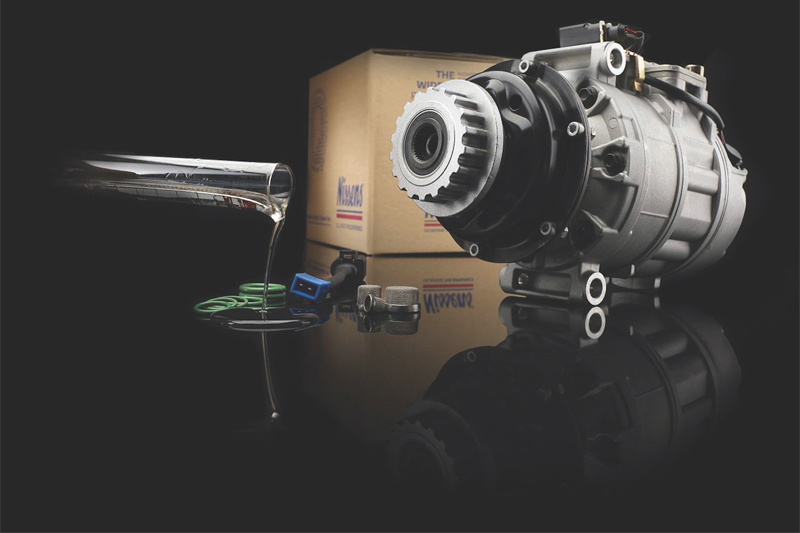
Nissens, the automotive thermal systems expert, explains why technicians should avoid mixing PAG with universal oils at all costs.
Polyalkylene glycol (PAG) oil is the most common lubricant used in modern automotive air conditioning (A/C) systems running on R134a and R1234yf refrigerants. It is a fully synthetic oil that provides efficient and universal lubricating capacity, is conductive, highly hygroscopic (absorbs moisture from the air), and is available in several viscosities (46/100/150).
Due to their advanced mechanical construction and moving components, as well as the fact that they operate at high temperature and pressure, A/C compressor manufacturers specify the precise type and quantity of lubricant that is required for the correct operation, functionality and long service life of their components.
It will come as little surprise therefore that a common reason for A/C compressor failure is the use of oil of a different specification to that stipulated by the compressor manufacturer. If the system is topped-up or filled with a universal Polyaphaolefins (PAO) oil with a viscosity of 68, where the original was PAG oil, for instance, despite the fact that in general the characteristics of PAO and PAG oil seem be similar, their viscosity is different. This can lead to serious problems and ultimately compressor failure, which, in most cases, will lead to the rejection of any subsequent warranty claim.
As good practice, the oil within the A/C system should be topped-up at the scheduled service interval and replaced entirely when the compressor is changed. To avoid the use of the wrong specification oil, manufacturers generally pre-fill their compressors, which also stops dirt, debris and moisture from entering the system. Technicians should therefore check the oil specification dictated by the vehicle manufacturer in order not to mix incompatible formulations.
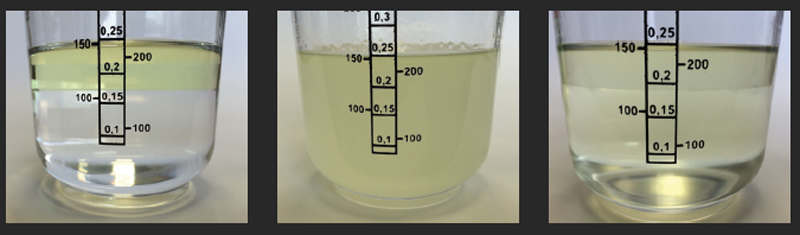
What’s the problem?
The two oils do not mix completely and cannot create a long-lasting homogenous mixture, which is needed to ensure the correct lubrication of the mechanical parts within the compressor. Although initially the oils may visually seem well-mixed, after a short period of time, when the compressor is not running, the two oils will separate (as indicated in Fig 1). When the compressor then starts from cold, separated oil of a higher density and viscosity will lead to less effective lubrication of the precisely engineered internal components, such as between the piston and cylinder, so increasing friction and causing the compressor to overheat and potentially seize.
In addition, universal oils do not mix the same way with the refrigerant as PAG oil does, thus the lubricant’s circulation in the system may be restricted, so as well as exposing the compressor components to potential damage, the system’s other components, such as the expansion valve or seals, could also be at risk.
Recommended solution
Always follow the compressor or VMs guidelines for the right specification of lubricant, but helpfully, Nissens compressors are always pre-filled with the right quantity and viscosity PAG oil and double endcapped, so there is no need to add any extra oil to the compressor.
Double end-capped PAG oil is chemically inactive and stable, offering exceptionally good lubrication characteristics, high moisture tolerance at high temperatures, and does not react chemically to form harmful acids/compounds. To further assist workshops, Nissens compressors are always delivered with an installation guidebook describing the correct installation procedure and are covered by a comprehensive warranty.