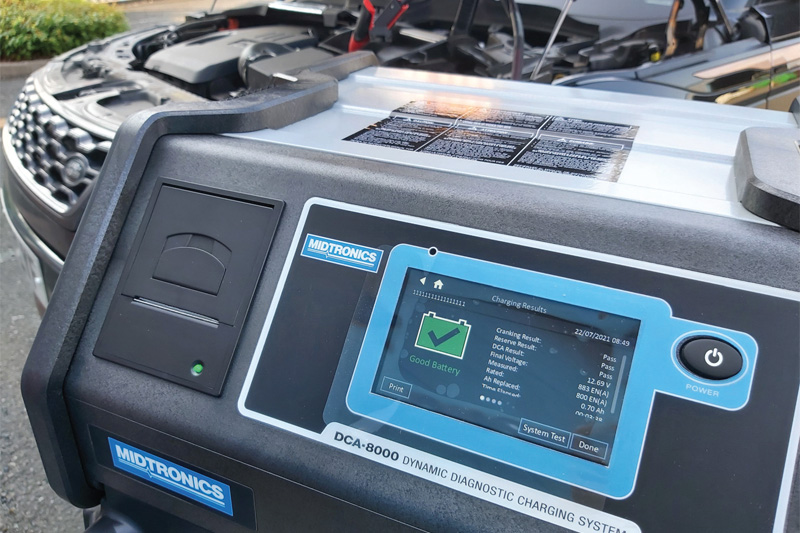
A recent webinar revealed some very interesting facts to the Rotronics team about technicians’ approach to battery management. Here, Managing Director of Rotronics, Ken Clark emphasises the importance of testing and charging vehicle batteries.
As part of a recent meeting, hosted by the IMI, an interactive Q&A session gathered key information from the broad audience, including technicians, workshop owners and managers, about their battery management practices. Interestingly, 63% of the participants said that they test every vehicle that comes into their workshop, however only 31% charge every vehicle.
Ken Clark, Manging Director at Rotronics, said: “We had hoped that the testing percentage figure would be a lot higher because we know that our customers who test and charge every vehicle reap far higher efficiency rewards and return on investment than those who do not. The percentage of those who charge each vehicle on entering the workshop was a real surprise. Only 31% is a low figure and shows that there are far too many vehicles that are not charged to the optimum level.
“With so many of our participants answering that they do not test and charge each vehicle, this means that a large percentage of battery defects will be missed and this is likely to result in higher battery replacement budgets. The DCA8000 is excellent technology to help workshops get around this issue.”
For the independent workshop, the DCA8000 is a complete battery management programme to look after your customers. Technicians will get one of two results, Good or Bad. Batteries that just need charging will be fully charged, with the DCA giving you an estimated charge time, to assist with your workshop productivity. The charge time will range from 20 mins to an hour, therefore within reasonable service time and it delivers 70amp power.
The uniqueness of the DCA8000 is that it fully diagnoses the battery and will measure the charge acceptance level, the reserve capacity, and the cranking ability of the vehicle. It has a full view of a battery’s health by looking at the power demands and charge acceptance.
This is a dynamic and workshop-saving diagnostic tool for all 12V applications that Rotronics has in its arsenal and is ideal for PMM readers. It does not waste hours of charging, and it reduces those inefficiencies of testing and charging separately.
It is a breakthrough for independent workshops to reduce downtime, and increase their diagnostic capability, like no other technology before. This means 100% first time fix, as there is no need to charge the battery up to retest. Customers get the right result first time, and they will always have a charged battery when the vehicle is returned.
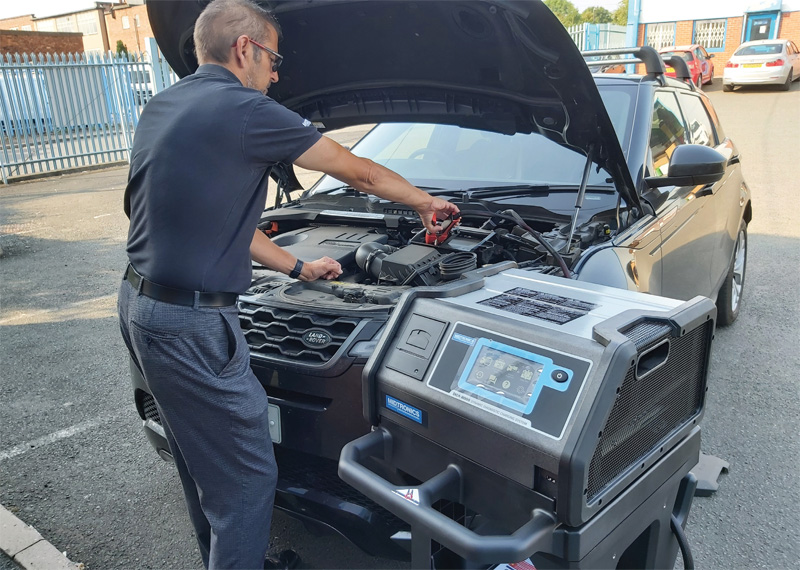
The DCA8000 report provides the test result, the charge time and how much the current has accepted. This provides justification for any charge that the customer may receive; this is a transparent process that adds value to your service time. This gives workshops the option to charge for this service as a valuable add-on to their workstream with little or no impact to workshop productivity.
During the Rotronics webinar, it emerged that 76% of the participants rarely or never have their battery management equipment serviced, repaired or calibrated. Only 18% claimed to have annual servicing and a mere 6% adhered to the requirements set out on the equipment guarantee.
Ken Clark comments: “This tells us that many workshops are using equipment that may not be fit for service or providing accurate results. Most of the battery management technology needs an annual service and repair and calibration should be carried out to ensure that testers are providing readings within specific tolerance levels and are working optimally.
“Our service and repair centre on the website provides invaluable guidance, (see link below) for finding out how to get the most out of your technology.”
Ken talked about how to get the best return on investment from battery equipment, and the importance of using the latest conductance profiling technology and showed the payback of using the Rotronics online reporting platform, ROBIS, with remote reporting.
Continues Ken: “Interestingly, only 5% of the participants thought that a battery management programme, testing and charging, was part of a good customer service programme. In the independent workshops, there could be a very strong customer service message, with added revenue opportunities, offering testing and charging as part of an ongoing programme to keep their customers’ vehicles in optimal working condition.
“On the positive side, nearly 60% of those taking part in the poll believed that testing a vehicle battery is good practice and provides preventative maintenance. The important piece to factor in now, is to improve the testing and charging percentage, to make sure that failure prevention is in day-to-day practices.”