HEVRA’s Pete Melville returns for part two of his hybrid and electric vehicle series. In this month’s article, Pete takes a closer look at the components that make up a hybrid or electric car.
In the last article, we spoke about the reasons for electrification and I provided a brief introduction to the hybrid car. Now, we’re going to look in a little more detail at the components that make up a hybrid or electric car.
Electric motor
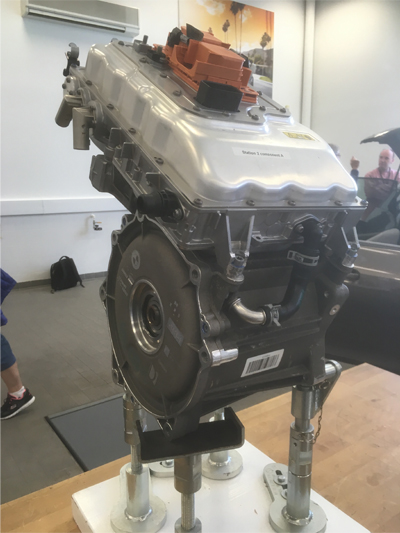
Firstly, we need to have an electric motor in order to drive the wheels in conjunction with the combustion engine. A DC motor such as those used for window regulators and windscreen wipers is not really suitable, as the large current flow across the brushes would result in poor efficiency and reliability. Instead, we use a three-phase AC motor.
There are two parts to the motor – the rotor (which rotates), and the stator (which is stationary). Think of the rotor as the crankshaft and the stator as the engine block if you prefer. The stator is formed of coils of wire, and as we pass current through them, they become electromagnets. By turning on the electromagnets alternately, we create a moving magnetic field. The rotor is magnetic, and therefore follows this magnetic field and creates our turning force. Some rotors have permanent magnets (e.g. Toyota), others have a wound rotor that becomes a magnet when current is induced from the stator (e.g. Tesla), and others have a wound rotor with a separate DC feed to turn it into a magnet (e.g. Renault). In all cases, the principle of the rotor following the rotating magnetic field is similar.
Inverter
So, in order to turn the motor, we need to feed it with alternating current. Our battery of course contains DC (AC cannot be stored), so we need a device in the middle to convert it, and this is the inverter. We’ve already established what causes the motor to turn, but we need some control over it. The motor’s torque is controlled by the current through
the windings, and the motor’s speed is controlled by the speed at which we switch on the windings (think of the latter like the ignition advance). For example, if we’re accelerating down a hill, we can switch the phases very quickly to speed the motor up, but we need little current. If we’re parking a caravan, we’ll need lots of torque but very little speed, so we can put lots of current through the windings, but alternate them relatively slowly. If you’ve seen the numerous videos of Teslas on the drag strip, you’ll have noticed that not only do they beat most things they’re put against, they do so with very little wheelspin. This is thanks to the very accurate speed control of an AC motor.
In order to drive the motor, first we must know its existing position. This is done by a rotor position sensor, or in some cases a resolver. The motor control module then decides which phases to switch on next, and with what current. The power transistors in the inverter then do the actual switching to operate the motor windings. The inverter also provides a path from the windings back to the battery for regenerative braking.
A separate inverter is needed for each AC motor in the vehicle. For example, the Tesla Model X has one in the rear for the rear motor, another in the front for the front motor, and a third in the air conditioning compressor to run its built-in electric motor. The second generation Toyota Prius has just one housing, which contains the inverters for both motors and the A/C compressor.
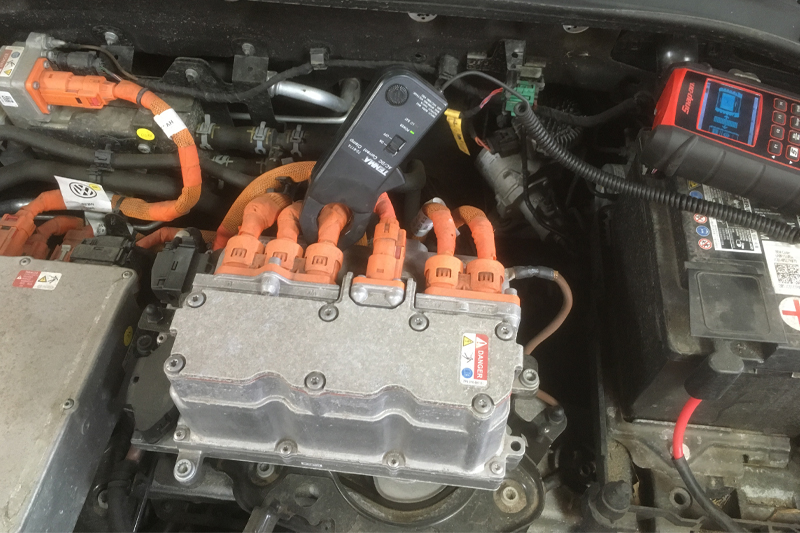
Inverters are almost always liquid cooled. The majority of cars have a completely separate low temperature cooling system so that heat from the engine doesn’t overheat the high voltage components. Others split off part of the cooling system at a certain temperature for the same reason (e.g. Mercedes), while some have innovative ways of using this waste heat to warm the battery (Tesla) or warm the interior (Hyundai). BMW uses the low temperature coolant circuit for cooling the intake air on turbocharged hybrids.
Most hybrid cars use two motors. One is used for starting the engine and spends most of its time as a generator. The other is used for driving the wheels and regenerative braking. Of course there are a variety of different systems used by different makes and models. Most cars package the inverter, motor control module and DC-DC converter into one housing. The DC-DC converter takes the place of an alternator.