Back by popular demand, Scantec Automotive’s Ross Kemp explains why fitting poor quality, cheap parts can lead to some diagnostic head scratching, as well as being a false economy.
As diagnostic specialists, we at Scantec often wonder why customers pay for our professional services and advice, and then don’t follow it. I would like to share a classic example with you in this article. The vehicle in question was a very low mileage Ford Focus, brought to us from another workshop. The initial complaint reported to us was that of an intermittent engine MIL warning and two fault codes relating to both post catalyst oxygen sensor heater circuits. The customer had duly replaced both sensors and was still experiencing the same faults.
An initial global scan did in fact confirm that we had two faults stored in the PCM – P0136 and P0156. Interestingly, although these faults related to both post catalyst oxygen sensors, they did not and do not relate to the heater circuits in any way – they in fact relate to a ‘no change in signal issue’.
Monitoring of all four sensors very quickly confirmed that both post CAT sensors continued to switch in time with the pre-CAT sensors, even after an extended road test, confirming to us that the catalyst itself had failed, with no gas conversion taking place. Quite clearly, replacement was required. At this point, we sent the vehicle back to the customer garage for them to source and fit a replacement.
Several months later, we received a call from the workshop, and they stated that they had replaced the CAT, but shortly afterwards the engine started to display misfire type symptoms and drivability issues. The workshop requested we book it in for some testing.
On arrival, the engine was, without doubt, struggling. It displayed a very uneven idle with the engine rocking about in its bay. However, the following morning when we set about testing, we noted with interest that the engine started and ran perfectly, with only one fault code logged in the PCM: ‘P0300 Random Cylinder Misfire’. Despite this, after a few minutes of running, the engine reverted to type and was back rocking away as per when it arrived.
Initial testing (including ignition and injector signal analysis) confirmed that no single cylinder was misfiring – in fact, it seemed to suggest that all cylinders were suffering from combustion anomalies. Mechanical, fuelling or ignition was our initial thought process here, but as the engine ran so well from cold, and since ignition testing showed no issues, we decided to initially concentrate on fuelling, as it seemed the most logical.
As you can see in Fig 1, we established that, interestingly, cylinders 1 and 4 quite clearly had a much longer on time – in fact nearly double that of cylinder 2 and 3. But why?
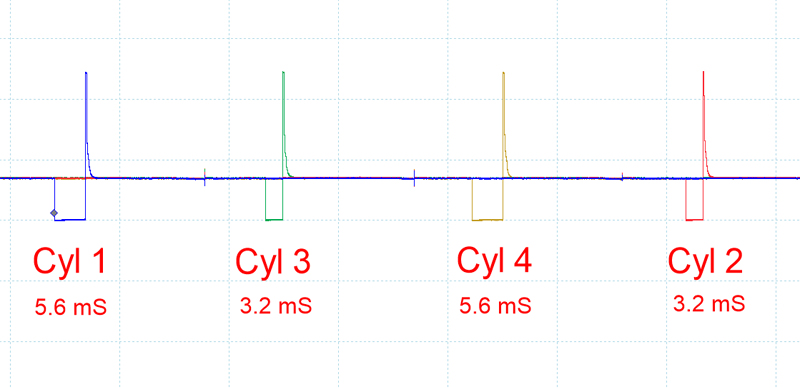
A little product knowledge is required here. This vehicle utilises a 1.6L Zetec-S PFi VCT engine, running the Siemens Sim29 engine management system, which runs four O2 sensors – two before the CAT and two after. Therefore, the Siemens system (when running in closed loop) runs two banks with regards to fuelling. Cylinders 1 and 4 are bank 1, and cylinders 2 and 3 are bank 2.
So, going back to our injector/fuelling issue, we can see that bank 1 is running nearly double the on time when compared to bank 2, so our thoughts return to the mix of genuine and non-genuine O2 sensors and their recent removal and refitting. Initial monitoring of all four O2 sensors confirms that they are all indicating a rich mixture (void of oxygen) with little activity taking place.
Forcing the system into an open loop strategy (by disconnecting the two pre-CAT O2 sensors) confirmed that the engine ran smoothly. However, bank 1 was still running much longer on times, clearly showing some learnt adaptations were taking place. We dealt with this by resetting fuel adaptations, but with the O2 sensors reconnected, the system would soon revert to type.
At this point, we really wanted to confirm basic injector operation to confirm no leaking, or over or under fuelling. When diagnostic testing, we aim as much as is practically possible to not disturb the system we are testing, in fear of changing the fault in some way. We also don’t want to remove the injector unless we must.
So, at this stage we ran some quick fuel injector delivery testing (see Fig 2) by means of monitoring static fuel pressure and externally activating all four injectors one at a time for a fixed period of time, while monitoring the fuel pressure drop. The theory was that, if the same fuel pressure is applied to each injector at the start of the test and each injector is activated for exactly the same time, the resulting end pressure should be the same, unless there are delivery differences between the injectors.
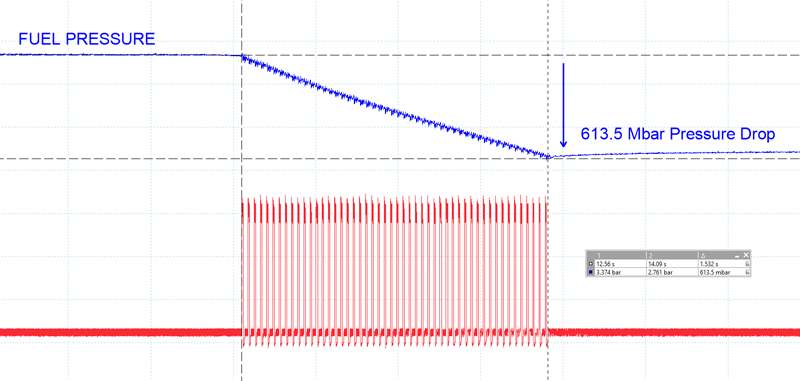
Our testing proved that not only were none of the injectors leaking, but they all displayed the same delivery rate, with a smooth uniform pressure drop. Therefore, we had to have some form of PCM calculation error or the PCM was receiving some incorrect information from the pre-CAT O2 sensors to make it believe additional fuel was required on bank 1.
To confirm correct PCM operation, we used an O2 sensor simulator while monitoring data diagnostically, to confirm that not only were the O2 sensors connected the right way around (important when you have four O2 sensor plugs in close proximity), but more importantly, that the PCM responded correctly by adjusting both banks’ fuelling as expected.
So, we stepped back slightly at this stage to establish what we know so far: all four O2 sensors are operating correctly, PCM is correctly interpreting those four O2 sensor signals, all four injectors are balanced and operating as expected, and the engine runs perfectly when in open loop – hence why, on initial cold start up, we noted no running issues.
Going back to basics, we had to consider that this issue only started after the CAT was replaced. We decided to have a look at this new CAT, and something was definitely not right. We noted that the exhaust pipes on cylinders 1 and 2 appeared to feed into one side of the CAT, and those on cylinders 3 and 4 into the other.
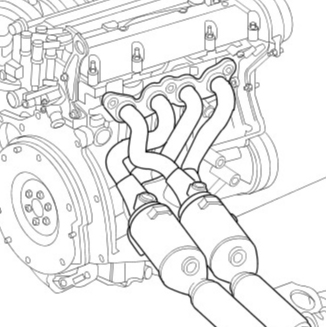
Yet, we knew from system knowledge and the above testing results that cylinders 1 and 4 were one bank, and 2 and 3 were the other, so this (not so well-built) aftermarket CAT that was fitted had the wrong exhaust pipe layout. Therefore, the O2 sensor locations were completely wrong.
When you consider the fact that the bank 1 O2 sensor is commanding fuelling adjustments via cylinders 1 and 4 injectors (as designed) but is in fact receiving exhaust gas data from cylinders 1 and 2 instead, it all became a little clearer as to what was going on. The PCM is never going to be able to adjust or correct the fundamental issue of the exhaust pipes being the wrong way around.
We also noted during testing that both the pre-CAT O2 sensors had damaged tips. We discovered that this was caused by poor quality welding of the O2 sensor mounting nuts, causing tips to be damaged on installation.
An interesting job, all in all! We were a little amused, however, when reviewing the job (and the original report condemning the original CAT) that we advised the fitting of a genuine unit. We have long advocated the use of genuine parts and the above is, in our opinion, a classic example of why.