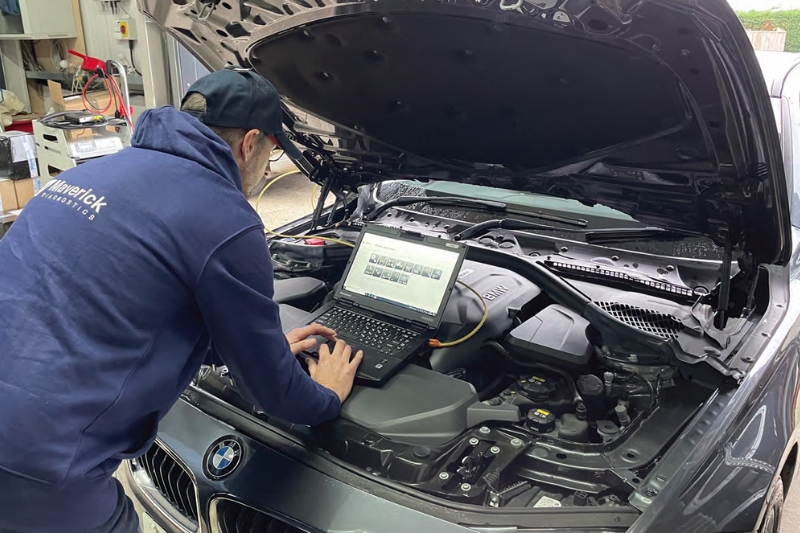
We asked founder of Maverick Diagnostics, Andy Brooke to give his unique insights on what you can do to futureproof your workshop and make the most of your investments.
Meet Andy
Andy Brooke, founder of Maverick Diagnostics, has dedicated over 30 years to the automotive industry, beginning his journey as a vehicle technician and regularly appearing in the pages of PMM. His extensive experience includes developing tools and diagnostic programs for both OEMs and the aftermarket, and he has become a leading authority on the challenges and opportunities facing independent workshops. Beyond running Maverick Diagnostics, Andy is actively involved in industry advocacy, working with the UK AFCAR Federation and the IAAF to protect the independent aftermarket’s interests. His work focuses on crucial issues like implementing block exemption and ensuring fair access to vehicle data and software in a post-Brexit world.
In the rapidly evolving world of the automotive aftermarket, workshops must be proactive to remain profitable and relevant. As someone who has spent over 30 years in the industry, from working as a vehicle technician to developing tools and tool programs for OEMs and the aftermarket, I’m here to share insights into preparing for future challenges, keeping workshops profitable, and, most importantly, making a return on your investments.
Take a good look around you
The automotive industry is undergoing significant changes, especially post- Brexit, with regulatory challenges like block exemption becoming critical to our market. As a member of the UK AFCAR Federation and the IAAF, I’m involved in initiatives to stabilise block exemption and ensure the independent aftermarket can continue to access necessary vehicle data and software. Vehicle manufacturers often make it difficult for us to use their software, and part of my mission is to assist the independent sector in these ongoing battles. So the question remains: how do we ensure our workshops are ready for these challenges and remain profitable?
Buy wisely
Diagnostic tools are essential, yet expensive, investments. To see the best return, you must not only own the right tools but also use them effectively. Unlike the early days when diagnostics relied on simple flash codes, modern vehicles are complex networks of microprocessors requiring advanced, fully guided diagnostics.
However, owning an OEM diagnostic tool is only beneficial if used by welltrained technicians. Too many workshop owners fail to invest in staff training, fearing employees might leave for better opportunities. Ironically, staff are more likely to stay if they feel valued and empowered through training. Workshops in other countries routinely charge an initial diagnostic fee, managing customer expectations and ensuring their time is compensated. UK workshops must do the same. Your diagnostic tools should pay for themselves by charging appropriately and showcasing the expertise they enable.
Managing expectations
An effective way to boost profitability is to manage customer expectations from the outset. When a customer books their vehicle in, use a comprehensive check-in form. Ask detailed questions: Has anyone worked on the car recently? Does the issue occur under specific conditions, like when the engine is cold? Recording this information not only speeds up the diagnostic process but also protects your workshop from potential disputes.
Customers must understand the value of your expertise. Instead of the old method of plugging in a tool for free, clearly outline the diagnostic process and associated costs. Every other country I’ve worked in follows this principle, and it’s time the UK aftermarket embraced it.
Give Google a miss
One common mistake is treating diagnostic trouble codes as definitive solutions rather than indicators. For instance, an air mass issue may not be caused by the sensor itself but rather an air leak. Misdiagnosis wastes time and money. Relying on accurate, up-to-date data is critical. Avoid the trap of Googling for answers; it often leads to confusion and misdirection. Instead, use reliable technical data sources or invest in a live vehicle technical support service.
Consider the OEM approach
Both OEM and aftermarket tools have their place in a workshop. OEM tools offer unparalleled accuracy and functionality, particularly for programming and module calibration. They provide a better return on investment because they allow you to charge higher rates and deliver superior service. Aftermarket tools, while useful for quick scans and simple diagnostics, cannot be relied upon for more complex jobs.
If you use an aftermarket tool for programming and something goes wrong, the vehicle manufacturer won’t have a record of the programming, and you could be left with costly issues. In contrast, OEM tools ensure the manufacturer can track and rectify problems, often saving money in the long run. Additionally, with the average UK workshop hourly rate at £75 and main dealer rates at £190, there is a clear opportunity to increase your rates when you use OEM tools.
Is remote reliable?
Remote diagnostic tools have gained popularity as a convenient solution for tricky situations. However, they come with limitations. Latency issues can make complex calibrations, such as steering rack or ADAS calibrations, unreliable. While remote tools are useful for quick fixes, investing in OEM tools remains more cost-effective for serious diagnostics.
Don’t be shocked by EVs
Electric and hybrid vehicles are here to stay. Whether you’re a petrolhead or not, the numbers and policies don’t lie. These vehicles are complex, with multiple water pumps, heaters, and systems that require specialised knowledge. EVs and hybrids will need fixing just as often as traditional cars, if not more, as they age. Training in EV diagnostics is crucial. Don’t just settle for basic courses; go further to fully understand these vehicles and their systems.
Specialising for success
Consider specialising in certain brands or types of vehicles. Research the vehicles commonly seen in your area and what main dealers are nearby. Specialisation reduces tool costs and increases efficiency, as you’ll become an expert in diagnosing and repairing specific makes and models.
Fix that Wi-Fi!
A key component of future-proofing your workshop is investing in robust IT infrastructure. Cloud-based diagnostics require a reliable internet connection. Gone are the days of running OE tools off a mobile phone or relying on slow Wi- Fi. Ensure you have wired computers, fast broadband, and adequate IT support.
The bottom line
The future is here, and it demands action. Start investing in training, tools, and infrastructure today. Your workshop’s survival depends on it.