesting the vehicle, we found that the DPF (or in this case, exhaust) pressures to be around 3 mBar at idle – confirming that there had never actually been a DPF issue.
Conclusion
So, we had discovered what in our opinion is a design fault, or perhaps a cost-saving exercise, in only using a single pressure measurement sensor. Due to this ‘design’, any developing faults in the complete exhaust system after the DPF will automatically be blamed on the DPF, causing unnecessary DPF regenerations and associated heat, increased fuel usage, ever increasing engine oil level, and if not carefully considered, unnecessary DPF replacements. We were also fairly confident that the demise of the original pressure sensor was caused by the excessive heat from the unnecessary regenerations being forced back up a single pressure pipe to the sensor due to the blockage in the SCR Cat.
Understanding the system design and the associated issues that may arise from said design and not blindly following manufacturer test plans (in this case) was the key to a correct diagnosis and avoided any unnecessary parts replacements.