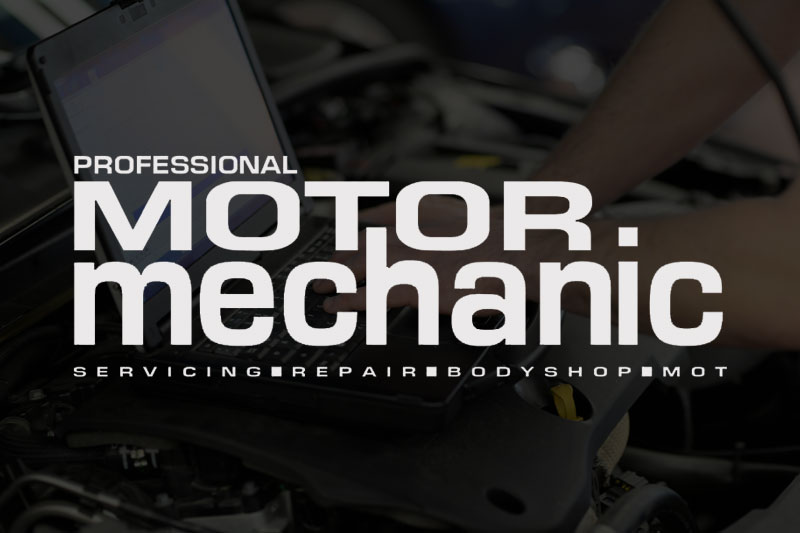
Diesel particulate filters have been fitted to diesel cars for around 12 years now and have received a mixed reaction from the industry. The modern diesel is a much more sophisticated affair than its 1980’s predecessor and the impetus for the technology that has given us smooth, powerful, clean diesels in our cars today has come from emissions regulations. It is unfortunate that in order to meet these increasingly stringent regulations, diesel engine manufacturers have had to turn away from improving the combustion process to using treatment of the exhaust.
NOx or particulates?
As can be seen on the chart (below) it is the reduction of oxides of nitrogen and particulate matter (PM) (soot) that has become the battle ground for the manufacturers. NOx is formed when the combustion temperatures exceed 1,800degC and the oxide formed depends not only on the temperature but the length of time the heat is applied.
Most manufacturers have used Exhaust Gas Recirculation (EGR) as a method of reducing NOx formation. This works by re-introducing the relatively inert exhaust gasses as a percentage of the total intake, which has the effect of slowing down the combustion process and reducing the peak
temperatures in the combustion chamber. Unfortunately it has side effects.
Reduced thermal efficiency
A longer combustion means the heat energy has more time to pass into the cooling system, which means that a more effective cooling system has to be used. The injection timing also has to be advanced to account for the prolonged combustion, causing some loss of mean torque and thermal efficiency; consequently fuel consumption increases.
Increased soot output
By reducing the amount of excess air available for combustion there is more chance of incomplete combustion. This is normally partially rectified by improved mixing of the air and fuel but there will still be a net increase in particulate matter.
Diesel Particulate Filter
The purpose of the filter is to trap any particulates produced by incomplete combustion. The filter consists of a ceramic monolith, sometimes incorporating an oxidising catalyst which converts any CO and HC into CO2 and water.
A Citroen DPF: The particle filter is shown in the grey mesh area (far left) while the oxidising catalyst is the cream item (far right)
As the gasses pass through the porous ceramic particle filter, the particulates are trapped. As long as the temperature remains high enough, the carbon particles will react with NOx to produce CO2 and Nitrogen; this is known as passive regeneration. Under low load conditions the temperature drops and soot particles build up in the filter. The degree of restriction to flow is monitored by a differential pressure sensor and when required, the DPF is put into a regeneration mode.
Regeneration
Regeneration can only happen when the running conditions are suitable. The engine must have been travelling at mid-throttle for a period of time as the computer will try to anticipate a steady situation such as a motorway journey. Regeneration occurs by raising the temperature of the DPF to around 550degC and providing it with extra oxygen. To do this, the computer reduces the EGR system contribution intake to 0%, ensuring maximum excess air and the electrical consumers such as the heated rear screen, glow plugs and fan unit are turned on to load the alternator.
Extra fuel is injected into the cylinder in a late or post injection, which sends hot gasses into the oxidation catalyst and DPF, raising its temperature sufficiently to cause the carbon to react with the excess oxygen and NO2 supplied by the engine.
A successful regeneration process will continue until the pressure differential across the DPF drops to an acceptable level. Should the driving circumstances change, for instance the car comes to a halt, the regeneration is abandoned until the conditions once again become suitable.
Problems arise when successive regenerations are abandoned and the soot levels build to a point where the DPF becomes restricted – cars that drive around in town traffic or for short journeys are susceptible to this. When it happens, the driver is notified by a warning light, and the vehicle should be taken on a journey that allows regeneration to happen (this should be described in the owner’s manual). If the warning is ignored, then a second warning appears or the vehicle may go into limp home mode. This is when the technician must force regeneration.
‘Forced’ regeneration
Forced regeneration can only be done with a scantool and certain conditions must be met, depending on the vehicle. Some forced regenerations can only happen when the vehicle is being driven so details of the process have to be investigated. Standing regeneration can be a noisy affair as the engine revs to 4,000rpm for up to 4 minutes then to 2,000rpm for a further 4 minutes.
The heat generated causes unusual burning smells so it is better performed with the vehicle raised and a fan blower providing some air movement underneath the vehicle.
Diagnosis
There have been many cases of DPFs being replaced only for the vehicle to return with the same problem. It is essential that the technician uses his or her skills to investigate all areas around combustion efficiency before condemning and replacing a DPF.
Eolys
Eolys is a pre-treatment used by Peugeot/Citroen to make regeneration of the DPF more effective. It reduces the temperature at which carbon particles react with oxygen from around 550degC to 450degC. The active ingredient is an iron and/or cerium rich compound in solution with a combustible solvent. A small quantity is added automatically from a separate tank to the main fuel tank every time the vehicle is refuelled.
The active ingredient goes through the combustion process and is deposited in the DPF. Eventually the DPF will become blocked with the deposit and will need to be replaced – the life span of a DPF fitted to this system ranges from 75,000 – 120,000 miles depending on the model.
Selective Catalytic Reduction (SRC)
There is another approach to reducing the NOx. As previously discussed in this article, EGR reduces the efficiency of the engine and promotes particulates. Future Euro regulations call for not only a reduction in PM measured by mass but also for a reduction in the number of particles.
The reason for this comes from research into the effect of nanoparticals, which has shown that, unlike larger soot particles, these tiny carbon particles are not expelled from the lung and can cause serious health problems. SCR is an alternative to EGR which addresses this problem. It has been used on commercial vehicles for some years now and is a proven method of reducing NOx.
It is now used by VAG and Mercedes on their passenger cars. The trade name is ‘AdBlue’ and it consists of a solution of 32.5% urea and water contained in a separate tank on the vehicle. It is not a fuel additive but instead is injected into the exhaust after the oxidising catalyst and DPF. When the urea meets the hot exhaust gasses it decomposes to ammonia (NH3) and CO2. The ammonia then reacts with the oxides of Nitrogen in a second catalytic converter to form Nitrogen and water. The advantage is not only a reduction in NOx of about 85%, but a reduction in the use of EGR means a more efficient combustion, reduced PM and improved fuel consumption.
The future
Most of the diesel emissions technology of recent years has dealt with the symptoms and not the problem. New technological approaches to the problem include even higher injection pressures and controlling the combustion process by water injection or emulsified fuels. This presents an uphill battle for manufacturers struggling to meet the increasingly stringent emissions regulations.
Thanks to lee@techblue.co.uk for use of the images.