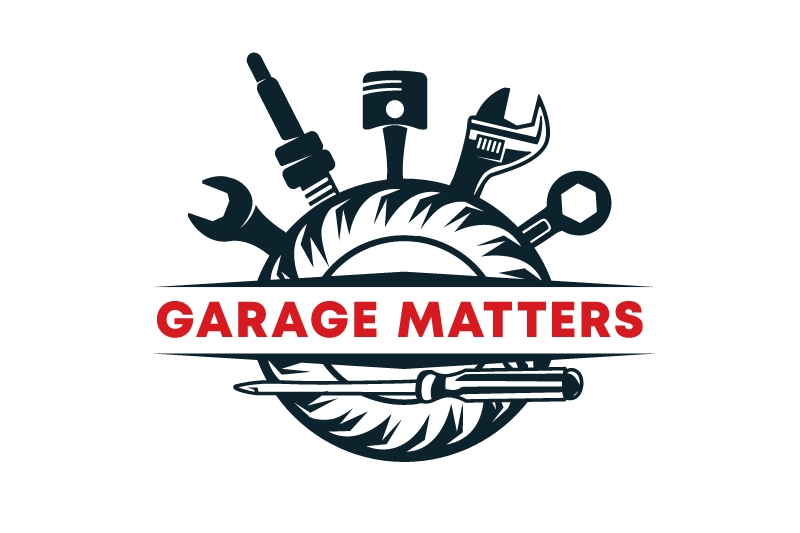
In this instalment of Garage Matters, PMM explores the rise of remanufacturing and asks why some garages in the UK remain reluctant.
I am sitting down to write this in the aftermath of Europe’s premier aftermarket trade show, Automechanika Frankfurt. An absolutely mammoth event, the biannual show might not be that familiar to readers of PMM. Unlike its UK counterpart, the German flagship is a very suit-heavy affair and, after all, why would you travel to a trade show in Germany when we have perfectly wonderful regionalised trade shows here in the UK (ahem, Mechanex). I bring it up because as I racked up the mileage walking from one meeting to another, which I’d poorly arranged back-to-back despite being miles (literally) apart, I happened to pass the APRA, or the Automotive Parts Remanufacturer’s Association, stand, on which they were giving a talk to a packed out audience. I couldn’t believe it – was this the same APRA that I stopped to chat with (and rest my feet) at a pop-up stand in the Automechanika foyer two years ago? Well, maybe that’s an indication of how much remanufacturing has taken off in recent years – indeed, we now include a regular feature on remanufacturing.
APRA themselves have set a useful definition for what constitutes a remanufactured part: it must fulfil a function at least equivalent to the original part; it must be restored from an existing part (the core), using a standardised industrial process; it must come with the same warranty as a new part; and, lastly, it isn’t a reused, repaired, rebuilt, refurbished, reworked or reconditioned part…
I have seen firsthand the remanufacturing process at Shaftec’s plant where they remanufacture steering racks, driveshafts, brake callipers and other hardwearing parts. The process of assessment, deep cleaning, stripping and reassembly with any failed components replaced with new ones results in a batch of products which are identical to brand new parts. Each part undergoes quality control before being shipped out. This, as I understand, is a fairly typical remanufacturing process.
We highlighted in last month’s issue the new slogan from Carwood to describe its remanufacturing ethos – “quality parts that don’t cost the earth”. We were quite taken with it in PMM HQ and it is an important reminder – reman parts are cheaper than new OE-quality parts, as much as 25 per cent cheaper, in fact. The reason for the saving often comes down to the fact that you get money back if you send in the part you’ve removed from your customer’s vehicle, i.e. the core. Sending that back is a necessary step in the whole remanufacturing process and indeed is the thing remanufacturers claim is the biggest stumbling block.
Many remanufacturers are able to offer options for historic vehicles that ordinary parts suppliers struggle to because they obtain their stock from the vehicles that are already on the road. But all of this requires workshops to be proactive in their part replacement routine. The better you look after, and the sooner you send back, the removed part, the more likely you are to receive your surcharge back.
For various reasons, remanufacturing has not been predicted to grow hugely by 2030, in contrast to the rest of the aftermarket. It’s not hard to imagine that as business grows in quantity, rather than quality – i.e. more cars need to be fixed, but those cars are getting older and cheaper – and staff shortages continue to dog workshops, the last thing workshop owners want to have to think about is sending back parts. Better, surely, to charge full price to the customer and get the job done and dusted?
Whilst, along with Germany, the UK is apparently one of the top users of reman products in Europe, the practice still suffers from a perception of being “used” or “second hand” parts. With all the will in the world, drivers rarely think “green” when offered the choice between two parts (and with an average of 80 per cent retained parts, reman parts are certainly the green option), they think about price and, if you’re lucky, safety.
France, the Netherlands and the Scandinavian countries have, like certain US states, laws that promote remanufacturing and this includes an obligation to offer customers a remanufactured option where available.
I was kindly taken out to Krakow in Poland, earlier this year, by Valeo. After a tour of the old town on day one (including the dragon’s bones displayed outside the main cathedral, which killjoy scientists say are whale bones….), we visited the Valeo plant in Czechowice on day two and were treated to a rather informative talk on remanufacturing. The company’s director of circular economy Mino Yamamoto told the assembled journalists that the “circular economy starts at the design phase”.
This is something that passenger vehicle manufacturers would do well to take on wholesale, as is common in the CV sector, where remanufacturing is taken into account from the start. One of the issues remanufacturers face is being presented with substandard cores from workshops. Often, cores are damaged as they are removed from the vehicle and that usually comes down to a design issue.
Valeo is determined to buck the trend and has vowed to double its reman offering from one to two million units by 2030 and this will include EV and high voltage parts. With, according to Yamamoto, only 20 per cent of workshops offering reman parts and only 13 per cent of customers accepting them, one might wonder why companies bother at all. The disheartening statistics don’t end there. According to the circular economy expert, two-thirds of workshops say the “reverse logistics” of sending back core is too complex; one third view reman as lower quality than new; one third, possibly the same third, aren’t convinced by the lower price; one third, again, aren’t convinced by the green credentials of remanufacturing; and so on and so forth… In short, sceptical garage owners are not convinced.
But manufacturers and independent remanufacturers clearly are convinced. For them, it removes raw materials from the equation. I put this to the Valeo team in Poland, who conceded it helped, but wasn’t a key driver behind the focus. Whatever it is, hopefully the good old spirit of “waste not, want not” will kick in in the near future, not just in the automotive industry but in all walks of life. It’s a crying shame to produce goods simply to see them languish on shelves and eventually end up in landfill, so why not consider remanufactured parts instead?
For more from this series, click here.