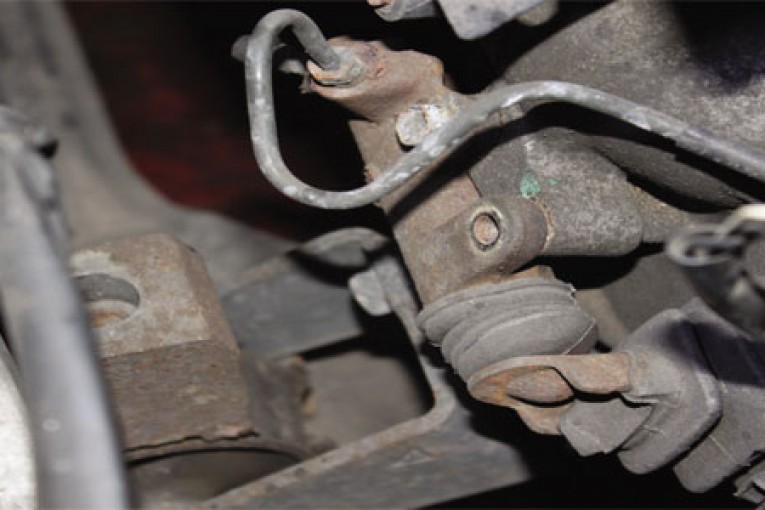
The Toyota Corolla was first launched in 1966 and has undergone several design alterations over its 11 generations. In July 2013, it reached a milestone by selling 40 million vehicles worldwide, so it will no doubt have made its presence felt in workshops throughout the UK.
This helpful guide should, therefore, prove handy for any garage looking to undertake a clutch repair. The clutch replacement is pretty straightforward, with no special tools required for the repair. A two-post ramp, two transmission jacks and an engine support beam were used for this repair.
It is important to note first that if the vehicle has alloy wheels fitted then you need to ensure that the locking wheel nut tool is available to remove them before starting the job.
Lift out the battery
Remove the engine top cover and then disconnect the battery terminals and stow. Undo the battery support clamp and lift out the battery. Remove the plastic battery support seat. Disconnect the Mass Air Flow (MAF) sensor switch from the air filter box and stow. Remove the air filter and housing compartment, which is secured in place with three bolts.
Unclip the wiring harness – connected to the gearbox by three clips – and undo the bolt for the earth cable bracket before stowing safely. Undo and release the two bolts holding the Clutch Slave Cylinder (CSC) to the gearbox (Fig 1) and undo the bolt that secures the hydraulic pipe on the top of the gearbox (Fig 2).
Fig 1
Fig 2
Stow towards the rear of the engine compartment. Remove the three accessible bell housing bolts at the top and disconnect the reverse light switch from the gearbox and stow. Remove the one accessible starter motor bolt. Support the engine by using the engine support beam. Undo the four bolts holding in place the top gearbox mount and undo the three bolts holding in place the gearbox support, before removing (Fig 3).
Fig 3
Raise the vehicle and remove both front wheels. Drain the gearbox oil. Undo and release the three securing nuts for the lower suspension arm links on both sides and detach the joints. Remove the splash guard and bottom section of the wheel arch liner from the nearside. Undo the driveshaft nuts and remove the drive shafts completely.
Remove the bottom front gearbox mount bolt (Fig 4) and the rear gearbox mount bolt (Fig 5).
Fig 4
Fig 5
The cross member will need to be removed; this is secured in place by six bolts – two bolts are at the front and four are at the rear (Fig 6).
Fig 6
When removing this, take extra care as it could drop suddenly. Remove the two gearbox brackets to allow some extra clearance for the gearbox removal. Undo the remaining starter motor bolts and remove.
Free the cables
Detach the gear linkage cables from the link arms held in by two clips. The clip for the first cable is on the top and the clip for the second cable is to the side (Fig 7).
Fig 7
The cables are then held in place within the bracket by two retaining plates. These were a little tricky to remove but, with a little perseverance, they eventually come loose. Once the cables are free, stow to the side securely. Remove the remaining bell housing bolts and carefully lower the gearbox to the floor.
Remove the worn clutch cover and clutch plate. With the clutch removed, check the flywheel for signs of heat stress such as hair line fractures or cracks. Clean the first motion shaft splines and any debris from the bell housing, which is especially important when a release bearing has failed.
Put a small dab of high melting point grease – not a copper-based product – on the first motion shaft splines, and make sure the new driven plate slides freely back and forth. This not only spreads the grease evenly, but also makes sure you have the correct kit.
Wipe any excess grease off the shaft and driven plate hub. Using a universal alignment tool, and checking the driven plate is the correct way round (note: “Getriebe Seite” is German for “Gearbox Side”) the clutch can be bolted to the flywheel evenly and sequentially.
Before fitting the gearbox, make sure the locating dowels are in place and not damaged. Refit any that have become dislodged and refit the gearbox. Make sure the gearbox bell housing bolts are secured before lowering the jack. Refitting is the reverse of the removal.