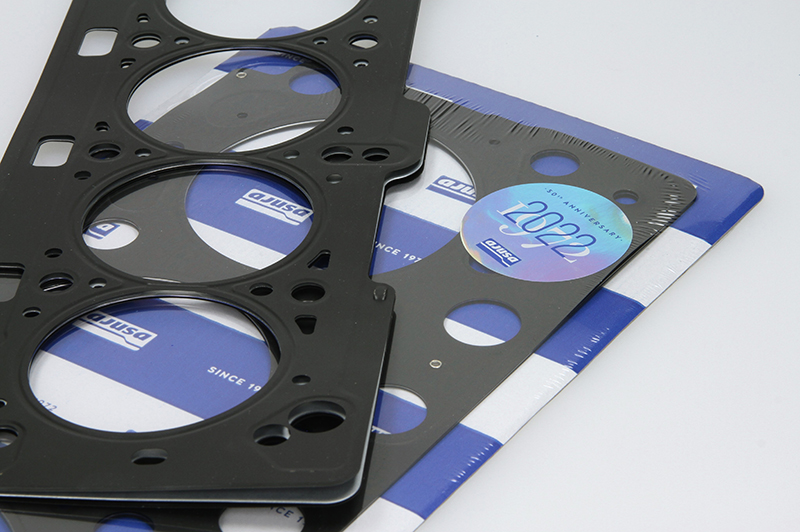
Ajusa charts the evolution of the cylinder head gasket.
There are different types of cylinder head gaskets depending on the materials used in their manufacturing. In the market, Ajusa offers a complete coverage of cylinder head gaskets from FibreMax, MLS and Metal-Elastomer. The evolution and changes in the materials used in the manufacture of gaskets can mainly be put down to the changes of the engine.
The cylinder head gasket is the most important gasket in the engine. The main function is to seal the combustion chamber, the water and coolant holes between the block and the cylinder head.
Current engine design is based on several points:
- Manufacturing engines more powerful with a better advantage of the thermal cycle, leading to increasing temperature and pressure inside the combustion chambers
- New engines are smaller and lighter to save fuel, leading to the use of aluminium and light alloys compared to the old engines that were entirely steel casting. As lighter metals are often softer, they are more sensitive to high temperatures, so the expansion and contraction of the engine is greater
- Authorities demanding more regulations on engines, so they generate lower emissions
Therefore, we need cylinder head gaskets that resist high temperatures, enable the engine to expand and contract, to resist dilatation and contraction of the materials, can withstand the attack of chemical products of the antifreeze and additives. All of this while sealing the combustion chambers, the cooling and lubricating circuit during engine lifetime. Engine component manufacturers solved these challenges with the development of the MLS gasket, substituting the classic fibre head gasket.
Multilayer gasket
Multilayer gaskets are composed of several sheets of steel in different thickness and different types of materials.
The different types of sheets that we can find in this type of gasket are:
- Spacer layer – it is a layer made of stainless steel which varies in thickness providing different thicknesses to the gasket
- Functional layer (external layers) – it’s a layer of cold-rolled stainless-steel and is the one which contains the sealing beads
- Stopper layer – used to increase the sealing pressure around the combustion chamber and to reduce the deformation of the beads which are in the functional layer, moreover, increasing the durability of these and therefore of the gasket
- Reinforcements/sealing ring – made of metal, elastomer, copper, etc. to prevent contact of different additives with the gasket
Elastomer coating is applied between the layers to improve the sealing capabilities, and to absorb vibrations in the engine. The distribution of previous sheets will depend on the requirements of the engine.
Fibre head gasket
The classic fibre head gasket is a compressible flat gasket. It’s composed using a stainless-steel layer compressed between a fibre material layer on both sides. The gasket contains metal rings around the cylinders to increase the sealing pressure and to avoid contact with the high temperatures produced inside the combustion chamber.
A silicone coating is used to prevent swelling of the fibre by contact with the antifreeze. It also helps to adapt the gasket to the different roughness present on the surfaces of the cylinder head and engine block.
The Viton coatings (elastomeric materials) ensure continuous contact with the surface so that areas such as oil passages holes are sealed at high pressure, creating a barrier which prevents leakage inside the engine.
Reinforcements of metal, elastomer, copper, etc. are introduced in those holes where it is necessary to avoid contact with different additives.
Due to the changes mentioned above in current engines, the fibre gasket is being progressively replaced by the MLS gasket, which adapts to the increases of engine requirements and provides a better seal.
Metal elastomer gaskets
Unlike the MLS gasket where the ribs are metallic, in this type of gaskets the ribs are made of elastomer, except for the rib that surrounds the cylinders, which is still metallic due to the high temperatures it supports and is made up of a single sheet of steel from 0.5 mm to 2 mm thick.
Due to the high stiffness of the joint, they are very common in industrial applications, such as buses and vans, where the demands are greater than in conventional vehicles.
Cylinder head gasket assembly tips
- Let the engine cool to room temperature – this is very important for aluminium cylinder heads
- Open the cap of the expansion tank of the cooling system
- Loosen head bolts in reverse order of tightening
- Clean and degrease block and cylinder head – it is important that the block and cylinder head are complete clean and free of any dust or particles
- Introduce a tap tool with the same metric and pitch as the bolts into the housing of the block. Remove any dirt by blowing or vacuuming inside the bolt housing
- Check the flatness of the block and cylinder head by the gasket surface. Deformations must not exceed, in general, the value of 0.5 mm. Depending on engine, this value can be different. In case there is any deformation higher than allowed, the cylinder head and block must be resurfaced. Once the block is resurfaced, you need to measure the height of the piston to the height of the block to choose the correct cylinder head gasket thickness. If it is not necessary to resurface the block you can assemble a new cylinder head gasket that has the same thickness as the one that was removed
- Check that the roughness of block and cylinder head are within the parameters allowed
- Check the height of cylinder sleeve to block’s plane