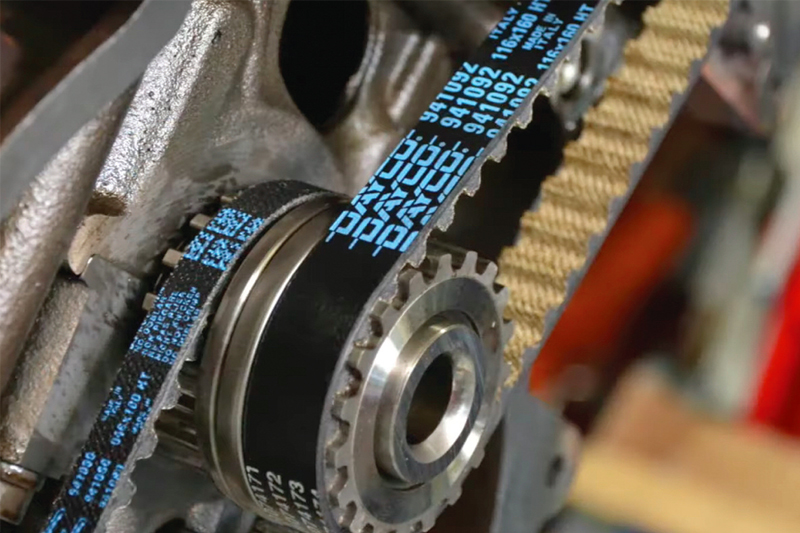
Dayco’s national sales manager Steve Carolan reminds readers of the benefits of belt-in-oil timing drive systems and the replacement opportunity they provide independent workshops.
Although some might question the validity of the concept, preferring the traditional chain drive solution, the fact that many VMs have long since moved to belt driven timing systems and a growing number are adopting the BIO route, means that the replacement process, driven both by the scheduled service interval and by a repair requirement, will be a more frequent workshop activity.
To help ensure the ongoing reliability of these engines, Dayco, as the pioneers of BIO on behalf of VMs such as Ford, PSA and VW, has for some time been highlighting the importance to workshops nationally of carrying out regular maintenance in line with the VMs scheduled service intervals. This is because, apart from the catastrophic consequences that would result from belt failure, belt degradation can also have serious implications to several other components, such as the oil pump and brake system vacuum pump.
BIO is a fantastic solution that helps small and efficient engines to deliver increased levels of power, alongside lower emissions and better fuel economy, primarily because it reduces friction in the drive system by up to 30 per cent. However, to maintain this level of performance and to continue to operate as the manufacturer designed, they need to be serviced regularly and the condition of the belt assessed.
Replacement tips
Naturally, should the belt need to be replaced, as the original equipment supplier for many BIO applications, we have replacement kits in the Dayco aftermarket range and this provides workshops with a genuine revenue opportunity because over the last year, our sales of BIO kits have doubled, which proves there is a growing demand for the parts and means they can directly benefit from the BIO revolution.
Following developments at the OE level, Dayco has superseded its original replacement kits for the 1.2 petrol engine used in many PSA applications, such as the C-Elysee, C3, DS3 and Expert, and the 1.2 diesel engine for models including C3, C3 Picasso, C4 Cactus, 208, 2008, 308 and 3008, previously KBIO07 and KBIO08, with KBIO14 and KBIO15 respectively.
Alongside the positive revenue generation benefits that the growth in BIO applications provides, Dayco remains active with the workshop, delivering technical messages, ongoing training and general support, all of which helps to promote sales and reduce the risk of returns and unnecessary warranty claims.
Part of this process is to react effectively when problems appear, quickly diagnose why they are occurring and then highlight the issues to workshops and technicians, so they are able to follow the correct fitting procedure to replace them successfully, which will increase customer satisfaction and avoid unnecessary warranty claims back to the factor.
A perfect example is the two-stage tensioning process that must be carried out when replacing the timing belt on the 1.6 and 2.0-litre HDI engines that are widely used by Fiat, Ford, PSA and Vauxhall, in many of their popular models in both passenger car and light commercial vehicle applications. Although the consequences of not following the procedure may not be immediate, because both units are of an interference design, the effect of a subsequent belt failure is likely to be catastrophic to the engine.
Another topical example concerns oval crankshaft sprockets, which also require specific belt tensioning requirements that if not followed, can end up stripping teeth from the timing belt for example. What these examples demonstrate is that even a scheduled service requirement on comparatively common engines requires technicians to follow a specific procedure, not apply a general rule.
EVs incoming
Returning to a subject much discussed within the industry as a whole, but in the aftermarket particularly, it’s worth reminding workshops of the realities of the electric vehicle revolution when it comes to the products that will still be required daily for the foreseeable future. Although the industry needs to be ready and react to a growing demand for EV specific replacement parts, the reality is that the vast majority of the vehicles that will enter the independent workshop for the next decade, will have an internal combustion engine (ICE), whether petrol or diesel.
Keeping up with demand
This growing demand for EV parts combined with the reality that ICE vehicles will still be around means that workshops need to keep up to speed with the current technology and be in a position to tackle the immediate needs of motorists and be able to carry out a first rate job first time. This is not to say the industry should be complacent and ignore the upcoming developments in the market and take advantage of the opportunities they present. However, foregoing training and learning more about the best practice service and repair requirements of ICE powered vehicles, which are still becoming ever more complicated, in favour of alternative fuel technology, doesn’t seem a wise decision, while ICE is, and still is likely to be for the next decade, the main revenue source for the typical workshop.
So, picking back up on the subject of BIO, belt and component replacement of these systems will be around for the long term, because even if the move to outlaw the sale of ICE powered vehicles by 2035 does happen, the fact is that the 2.0-litre TDCi engine used in models such as the Ford Transit, is still planned to be in production until 2030, so the newest vehicles are unlikely to enter the aftermarket until 2033.