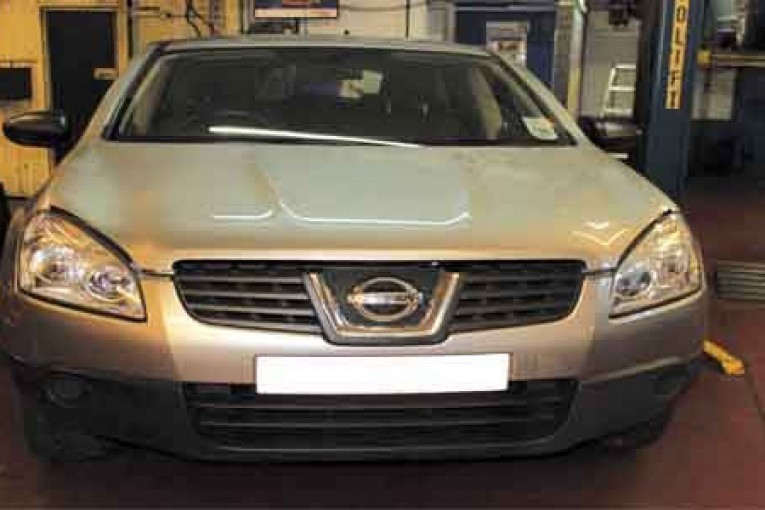
Famously named after a nomadic Turkic tribe in Iran and introduced in 2007, the first generation Nissan Qashqai has made quite an impact during its five-year production span.
Selling more than 130,000 vehicles until it was replaced by the second generation version in 2010, the Nissan has become a common sight in the UK aftermarket which makes it a prime candidate for a ‘clutch clinic’ inclusion.
Removing the clutch
No special tools are required to complete the repair, the only additional tools needed are a transmission jack, an engine support cradle and a long axle stand. A two-post ramp was used in this example and it is recommended that you don’t use a four-post ramp as it may not provide enough clearance. For the sake of safety it’s considered best practice to disconnect the battery earth lead before commencing work. If the vehicle has alloy wheels it may be fitted with anti-theft wheel bolts, so make sure you have the key before you start.
Open the bonnet and unbolt the clamp securing the battery. Undo the battery terminals and lift out the battery. Slide out the plastic battery undertray and release the electrical harnesses (Figs 1 & 2) attached to the battery support housing.
Fig 1
Fig 2
Undo the single bolt (pictured below) securing the airbox and release the clips securing it to the inlet manifold.
Unclip the housing near the grill and lift up the complete air filter housing. Undo the bolts securing the metal part of the battery tray and lift it out. Clamp the flexible part of the slave cylinder pipe to prevent any fluid loss and disconnect it. Unbolt both starter motor bolts and pull the unit back. Unclip the gear linkages by pulling the tab (Fig 4) and squeezing the clips together (Fig 5).
Fig 4
Fig 5
Remove all pipes and harnesses clipped to the gearbox and remove the upper bell housing bolts. Support the engine using the cradle and remove the complete gearbox mounting assembly. Raise the vehicle halfway and remove both front road wheels. Remove both hub nut split-pins and undo the nuts. Undo the bolt securing the lower suspension arm on both sides and release. Release both track rod ends and drain the gearbox oil. Remove the nearside driveshaft and the wheel arch liner (pictured below).
Disconnect the reverse light switch and remove the offside driveshaft by removing the support bracket bolts (pictured below).
Remove the gearbox stabiliser bracket and undo the lower bell housing bolts. Using the gearbox stand, carefully support the gearbox as its separated from the engine and rest it on the subframe under the wheel-arch. There should be enough clearance for the clutch and release bearing to be replaced without having to lower the subframe.
Checking the flywheel
With the clutch removed, check the flywheel for signs of heat stress. Clean the first motion shaft splines and any debris from the bell housing (especially important when a release bearing has failed). Depending on the application, the Concentric Slave Cylinder (CSC) may look a little different to the old version. This is completely normal as the original parts have been updated so don’t worry about fitting it. Selecting the correct CSC in some cases can get a little tricky as there are four different versions of the CSC fitted and they all have different sized connection ports. Don’t be alarmed if the motor factor asks you to measure the old CSC as this may be the only way to indentify the correct unit.
Put a small dab of high melting point grease (not a copper-based product) on the first motion shaft splines and make sure the new driven plate slides freely back and forth. This not only spreads the grease evenly but also makes sure you have the correct kit. Wipe any excess grease off the shaft and driven plate hub. Using a universal alignment tool, and checking the driven plate is the correct way round, (note “Getriebe Seite” is German for “Gearbox Side”) the clutch can be bolted to the flywheel evenly and sequentially.
Before fitting the gearbox make sure the locating dowels are in place and not damaged. Refit any that have become dislodged and refit the gearbox. Make sure the gearbox bell housing bolts are secured before lowering the jack. Refitting is the reverse of the removal.