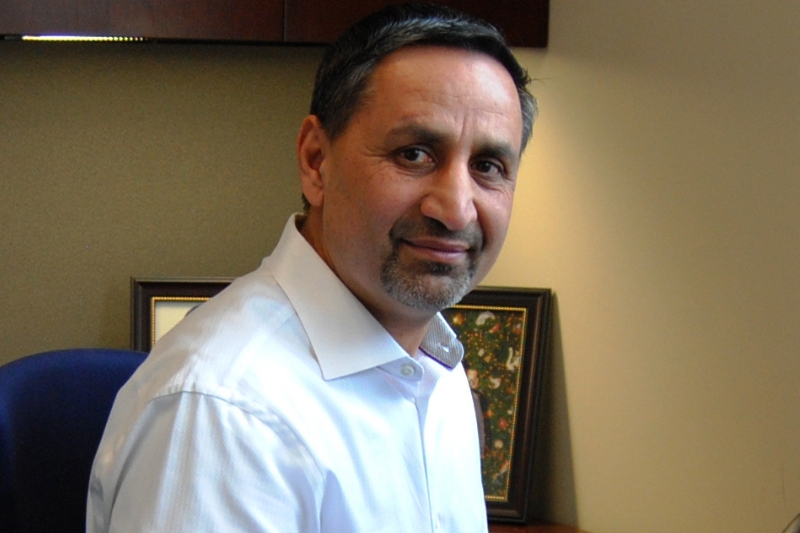
The ALLDATA team kindly came to PMM ’s HQ to discuss the importance of OE data, supporting garages and the future role of AI in car repair.
How can ALLDATA help workshops increase their profits?
Satwinder Mangat, president (SM): If you are fixing the car based on the OEM standard and you’re doing it right first time, then you can fix more cars because you don’t need to try and test and do all the other things and replace a part here and a part there. Once you fix one customer’s car properly, then the referral starts because you fixed it right to the standard.
Now that cars are more complex, is there more need for ALLDATA than before?
SM: Definitely. Complexity is going up, you can’t fix the bumper or change the things that you used to because there are so many ADAS systems, so you need OEM data now for sure. Especially because a lot of these components are safety components, so you need to ensure you are enacting a competent and accurate repair.
What support do you provide to the workshop undertaking these repairs?
SM: So not only are we providing the information and the products, but our customer service offering is also one of the best. If you look into the UK and European markets, we have what we call our Info Centre team. When you are having a hard time finding the information, which is possible anytime because so much is in there, you can call our team and they will provide you that information within a very short period of time. That’s the trust that you can have as a garage that I have the product but if I can’t find the right information then I have somebody sitting on the other side that I can speak to.
And who are those people sitting on the other side?
SM: Some of them are from the technician background, same market background, they understand this space right and that’s how they can find the information. Some of them have worked in the industry for 20 years, so they can help. Not only providing information also, but also sometimes taking them through it. Going the extra mile.
How is the UK market different from North America?
SM: In terms of actually fixing the car it’s the same. However, many of the bodyshops here may not do the work or the mechanical shops may not do the body side. But in the US it’s changing. The mechanical side will now also start doing the body work. They do whatever they can do, maybe not all of it, but they do cross that divide both ways.
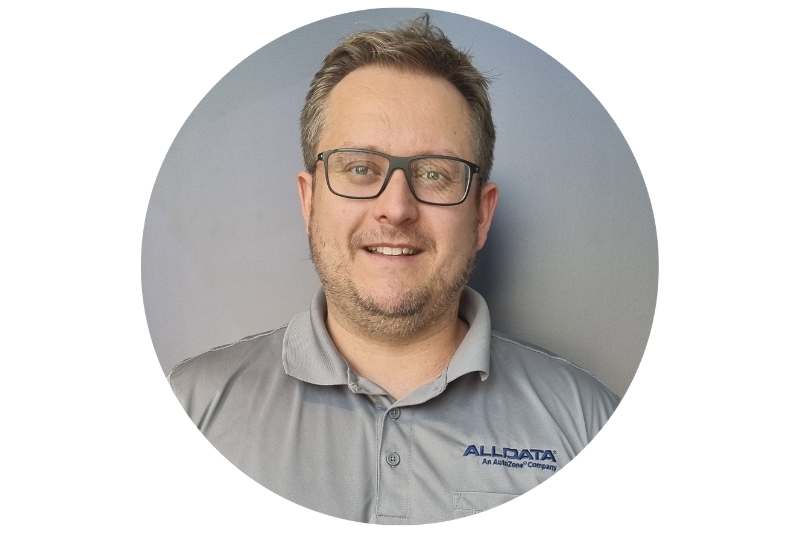
And in the UK you rely on distribution partners to spread the product?
Karol Englert, managing director, Europe (KE): We pride ourselves, and this is not only when it comes to working with partners, but also onboarding our employees, to have a best-in-class onboarding process. It’s really important for us that our resellers understand the product, that they do understand what is the value proposition of our product and that they do understand how can we support and who to approach if they have issues.
Why have you added labour times as an add-on?
KE: Very often jobs are being declined because you just don’t know how long it takes to do it. There is much uncertainty. So, for us it was key to provide labour times to help clarify things for the garage. Frankly speaking, we are discussing this as well within ALLDATA. It’s very difficult to say those are exactly the labour times, right? Because the labour times we provide are the original labour times from the manufacturer. In many cases they fit, but in some real life cases they differ. What we provide is a good estimate and a first idea of how long a certain job will take.
What role, if any, do you think AI will have to play in diagnosing faults in the workshop?
SM: It is providing plenty of opportunities for us, as a company. The first opportunity it presents is simplifying the information search process. Because finding the information is, again, helping our workshops become more effective. So AI can help a lot. We already did a proof of concept last year with one manufacturer and it was much, much better.
The second opportunity AI presents, is once you have the information, how can you simplify it? Right now, if you look into OEM procedures, many of them may be 30 pages long. We know from our technicians, they don’t read 30 pages, it’s too complex. But AI can summarise that information for you as a technician. So for example, these are the six steps that you need to follow. Then you need to go into more detail as you go through. So simplification, creating a layman version of the information is the next step.
The last thing to discuss today, when it comes to AI, is how we can take it to the next step for the workshop. Technicians are surrounded by and generate data everyday. DTCs, trouble codes, make, model, year… we have access to all that raw data which we can harness and analyse to answer “what is the probable cause of that trouble code?” We have millions of records on file, so it will take an AI program to go through all that.
But AI will never write the data sheets itself?
SM: We’re going to still keep the OEM original information right there, available. We will say, here’s the OEM information and here is a simplified version of it. You need to still go deeper into it, for sure. But even the simplified version that we are going to create is going to be from that original 30 page document. We’re not writing anything, just simplifying.