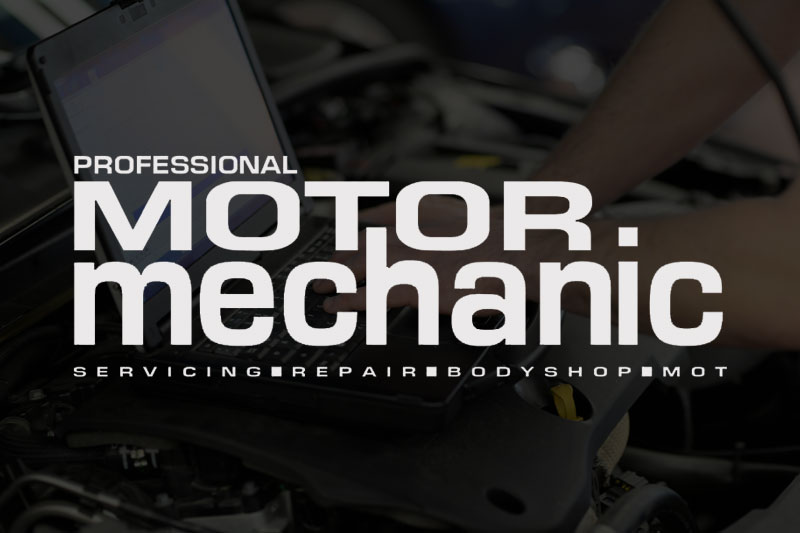
Glow plug technology can be divided into two major categories – metal sheathed types and ceramic types. Ceramic glow plugs utilise a heating element which is encased in a special type of ceramic – Silicon Nitride. Ceramic glow plugs have the ability to heat up more quickly than metal types and in addition can gain higher operating temperatures for an extended period of time. They are also more compact making these features especially advantageous in modern engines.
THE MAKE-UP OF A CERAMIC GLOW PLUG
Insulator – The insulator separates the electrically positive (Connection terminal) from the electrically negative part (Metal shell) of the glow plug.
Thread – The thread of a high-quality glow plug is always rolled and never cut. By this production method fast, accurate threads are formed, eliminating the possibility of damage to the glow plug bore in the cylinder head.
Centre electrode – The supply voltage is applied to the coils via the solid centre electrode.
Heating coil – Contrary to a metal glow plug, a ceramic glow plug uses a ceramic heating element.
Ceramic casing – The heating coil or heating element of a ceramic glow plug is encased in a high performance ceramic material: silicon nitride. It protects the coil from the high temperatures and vibrations created by the combustion process. It is also an excellent heat conductor, allowing the heat energy of the coil to be rapidly released into the combustion chamber.
Connection terminal – The supply voltage is applied at the connection terminal. This may be a threaded post to suit a connector which is secured by a nut or an unthreaded post to suit a push-on connector.
Metal shell – The metal shell of a glow plug usually provides the electrically negative pole (ground connection).
Taper seat – The taper seat provides simple but effective gas-tight sealing of the combustion chamber without the need for sealing gaskets, etc. Its compact form also allows bore sizes to be kept to a minimum. The taper faces also provide an excellent electrical ground (earth).
Contacting ring – The contacting ring provides the electrical connection at the junction of the centre electrode and the heating element.
INSTALLATION ADVICE
Particular care must be exercised when installing ceramic glow plugs. When fitted, the ceramic is designed to withstand the arduous events that occur within in the combustion chamber, however they are more susceptible than metal types to damage caused by unsupported side loads or impact. Improper installation can make it unusable or even lead to damage to the engine.
1. Where possible the removal of a glow plug should take place with the engine at operating temperature to assist in releasing the plug.
2. Carefully loosen the glow plug.
3. Remove any loose debris around the glow plug with compressed air.
4. Unscrew the old glow plug.
5. Remove any carbon deposits from the glow plug bore – with a reamer if necessary – then clean and inspect the thread in the cylinder head.
6. Screw the glow plug in by hand until it seats in the cylinder head.
7. Set the torque wrench to the correct tightening torque.
8. Ensure that the socket of the torque wrench is correctly in line with the tightening nut of the glow plug and secure it.
9. Refit the electrical supply connection.