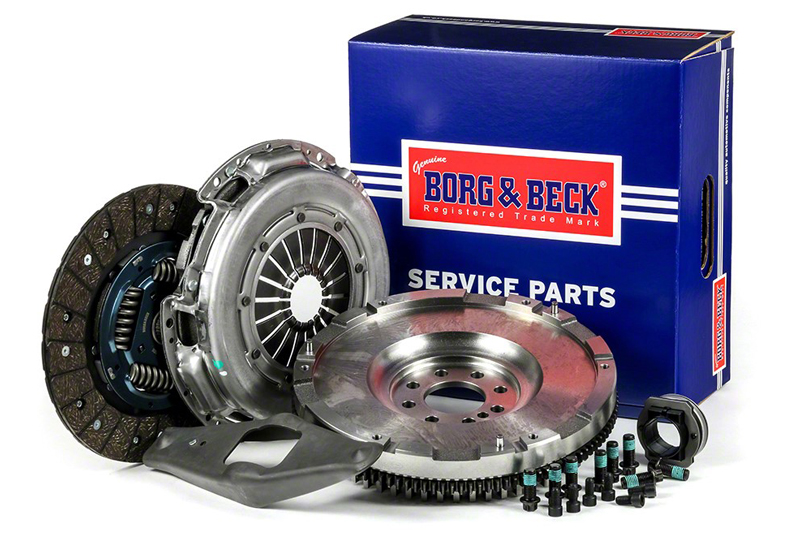
First Line has shared the most common installation errors it has come across for the automotive clutch system, in a bid to prevent technicians from making the same mistakes.
How to check if a clutch is faulty
There are many factors that can contribute and cause a clutch to fail. One of these examples is driving style: does the driver ride the clutch and unknowingly burn through it; has the vehicle been used to tow; is it regularly parked on a steep hill; or has it recently had a clutch fitted, which unfortunately could have been misaligned or over greased during installation and has therefore failed prematurely? All of these questions are ones that technicians should be asking the driver, as this may help lead them to a correct diagnosis. In addition, one of the most important areas to check is the release mechanism, because, irrespective of whether it is hydraulic or cable driven, if something has seized or worn, this could certainly cause the clutch to fail.
Common installation errors
Clutch Judder
Judder can result from over-greasing the splined input shaft. In fact, it only requires a small amount of grease to operate correctly and if too much is applied, then this can splatter onto the plate, contaminating the surface and causing the problem.
A similar effect can also occur if the cover is not bolted down evenly or seated on the dowels. If it is not correctly aligned and bolted down, the clutch plate will not clamp evenly during clutch engagement, leading to judder.
Clutch Slip
Slip can be caused by contamination such as an engine to gearbox oil leak or if the clutch cable is adjusted too tightly. It can also be triggered if there are seizing components within the hydraulic system.
Clutch Drag
Drag can be generated if the hydraulic system hasn’t been bled properly, which will result in the release mechanism not achieving the right travel to totally disengage the clutch. Cable driven vehicles can suffer a similar effect if the adjustment is incorrect.
Another common cause of premature failure is due to a ‘hung’ gearbox. It’s, therefore, vital for technicians to use the correct equipment to support it and lift it into place, as the slightest distortion created from it hanging on the engine during installation, will result in damage.
First Line’s Borg & Beck range consists of more than 800 references and includes 2 in 1 clutch kits, 3 in 1 clutch kits, 3 in 1 concentric slave cylinder clutch kits and solid flywheel kits, all of which are of original equipment (OE) quality with two year/unlimited mileage warranty against manufacturing defects for total peace of mind.