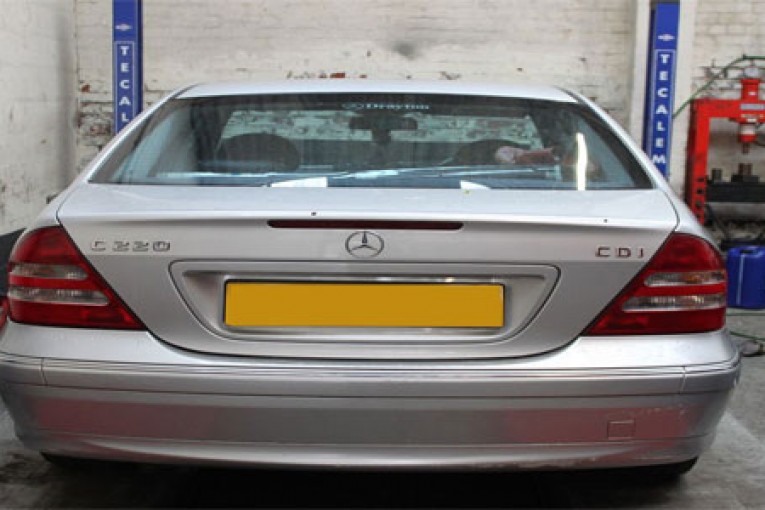
Introduced in 2000, the Mercedes C Class W203 is a proven contender for the competitive executive compact market and has sold over 80,000 vehicles in the UK, making the vehicle a perfect candidate for this clinic.
A clutch replacement on the Mercedes can be a little tricky but with guidance of the LuK ‘Clutch Clinic’, the whole process will become much easier. Nothing out of the ordinary is needed to complete the job, the only special tools required are a transmission jack and a long axle stand. A four-post ramp was used in this example however a two-post ramp may also be suitable.
For safety reasons its considered best practice to disconnect the battery earth lead before commencing work. The vehicle may be fitted with anti-theft wheel bolts, so make sure you have the key before you start.
Raise the vehicle and remove the small rear under-tray and the supporting bracket attached to the chassis. Unbolt and remove the exhaust mounting bracket (Fig 1) and remove the large clip (Fig 2) securing the exhaust assembly to the down pipe.
Fig 1
Fig 2
While supporting the exhaust, remove the supporting rubber mountings near the rear silencer and lower the whole system to the floor. Undo and remove the two central heat shields (pictured below) to provide access to the propshaft.
Undo the centre support bracket for the prop-shaft and remove the clips connecting the gear change mechanism (pictured below) to the bracket.
While supporting the gearbox, undo the large mounting (pictured below) and the large rubber support.
Unclip both the handbrake cable and the selector cable and stow them to one side. Mark the positions of the front and rear propshaft flanges (pictured below) and remove the nut and bolts attaching them.
Unbolt and remove the centre bearing support and carefully lower the prop-shaft assembly to the floor. Release the gearbox change mechanism from above the gearbox, secured by a small clip and a ball joint.
Unplug all the electrical connections from the gearbox and near the bell-housing. Disconnect the slave cylinder connection by releasing the small clip (pictured below) and pulling out the pipe.
Plug the pipe to prevent leakage and undo all of the bell-housing bolts with support before carefully lowering the gearbox to the floor.
With the clutch removed, check the dual mass flywheel (DMF) for signs of heat stress and evidence of grease loss. The DMF should also be tested for ‘freeplay’ and ‘rock’ between the primary and secondary masses (LuK tool number 400 0080 10 is specifically designed for this purpose on all LuK manufactured DMFs). Full instructions and tolerance data for all LuK DMFs are contained on a CD which comes with this special tool.
Splines maintenance
Clean the first motion shaft splines and any debris from the bell housing (especially important when a release bearing has failed). Remember, if the bearing or sleeve is made of plastic there is no need for lubrication. If both parts are metal, a high melting point grease should be used and not copper-based products.
Put a small dab of grease on the first motion shaft splines and make sure the new driven plate slides freely back and forth. This not only spreads the grease evenly but also makes sure you have the correct kit. Wipe any excess grease off the shaft and driven plate hub. Using a universal alignment tool and checking the driven plate is the correct way round (note “Getriebe Seite” is German for “Gearbox Side”) the clutch can be bolted to the flywheel evenly and sequentially.
Before fitting the gearbox make sure the locating dowels are in place and not damaged. Refit any that have become dislodged and refit the gearbox. Make sure the gearbox bell housing bolts are secured before lowering the jack. Refitting is the reverse of the removal.