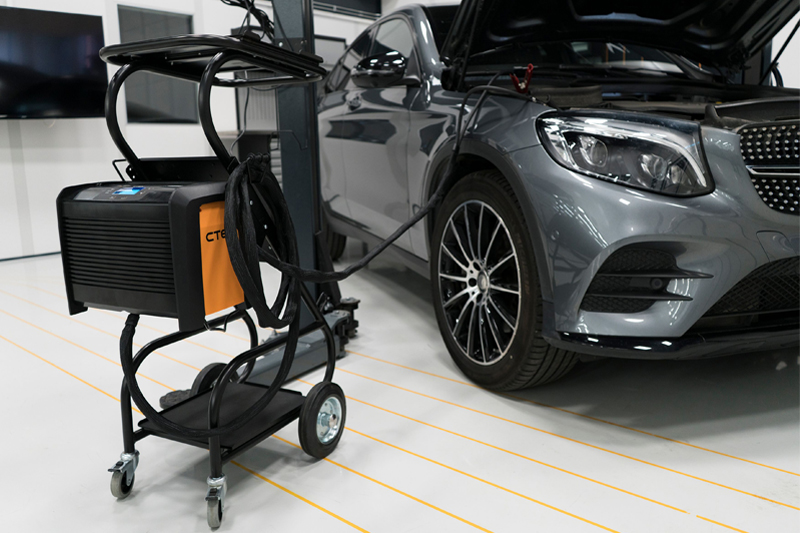
You knew that the battery needed to be supported during diagnostic work, but according to CTEK you should also be hooking up the support unit during service and repair too. Here, we look at why battery support is vital and how the demands on the battery keep growing.
Vehicles today have essentially become very expensive computers on wheels. When a vehicle enters a workshop for service or repair, the diagnostic processes being undertaken as part of these procedures are placing the battery under greater strain than ever before, risking battery failure.
Battery support is therefore an essential part of all workshop practices. Using battery support in conjunction with any routine service, fault finding or repair, should be carried out not only from a technical safety point of view, but also to maximise workshop efficiency and provide a complementary added value service to the customer.
When you open a car door you trigger the interior and exterior lights which can deplete the battery. Using the heating system or electric windows, using the vehicle audio system, charging a phone or other devices from the car and the keyless entry system all use energy which comes directly from the battery. A modern vehicle has more than 200 electronic control units, they are controlling many of the vehicle’s functions and a lot of them are turned on as soon as you unlock your vehicle.
A recent survey undertaken by CTEK in partnership with PMM identified that as many as 80 per cent of vehicles entering the workshop have a battery that needs attention. These batteries either need recharging, reconditioning, or replacing. The survey also found that only 45 per cent of workshops offer battery charging as part of regular maintenance.
While the knowledge about battery support is increasing, many workshops are still not maximising the opportunity. If the battery isn’t in a great state when it enters the workshop, any drains or strains during the diagnostic process could result in battery failure, disrupting the diagnostic procedure. Battery support is a vital activity often not fully appreciated for its importance in saving a technician’s time, insuring against costly diagnostic failures and preventing possible costly damage to the ECU.
The function of the battery support is to give as high current as needed at a preferable voltage and it is recommended to have the battery support plugged in during the whole service session.
Cranking up the amps
A lot of manufacturers have a demand for at least 120 Ampere when a vehicle is undergoing service, and a lot of the new models have a demand for at least 100 Ampere. As a result, CTEK is seeing a big demand for the PRO120 product – a fully automatic 120A battery support unit, with incremental 13 voltage power supply, for precise control over the most demanding fault finding, service and repair procedures.
PRO120 aims to give professional workshops control during all types of diagnostics, updating and repair work. In power supply mode, PRO120 delivers selectable output voltages in 0.1V increments from 12.6V to 14.8V to match manufacturers’ minimum service specifications. It claims to react quickly to sudden power spikes and has extremely low ripple with no flutter to prevent damage to the vehicle’s sensitive electronics. PRO120’s fanless cooling system has no moving parts and keeps the ambient operating temperature constant in hot and cold conditions as low as -20˚C (- 4°F). This prevents ‘derating’, where the heat generated during use causes the output voltage to drop and the diagnostic process to fail.
In conclusion, BSUs play a pivotal role in ensuring the success of software updates and ECU reprogramming processes. With their ability to stabilise voltage levels, adapt to load changes, and optimise output capacity, BSUs like the PRO range from CTEK are assets in modern automotive workshops, where precision and reliability are nonnegotiable.