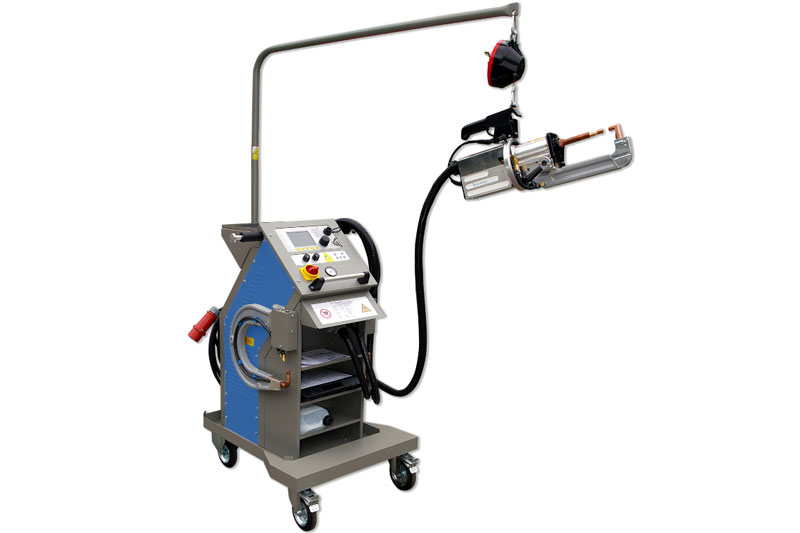
Automotive welding jobs have just become easier task for professional bodyshops, thanks to the arrival of the Elma-Tech MIDI-spot-VISION, supplied by Stafford-based bodyshop equipment specialist, Tri-Sphere.
Automatic detection of normal or high strength material type, automatic detection of total sheet thickness are two major advantages delivered by the new Elma-Tech welding system, which has aluminium welding capabilities.
Manufactured in Germany by Elma-Tech, the MIDI-spot-VISION is a medium frequency inverter, designed for use on bodywork built from high or maximum strength steels and alloys.
Tri-Sphere says the water-cooled MIDI-spot-VISION system delivers an output of up to 13,000 kVA, from a 32A supply. In addition, it delivers 500 decanewtons of weld pressure and complies with all UK legislative requirements, including EU Directive 2004/40EG.
Safety is a major concern for any welding system operator and the Elma-Tech delivers there, too. As the transformer is housed in the gun rather than the machine, a significant health and safety concern has been removed. Meanwhile, the MIDI-spot-VISION welding system provides all the welding capabilities that bodyshops need – from a single machine.
The system features built-in energy controls as well as parallel resistance detection. The fully automatic welding process checks the status of each weld every 50 microseconds. Welding parameters for each job are recorded and can be assigned to a specific vehicle and downloaded or updated via a USB.
In use, the Elma-Tech MIDI-spot-VISION welding system is extremely versatile, accommodating galvanised coated panels, or panels with traces of E coat paint/adhesive, with ease.
The lightweight gun makes dent repairs, steel plate pulls or pin and T-pin welds, very straightforward indeed.