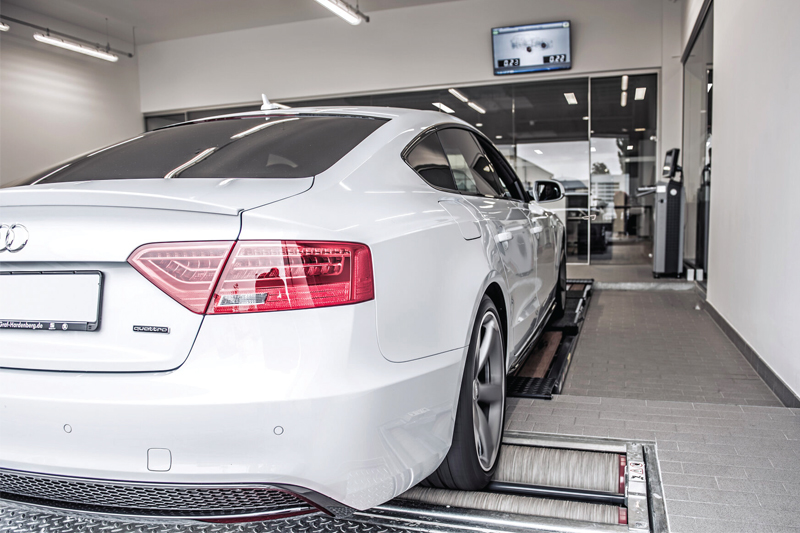
With MAHA UK’s engineers used to getting underneath vehicles, the workshop equipment supplier understands the role of safety in technicians’ work. In this article, MAHA UK offers a safety briefing to keep technicians and the vehicle they’re working on safe.
When it comes to setting up a brake tester, like MAHA UK’s MBT 2250 EUROSYSTEM, nothing should be left to chance. The installation and setup of equipment should always be done by a suitably trained service technician to ensure that individuals with the right training and expertise can handle this critical task.
Potential hazards, such as electrical equipment near moisture or improper installation locations can be expertly addressed by a qualified technician. By entrusting professionals with the installation process, risks are minimised.
This is the MAHA UK approach – and here are some top tips for using a brake tester correctly and safely:
Qualified personnel: Only trained individuals should operate a brake tester, strictly following its performance limits to ensure safety and accurate testing.
Maintain a clean environment: Keeping the area around the brake tester clean is vital for safety and equipment performance.
Secure shutdown: When the brake tester isn’t in use, turn it off and secure the main switch with a padlock to prevent unauthorised use.
Emergency procedures: In case of an emergency, users should know how to use the main switch or emergency-stop switch to promptly shut down the system.
Ventilation: Adequate airing is essential to prevent carbon monoxide poisoning when operating a vehicle engine in enclosed spaces.
Danger zone inspection: Prior to driving a vehicle onto the tester, inspect the danger zone for potential safety risks.
Roller drive caution: For vehicles with a driven axle on the roller set, exiting should only be done with the roller drive running to prevent roller damage and to assist exit.
Maintenance matters
Even during maintenance and servicing, the message remains as stringent. Here’s what MAHA UK recommends:
Professional service: Service work should be carried out by qualified service technicians or authorised service partners to guarantee expertise.
Electrical work: Only those suitably trained should handle electrical parts of the system.
Secure shutdown: Before performing repair, maintenance, or setup work, turn off the main switch and secure it with a padlock.
Fire hazard prevention: Regularly clean the roller set to prevent fire hazards caused by rubber abrasion before any maintenance work begins.
Overheating awareness: Exercise caution regarding overheating parts when working on the control cabinet or roller sets.
Emergency response: Reassuringly, from MAHA UK’s perspective, motors are isolated by disengaging the motor protection switches during maintenance/calibration, to avoid accidental start-up.
MOT Equipment
MAHA UK’s 2250 EUROSYSTEM is a connected roller brake tester approved by the DVSA for MOT testing. Designed for class 4 and 7 vehicles, the it is appropriate for cars and vans with an axle load up to 3.5t. Built for high volume and repeatability, this piece of equipment aims to provide MOT testers with consistent and clear results.
MAHA UK Managing Director, Neil Ebbs, said: “From installation, servicing, calibration and repairs, we’re committed to supporting both car and commercial vehicle workshops. It’s vital that workshops run safely and efficiently, providing technicians with confidence in the equipment they are operating.
“Our service engineers are only a call away reacting to customer needs. MAHA UK calibrates the equipment at the point of installation, along with offering a calibration, service and maintenance contract for extra peace of mind. Our after-sales support, as well as warranty packages, ensures we’re supportive of our customers throughout the equipment’s lifetime.”