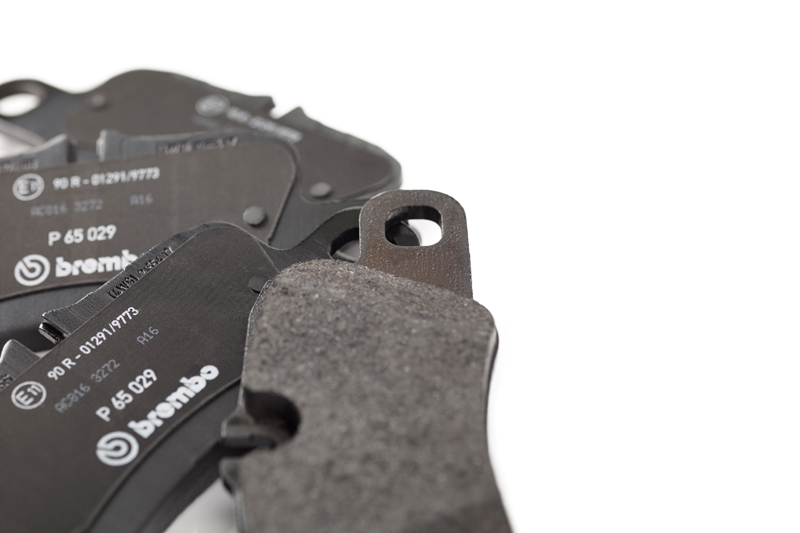
Brembo takes a look at noise, vibration and harshness in brakes and what can be done to reduce them.
Brembo works with vehicle manufacturers that provide exact information such as the weight and specifications of the parts surrounding the brakes to produce the most efficient braking systems for the vehicle. Using this information, we design the brake components of the exact type and dimension for optimum performance, while maintaining the utmost level of comfort when braking, without sacrificing any friction coefficient. One of the highest demands from potential car owners is comfort while driving.
However, in order to provide more comfort with our brakes, we need to understand what NVH is and how it is caused. In part one of this series, we will go through NVH produced by brake discs and discuss the solutions taken to reduce uncomfortable braking.
NVH is defined as Noise, Vibration and Harshness and affects ride quality, driveability and occupant comfort. The examples of NVH commonly experienced in braking systems range from the high pitched annoying squeal to an uncomfortable sensation from vibration and harshness. Although most of the time these issues rear their head when braking, there are instances that this can be experienced without the brakes being applied and this occurs with mechanical defects of components usually through wear and tear.
To reduce NVH, there are several factors that the engineers need to bear in mind when designing the braking systems of a vehicle. They need to bear in mind not only the components of the braking systems, but the surrounding components, how they perform or react when in motion, exposed to heat and what happens to them through normal wear and tear. They need to factor in that these elements are variable subject to the amount of use or exposure to the environment, so it is important to bear in mind that although the design of a brake component will reduce NVH when components are new, there are still preventative measures that need to be followed to prevent NVH as the components age.
Noise, vibration and harshness are closely related to each other in the way that they are produced. Noise is unwanted sound. Any object that vibrates will create a sound. When an object vibrates, it tends to vibrate at a particular frequency or a set of frequencies. The frequency or frequencies at which an object tends to vibrate when “disturbed” is known as the natural frequency of the object. If the amplitudes of the vibrations are large enough and if natural frequency is within the human frequency range, then the vibrating object will produce sound waves that are audible. The slower the vibration or lower the frequency will manifest from a low pitched sound into more of judder sensation as the frequency decreases. Low frequency vibrations can form due to the natural characteristics of the brake disc material referred to as “thermoelastic deformation” when exposed to heat and in motion. Brake discs are mostly made out of metal and when exposed to heat their natural characteristics cause them to expand but also flex slightly.
There are two main vibrations groups: cold judder and hot judder. Cold judder is a vibration phenomenon occurring during braking caused by geometrical irregularities due to machining, mounting, uneven wear, or uneven friction. Hot judder is a vibration phenomenon occurring during braking caused by the formation of dark ‘hot spots’ on the disc. These are caused by a transformation of the cast iron itself (due to overheating) or by localised deposits of friction material.
There are several solutions taken to prevent NVH in the design of a brake disc. Brembo uses more than 40 different variants of cast iron, to reduce hot and cold judder by using a high carbon cast iron that has different elasticity to improve damping thus reducing the effects of judder.
The surface of the brake disc must be smooth to prevent pad vibration as it makes contact. Corrosion will affect this. To prevent corrosion of the brake discs before being fitted to the vehicle, Brembo brake discs are finished with UV paint treatment that provides a smoother finish, with no risk of remnants embedding the friction material during the bedding in process.
The microstructure of the brake discs is individually tested to ensure that it can withstand braking forces. Besides strength, the physical structure of the brake disc must be in tolerance. When a disc is brand new, the maximum tolerance of run out measurement and Disc Thickness Variation is less than 50-80% the width of a human hair. And these measurements need to be this exact to prevent brake torque variation that would replicate that judder symptom.
The way the disc is connected together in terms of the hat to the braking surface can influence NVH, there has been innovation more commonly known as the two piece brake discs. This innovation not only offers a 30% weight saving on the unsprung mass by the hat being manufactured in lighter materials but also provides for flexibility of the braking surface without distorting the hat. The braking surface can be attached to the hat by fastening bushings to connect the two parts, allowing the braking surface to expand without deforming. Another alternative is joining the two surfaces together by co-casting. These solutions should not be swapped with a single piece brake disc. Doing this can affect the overall stability by increasing the unsprung mass and decrease the NVH damping effect without the before mentioned technology.
NVH prevention goes further than just the surface of the brake disc – the internal venting designs are much more complex due to the ventilation chambers inside used to dissipate the heat as quickly as possible. The shape and distribution of the pillars creates air circulation inside the ventilation chamber, which allows for greater heat removal, as well as an increased resistance of up to 40% against the formation of cracks. The latest-generation of Brembo brake discs, the patented pillar ventilation technology are designed with pillars with a different geometry and are arranged along three rings on the braking surface.
Each disc is checked and, if necessary, balanced automatically during production. Discs are checked on an electronic test bench which spins the disc and measures any imbalance. If any imbalance is detected, the excess material is ground away to balance the disc perfectly. If unbalanced, this will affect the comfort of the driver and cause premature wearing of surrounding components. Not all discs need correction, and the majority are already perfectly balanced, making it unnecessary to machine material from the outer edge. This means that some discs may have a notch while others do not.