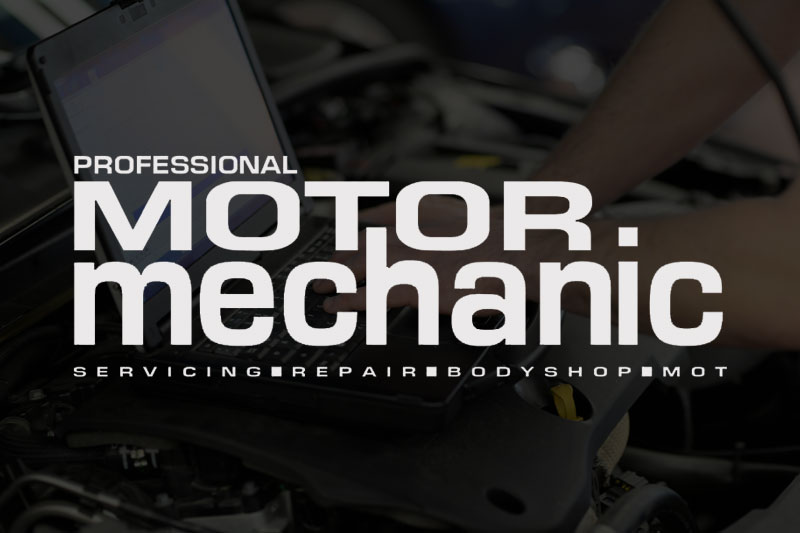
Recently we had a visit from a Peugeot 206 that arrived at the workshop with a stallingcomplaint. The owner explainedthat when she came to a halt on a roundabout or in stationary traffic, after 10 seconds or so the engine would start running ‘lumpy’ and then cut out. The car had been taken to a number of garages where various parts had been changed but the problem still existed.
The Peugeot engine
First things first, I took a look under the bonnet and all seemed to be in order so it was time to take the car out on the road. I didn’t have to wait too long to notice the problem myself, however after coming to a halt the car restarted straight away. In order to investigate further I decided to take the car on an extended test drive to see if its performance was affected in any other way. Although the car did perform well it was slightly sluggish at the top end so I made sure to double check that the cutting-out was still occurring before taking the car into my workshop to have a proper look.
Back in the workshop
Using the scan tool first, no DTCs were logged. I then checked the serial data and, again, all appeared to be as it should. The 206 is a car I see on a regular basis, mainly for reboot maintenance, so at this point I decided to look at the basics in a little more depth. The air filter and air intake pipes were checked, and despite their clean appearance, the air filter looked like it needed replacing. The car stalled whilst in my workshop and appeared to be running ‘lumpyish’ before cutting out.
The fuel pressure test
With scope in hand my attention was now drawn to the 12 volt power supply coming from a multi-purpose relay which is mounted under the ECU. Removing the ECU usually uncovers a damp and dirt trap; this is exactly what I found so needless to say there was a bit of cleaning required. After disconnecting the relay, checking the pins and cleaning the sockets the connection was sound and the 12 volt supply was all in working order. I then restarted the engine, allowing it to run, but once again the engine began to sound lumpy and cut out. This was strange but I could now tell that the engine did not have an electrical supply problem. The earth path was checked for possible high resistance (which can cause running problems) but there were no troubles there either.
It was now time to move on to the idle air control valve, throttle position sensor, the map sensor and the infamous Lambda sensor. I checked the 5v first and all was sound with that.
Time for a rethink
The next check was the mapping sensor and this test proved to be the breakthrough that I was looking for. This sensor is a ‘digital type’ and is much faster than the old analogue type. With the engine running I attempted to open the throttle fully. The engine RPM rose and then gradually fell before cutting out as if it had run out of petrol. After conducting the test three times, the output of the mapping sensor frequently rose accordingly with the engine RPM, suggesting that there was no problem in this area.
Now I finally had something concrete to go on: fuel flow and pressure regulation. This was a very strange situation as fuel supply problems normally occur in the power band, which would lead to a severe drivability problem – lack of power. However, I was not entirely happy with the top-end performance so felt it was time to carry out a test on the fuel pump.
Testing the fuel pump
Firstly I went to look around the fuel pod for the pressure regulator, but it was nowhere to be seen!The rail had both supply and return pipes fitted, so the only other place it could have been fitted is in the fuel pump return. These pumps are fitted in the tank underneath the rear seat and I intended to carry out a two-fold test: the first was to connect the fuel pressure gauge to the return flow; and the second was to connect the scope to the 12v supply and also use the ground wire to the pump.
Fuel pump
With the engine running and the fuel pressure reading under 2 bar, the voltage was stable at 12.8 volts, however the fuel pressure started to drop rapidly and the engine started to run lumpy although the voltage still remained stable. Once the car cut out, the voltage went down and shut off the relay (as it should). This test was carried out three times.
I had now reached my decision that the fuel pump was at fault and I would remove the pump for a more thorough investigation. I couldn’t see any damage or blockage – the regulator was fitted to the pump on the return circuit and was of a ‘fired-type’ and the pump speed was varied to generate the pressure. Finally I had something positive to report to the customer!
I replaced the fuel pump with a quality Bosch replacement, the car was then retested and the problem was solved.
Every so often a problem job like this will come knocking where there are no DTC’s logged and the fact that it turned out to be a faulty fuel pump was very strange indeed. In the past I have often come across fuelling issues – which usually result in a lack of power or non-starters – and in some cases a DTC would be logged. In the case of BMW in particular, at least three vehicles were down on power and in all cases the fuel pump proved to be at fault.
ANDY’S FINAL THOUGHTS
It was obvious to me that my new customer, like others before her had fallen into the hands of what I describe as ‘Fault Code Jockey’s’. By this I mean that you’ll often read adverts in the local paper saying: “We have the latest in diagnostic equipment that can pin-point any fault”, however If that was the case I would be a millionaire by now!
Every aspect of a fault must be reviewed and tested and such a job can be very challenging. As such, knowledge is not only needed but in a lot of cases it is also gained. Using BMW as an example, a faulty fuel pump can log a DTC of ‘lean fuel mixture’ and ‘Lambda sensor’ but that doesn’t automatically mean you have found the problem and doesn’t even guarantee that there is a base to start with. Therefore it should be remembered that regardless of how committed you may be, there is always room for improvement!