TRW Aftermarket looks at the development of steering systems to meet the ever changing needs of the customer and important industry trends.
The demands on global vehicle manufacturers (VMs) to reduce vehicle weight, cost and hydrocarbon emissions are omnipresent. In turn, this places more and more pressure on parts and systems manufacturers to develop new fuel-saving technologies or to improve existing ones.
A leader in this field is ZF Group, owner of the TRW brand. The business invests approximately five percent of its sales in Research and Development (recently €1.4 billion). This ensures its customers get the most up to date technology and goes a long way towards making the world’s roads safer.
A simple way to preserve fuel consumption in this area is to disconnect conventional steering support from the engine when it is not needed. With a conventional hydraulic servo steering system, the power steering pump is driven by the engine via a V-belt or ribbed belt. This method means the pump is in continuous use even when the driver isn’t steering; using an unnecessary amount of energy and fuel.
Electrically Power Hydraulic Steering (EPHS) systems
A fundamental in steering development was the revolutionary replacement of the belt-driven power steering pump with an electrical one. Known generically as Electrically Power Hydraulic Steering (EPHS) systems, certain types use only 25 percent of the energy of a conventional system.
EPHS is a ZF TRW electrically assisted steering solution which combines advantages of electronically controlled on-demand steering with robust hydraulic actuation. ZF TRW’s EPHS is a compact Motor Pump Unit (MPU) connected with a conventional rack and pinion power gear.
As with other electric steering solutions, EPHS is independent of the combustion engine. The system requires comparably low application development costs – an ideal solution for hybrid electric vehicle platforms.
Compared with traditional hydraulic power steering, EPHS systems offer a fuel saving of up to 0.3L/100km and a reduction of carbon dioxide emissions of approximately 7g/km.
ZF TRW offers different feature and power levels of EPHS, which cover A/B segment applications (GenB) up to applications with a maximum rack force of 18kN (GenC) – extending the benefits of electric steering to larger vehicles, including SUVs and delivery vans. In terms of software tuneability, EPHS delivers a number of benefits to steering feel, such as speed proportional functionality and general customizable steering properties.
Electric Power Steering (EPS)
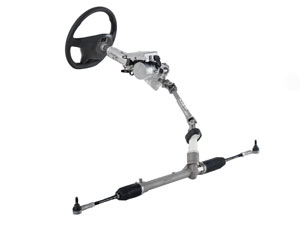
The next step in the evolution of steering development is complete electrical systems. Commonly known as Electric Power Steering systems (EPS), they offer even greater fuel economy potential. In addition, they play a major role in environmental protection due to the absence of any hydraulic fluid.
One of the products in the EPS range is the electrical servo steering system with steering column drive (Column Drive EPS).
Originally designed for small-car segment, ZF TRW’s Column Drive EPS has evolved into a family of modular and scalable solutions supporting a range of steering rack loads from 4.0kN to 10kN. One of the major benefits of the Column Drive system is its clever packaging which can be tailored for a broad range of vehicle applications while still reducing life cycle costs.
Its modular and scalable architecture allows for great freedom of packaging and tailored design for a broad range of vehicle applications while reducing life cycle costs. Its location in the passenger compartment enables reduced temperature and sealing requirements compared with systems situated under the hood. Used in more than 26 million passenger cars in every region of the world, ZF TRW’s Column Drive EPS technology delivers a cost-effective and fuel efficient steering solution while being fully capable of 5* NCAP crash requirements. It provides class-leading steering dynamics and intelligent actuation for the fast growing field of Driver Assistance Systems (DAS) and automated driving.
Rack/Belt Drive EPS
For larger and premium segment vehicles, ZF TRW’s Belt Drive EPS (also referred to as Rack Drive) is a solution that integrates a brushless motor, toothed belt, and ball nut assembly with pulley and bearing in one unit. This setup results in lower inertia and friction for high power applications, as well as a very direct steering feel and superior response. As with the Column drive technology, ZF TRW’s Belt Drive EPS system has been designed as a modular and scalable architecture to offer great freedom of packaging and tailored design for a broad range of vehicle applications. Its Electric Power Pack (EPP), an integrated motor and ECU, comes in both an axial and radial package options. Each of these in turn can be flexibly packaged around the steering gear in both in-board and out-board configurations.
Belt drive technology is particularly suited to cars within the European D (US Midsize) segment and above, and the ZF TRW Belt Drive systems operate directly from 12V power on rack loads up to 18kN. The system shares a “mechatronic core” (system architecture, safety, sensor, motor, ECU and software designs) with its Column Drive cousin. With no energy drag on the engine, EPS systems offer a fuel savings of up to 0.33L/100km, with a corresponding reduction in carbon dioxide emissions of approximately 8g/km.
ZF TRW continues to make major advances in this area. A new prototype that combines technologies from ZF and TRW could help improve safety as well as performance in partially and fully automated vehicles.
The test vehicle uses TRW’s new dual pinion EPS on the front axle and ZF’s Active Kinematics Control (AKC) by ZF on the rear to improve vehicle control. It illustrates how safety and driving comfort can be significantly increased when well-established and proven systems are perfectly tuned to work together.
At low speeds, AKC moves the rear wheels in the opposite direction to the steering angle of the front wheels. This reduces the vehicle’s turning radius helping to improve driver comfort.
At higher speeds, the rear and front wheels steer in the same direction improving the vehicle’s stability. When all wheels steer into the same direction, the vehicle rotation around the vertical axis is reduced, enabling safer driving.
Even during lane change manoeuvres on low-mu surfaces, the car stays on course. Connecting the two steering systems could also be leveraged for automated vehicle functions. The prototype demonstrates an effective steer by-wire control concept. This could be used to control autonomous overtaking and lane change manoeuvres with greater precision.