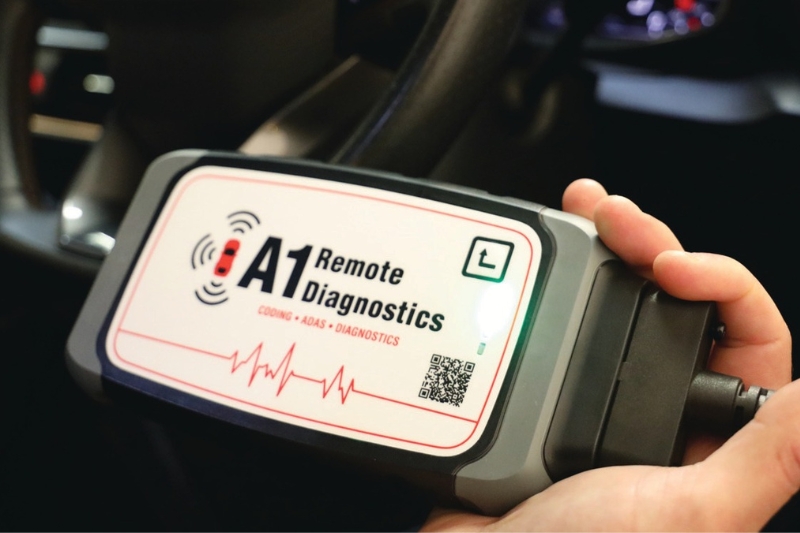
Are secure gateways giving you headaches? You’re most definitely not alone. A1 Remote Diagnostics’ operations director Adam Molloy says secure gateways were the hot topic of conversation at the Mechanex-PMM Live Sandown show last November.
We talked to hundreds of technicians over the two-day event. Of those, 70 per cent reported problems accessing secure gateways. It’s a huge source of frustration for workshops. It’s understandable. What were once straightforward tasks for technicians, have become complex and time-consuming jobs.
The most common problem we heard was resetting service lights. As a garage owner, servicing work is one of the most lucrative. Ideally, you want a good turnover of servicing work on the ramps each day. However, once the service is complete, if you can’t turn off the service light, the reality is that it’s far from complete. That vehicle is now taking up valuable ramp time or causing congestion in the workshop space.
Over the last six months we’ve seen a rise in certain models becoming more problematic. The Volkswagen Audi Group’s SFD and the SFD2’s locks are becoming the most common culprits. But the problem is far from limited to specific models and service light issues. Technicians are also reporting that winding back brake calipers is becoming a big issue, as are other bi-directional controls, component testing, and ADAS calibrations. Unfortunately, secure gateway headaches aren’t always something a busy garage foresees.
A typical scenario is when a vehicle is booked in for rear brake pad replacement. The parts are ordered and it’s only once the vehicle is on the ramp that the technician discovers it has an electric handbrake. As this involves setting the caliper into service mode and winding the caliper back, the diagnostic and coding element will most certainly mean accessing the secure gateway. Suddenly the job is a lot more complicated and time-consuming.
The good news is that help is at hand in the form of independent remote diagnostic interfaces which enable workshops to dial in to fast-responding dealer-trained techs from anywhere in the UK. The interfaces are easily accessible, relatively inexpensive, save a huge amount of time, and protect profit margins. With our A1 Remote Diagnostic interface, we’re seeing workshops turn around jobs in 15 minutes instead of 15 days. Previously, the only option was to take the vehicle to a main dealer to code and finish the job. Now, there’s no need to involve a main dealer at all.
The A1 Remote system covers every mainstream OEM make and model fitted with a secure gateway, making it an invaluable addition to a workshop’s existing diagnostic equipment; none of which have 100 per cent OEM access. The workshop buys the interface, plugs it in to the vehicle and dials in A1 Remote Diagnostics whenever needed. A1’s dealer-trained techs answer within just two minutes, remotely access the vehicle, enter the secure gateway, and complete the job at hand.
For example, if it’s a brake caliper job, the whole thing can be done ‘alongside’ the workshop technician in as little as 20 minutes – including changing the actual pads.
As vehicles become more complex, they’ll have even more ECUs, and secure gateways will continue to be a barrier to work for workshops. The simple answer is to invest in a remote interface.