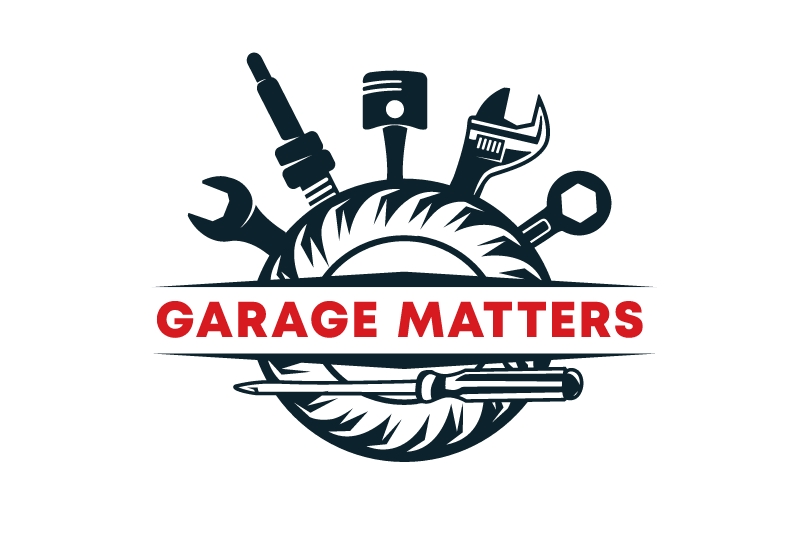
PMM editor Kieran Nee writes about the skills crisis in the automotive aftermarket.
I tagged along on an EV course a few years ago near my hometown, Southend-on-Sea. I arranged the visit for first thing Monday morning so I could go home for the weekend and on a chilly February morning, I and 15 technicians huddled around a sleeping Prius in a huge college sports hall just off the arterial road out of town. In the down time as our assessor prepared our tests (don’t worry, I didn’t take one), we got chatting. First, I spoke to one guy about what he liked and didn’t like about working in a garage, but soon enough most of the group had piled into the conversation, each one adding their own variation on what remained a steady theme: the pay was “pants” (a rather polite bunch, us Saffenders). One guy working in a garage nearby was incensed at the thought of recommending a life of car repair to the younger generation, “no way,” he yelled, “why would anyone get into this industry? There’s no money in it at all.” Another nodded, adding that he’s in the process of joining the AA instead.
This was far from the only time money was raised when I asked technicians particularly, but also garage owners, about their jobs. In fact, among technicians it was almost a certainty that the response to anything would come back to pay – to the point where I just stopped asking. What was the point? I had a similar experience, but the inverse, with organisations, commentators, you know, the kind of people who appear in magazines; I would ask whether pay should be higher and the response would be that training, career progression, the working environment, inclusivity… you name it and it was more important than pay. I don’t like to let my cynical side take over too often but, try as hard as I might to see the positive side of the story, I remained resolutely unconvinced.
Then, as the pandemic restrictions began to loosen and confidence returned, the country went through… not exactly a boom, but the numbers went up – some more than others. Prices rose, jobs rose and, undeniably, wages rose – garages bore the brunt of all three. We devoted the first episode of the PMM Podcast to the rising cost of parts and the following two episodes to pricing jobs and hiring staff respectively. What we didn’t ask at the time, however, was whether staff should be paid higher, although one garage owner in Walthamstow, when I asked whether he was pricing his jobs too high, did memorably deadpan back to me “well, we’re not exactly driving around in Bentleys are we?”
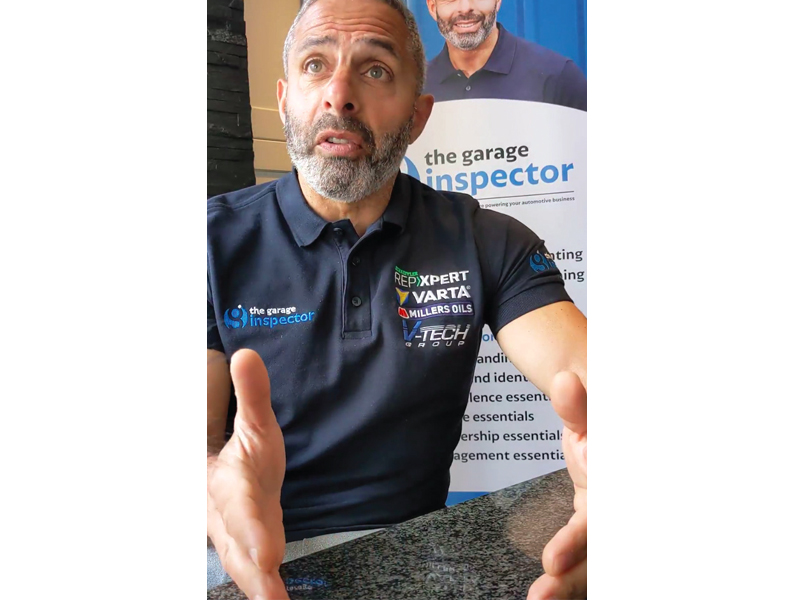
Well, quite. It’s hard to get a grasp on the true average pay for a technician in the industry, and of course it varies hugely throughout the UK, but I don’t think it’s an exaggeration to say some areas have seen quite considerable wage rises. This was confirmed when I spoke to Jennifer Webb, owner of HR Vitals, which is a company dedicated to improving worker relations in the independent aftermarket – if you’re thinking that sounds obscure, then I’m doing Jen a disservice. Hers was one of the busiest talks at last year’s Blend event and she has just started a regular column in this very magazine – don’t let the term HR put you off, she is talking to garages every day and is helping them create better teams in the workshop. When I put it to her that the number one complaint I’d come across was money, she argued that “on average, we [used to see] technician salaries between £26- 30,000. Now, it’s usually sitting around £35,000. Some even go as high as £50,000.” I spoke to Andy Savva, the Garage Inspector, in his kitchen in North London and he quoted similar figures: “What are you going to do –” Andy asked me, in the passionate way that he asks all questions, which makes you feel the weight of every word, “when a tech is already being paid 35-36 thousand, or in London, 38- 39 thousand, how much more can you offer them to come and work for you instead?”
Technology shift?
The latest figures from the IMI show that vacancies within the “motor trades” sector remain stubbornly high, despite having come down from 23,000 to 22,000. Per 100 employees, that represents a drop from 4.1 vacancies to 4 – the joint highest in the country, alongside “Accommodation & food service activities”. Where the latter category will be predominantly minimum wage jobs and will have seen its numbers decimated by Brexit and the minimum salary requirement for new migrants being set at a whopping £38,000, no such arguments can be made for the former category. The IMI’s own assessment for the automotive sector’s inability to fill job roles is due to the “increasingly technological advances” of modern vehicles – a.k.a, cars are getting too complicated to fix. Those same technological advances, the IMI goes on to argue, means a “rising number of technical roles … and in the near future means the pool of applicants is potentially wider than ever.” The press release goes on to wave the usual flag for “changing perceptions” to “attract talent from other sectors”.
Whilst cars are getting more complicated, and vehicle manufacturers are ramping up efforts to monopolise the more technologically advanced aspects of car repair, it’s hard to see how this is the explaining factor behind the major deficit in skilled workers that the industry is facing. Of all the people I’ve spoken to over the years about the skills shortage, no one has mentioned people leaving the industry due to repairs being too complicated and by the IMI’s own logic, it should have actually attracted more people into the industry.
I personally think it is unlikely the car repair sector will be attracting workers from other, more technologically focused sectors, in any great numbers any time soon, or ever, for that matter. But if wages have gone up as Jen and Andy say they have, why is there still such a huge skills gap? Well, according to the IMI, 18 per cent of vehicle technicians are over the age of 55, which means that rather than technology pushing technicians out of work, they’re probably just retiring as they normally would.
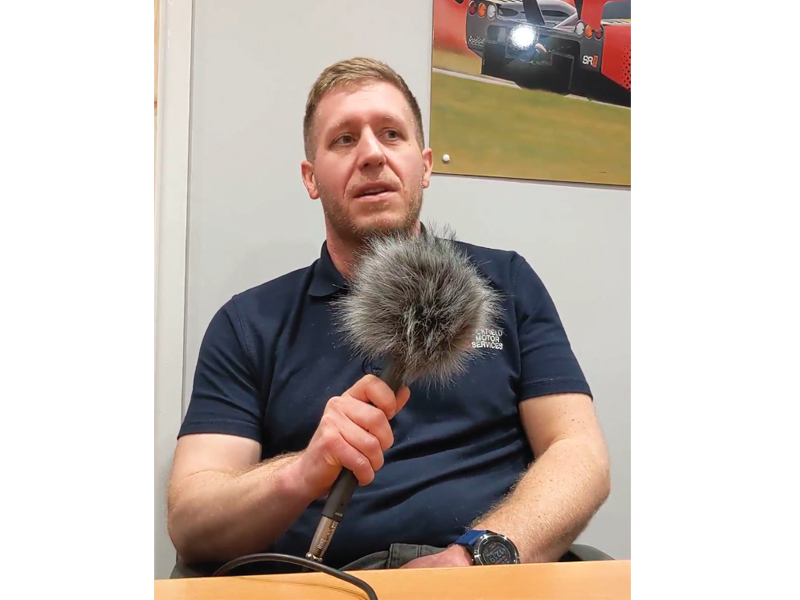
New blood
Two years ago I visited Brands Hatch to speak to Autotech Recruit’s Gavin White about what the industry needs to do to attract younger people into the industry, it rained quite heavily and you could hear that and the sound of the British superbikes whizzing by every few minutes. In other words, it was podcast gold. Gavin had brought with a young technician, Tom, who shared with me his thoughts on why people his age weren’t interested in going into car repair. Not only, according to Tom, was it down to the pay, but also the working conditions. Essentially, the job was too dirty for young people who like to be “clean and perfect” all the time – his words, not mine.
Again, like the rising wages of recent years, workshops are a lot cleaner and tidier than they ever were before. Visiting Edward Cockill recently at Uckfield Motor Services in East Sussex recently, I was shocked at how clean and tidy everything was – it felt more like a state of the art factory floor than an aftermarket workshop. Correspondingly, Ed consistently has at least one, and sometimes two, apprentices on the go at any one time. This summer’s Mechanex-PMM Live show saw garage owner Dean Lomas give a (largely improvised) talk on the importance of apprentices to his workshop.
The message from these garages is clear: you need to go the extra mile to attract staff. As Ed told me, “it is a bit of a pain, but you’ve got to look it as an investment.” Truth be told, I think both Ed and Dean enjoy giving young people in their area a chance, even if it doesn’t always work out. It might not be such a risk, however. GiPA’s Quentin Le Hetet explained, at last year’s IAAF Conference, that 80 per cent of workshops with an apprentice know that at the end of the apprenticeship, they will offer the apprentice a full time job. If that sounds suspiciously high, it might be because so few workshops have apprentices in the first place – 23 per cent. Meanwhile, according to Quentin, 90 per cent of independent garages claim it is “very challenging” to find workshop staff.
Three way problem
You might say there are three factors at play here: Firstly, workshops need to keep the staff they already have; secondly, workshops need to attract new staff; and lastly, the industry as a whole needs more staff.
Now wages have gone up and workshops have been cleaned up and order imposed, what next? Some fantastic workshops are still struggling to hire staff and especially young technicians. As the IMI report from earlier showed, there is simply a deficit of staff within the industry. Ironically, it is the shortage of staff which has pushed competition up and in turn made wages rise, rather than wages rising in order to attract new staff. Workshops are competing fiercely amongst themselves for a reduced pool of skilled technicians. If the workforce hadn’t been so restricted in the first place, wages never would have risen… it’s a cruel irony that to be paid a fair wage, the industry as a whole needs to suffer from a shortage of talent.
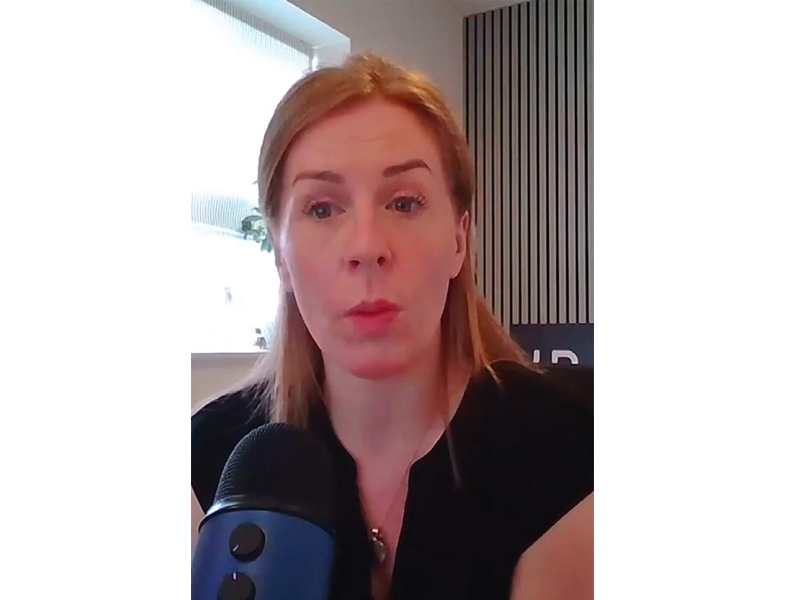
But why is the motor repair trade, which offers reliable employment filled with mentally stimulating tasks and a wide range of opportunities, not a more attractive prospect for young people? Andy puts it down, at least in part, to the Blair-Brown years: “I think we missed a whole decade, when people were told that in order to succeed, you must go to university.”
I attended university at the tail end of those years and I do agree, many people were told to go to university who really would have been better off doing an apprenticeship. I worked on building sites in between term times and quickly learnt that a manual job was in no way the “stupid” option compared to a graduate job. But it was exhausting and took up all my time as without the overtime the money wasn’t worth it. Andy’s suggestion on the PMM Podcast episode “The Skills Crisis: Is Money the Answer”, in which I spoke to Ed, Andy and Jen about how workshops can go the extra mile to attract staff, was a four day week. I couldn’t say whether it would work or not, but it’s certainly the kind of blue sky thinking this industry needs right now, rather than pie in the sky ideas about recruiting computer programmers to change clutches.
For more from this series, click here.