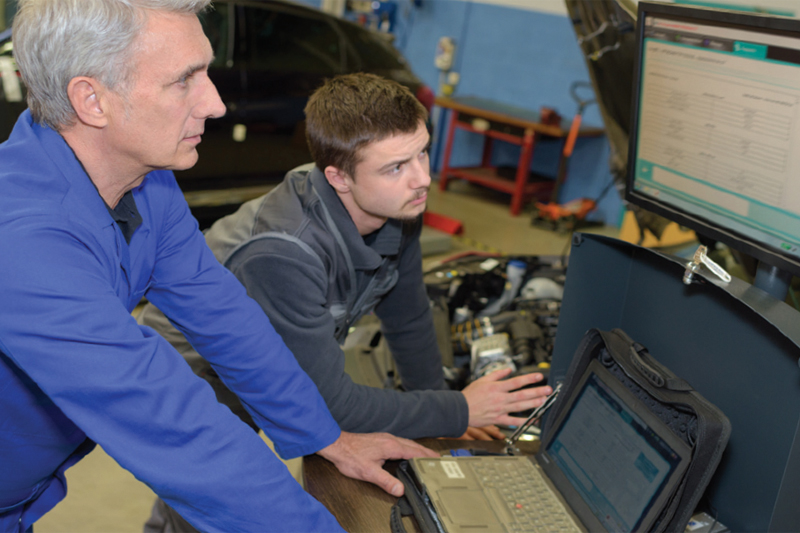
For this month’s Apprenticeship Answers, Gemma Westlake revisits the topic of the End Point Assessment (EPA), providing in-depth insight into exactly what is expected of an apprentice.
As promised in the previous article we will now be looking into the EPA (End Point Assessment) for apprentices in a little bit more detail. So, what have we already discussed? You may have read about how in the run up to the EPA, apprentices need to have completed a mixture of practical and written/online assessments alongside online gateway exams. To complete the actual EPA, the learner needs to have achieved both English and Maths at a grade four or above, achieved their F Gas certificate, and be deemed ready by both their mentor and workplace, who will have agreed in advance to enable the booking of the EPA.
As previously stated, the EPA then consists of an online exam, two days of practical assessments, and finally, a professional discussion. ‘What tasks can take up two days of practical assessments?’ I hear you ask. Well, it can differ for each learner. It is designed to highlight key skills that a technician would be expected to use in a workplace. This will include removal and refitting of components and fault diagnosis. There is some extremely helpful guidance that can be found on the IMI website.
The practical tasks to be completed can differ for a learner that is on the AP02 qualification compared to AP03 (AP03 being the newer version); if you are currently looking at finding your own apprentice, then it would make sense for us to look into the AP03 for now.
The practical section of the EPA is carried out over two days and is completed in EPA-approved centres. An independent assessor will observe the learner completing between four and six practical tasks. These tasks are designed to incorporate skills across nine different skill sets, as seen in the table on the IMI awarding website.
A good example of one such task would be removal and refitting of the cylinder head. The assessor expects to see that the future technician understands how to not only remove and refit components, but how to find technical information, such as bolt tightening sequences and tightness, and follow the correct procedure using equipment such as torque wrenches and angle gauges. This also includes removal, refitting and the correct procedures for the timing belt – again using (normally) online technical information from Autodata or similar.
Any fault diagnosis jobs would be expected to follow the same pattern; find and interpret the technical information, use a logical diagnostic approach with the information/wiring diagrams, and use the correct diagnostic equipment for the task to find and rectify the fault. A key component to any task (as it would be in a workshop) is to ensure that health and safety is adhered to at all times; the learner will be asked to identify health and safety risks for the job that they have been given. When each task is completed a clear and detailed job card is written out. Each task is given a time of 110% compared to manufacturer repair times and diagnostic time on top, and the learner is given instructions both verbally and in written form at the beginning.
I hope this has helped give a bit more of an insight into what can be expected. Join me next time to discuss education tactics, decreasing nerves, and how to prepare your apprentice for the learning process.