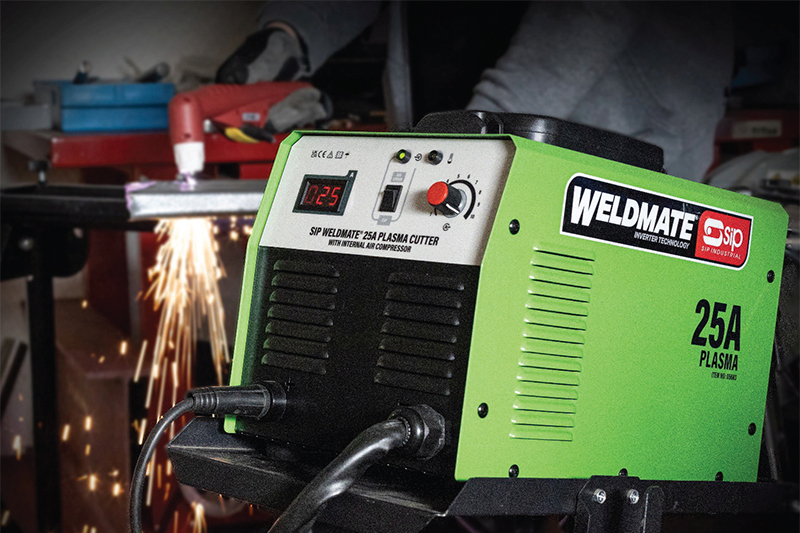
SIP Industrial Products is here for your classic car welding needs.
SIP Industrial Products has launched its new welding and plasma cutting range that covers it all; including professional ranges for automotive and classic car restoration. But what do you need to consider when restoring a classic car?
Restoring a classic car can be a rewarding endeavour for any enthusiast or professional mechanic, bringing life back to an old machine, but it isn’t a task that should be taken lightly. Welding plays a huge part in the process and we are here to explain the challenges that you are likely to encounter and advise on the optimum methods and products to use.
Material condition
Most classic cars suffer from corrosion due to age. Metals were thicker when manufactured but have since weakened, requiring careful heat control during welding to prevent distortion and burn-through while ensuring strong welds. Rust is another common issue, particularly around footwells and structural components. Often, restoration starts by cutting out rusted sections and replacing them with new material.
Body shapes, contours & alignment
It’s safe to say that classic cars have plenty of personality and usually come with more distinctive and unique body shapes compared to modern vehicles. Achieving seamless welds and maintaining original contours is vital.
Proper alignment is also key – misaligned panels and inaccurate measurements can undo hours of work. Keeping weld pools neat and consistent preserves the classic look and feel.
Metal compatibility
Times have certainly changed, and so have materials. The majority of classic cars were manufactured using mild steel, with high-strength alloys being used to reinforce some components. Because of this, it’s crucial to select the correct welding process and filling materials for your car. Strong and durable welds need to be achieved, and you need to make sure you’re choosing the right materials to be successful.
Structural damage and integrity
Classic cars might look great, your panels might be aligned properly and your welds nice and neat, but what lies under the body is equally as important. Classic cars will often suffer a lot of hidden damage. It’s important that a full assessment is undertaken. The structural integrity of the car must be solid to maintain safety and performance.
Now you know these considerations, what welding methods do you need in order to complete these tasks?
Choosing the right welding methods
Restoring a classic car to its former glory requires skill and the right welding techniques. For thin and sensitive body panels, DC TIG welding is the ideal choice, producing strong and consistent welds when paired with the correct filler materials. For easily accessible panels, a handheld spot welder is useful for achieving quick and consistent welds.
When working with clean metals that have multiple layers,MIG spot welding – also known as “puddle” welding – is a great option, reducing distortion and improving strength. If dealing with overlapping materials, drilling a small pilot hole can help form a strong weld puddle.
For panel joints, stitch MIG welding is effective in reducing distortion and providing flexibility while controlling heat. Welding butt clamps ensure correct alignment and spacing between materials for optimal results.
When it comes to cutting rusted panels, plasma cutting provides a cleaner and more precise alternative to grinders, making it easier to prepare areas for patching and welding. They generate a lot of heat in a very small area, making them quick, neat and ideal for cutting out new panel shapes and accesses when used with a template.
When dealing with body panels, it can also be important to shrink the sheet metal and stiffen your body panels to ensure strong shape. This is commonly achieved with a gas torch and compressed air or a wet rag. To remove “oil canning” you first heat up a specific area of the panel and then cool it down. This method shrinks the metal, eliminating the oil canning effect. In the modern world, it’s much more efficient to use an induction heater to create the same result.
A handheld induction heater with a flat pad is a controlled and flame-free way of heating the material, ready for cooling and shrinking.
New range
SIP launched its new Weldmate range off the back of 50 years specialising in welding. The range includes MIG and TIG welders, handheld spot welders, plasma cutters, headshields, accessories, and welding consumables – everything needed for classic car restoration. Fully compliant with EU 2019/1784 (Eco Design for Welding Equipment) all of SIP’s welding machines feature fourth generation inverter technology with over 80 per cent efficiency. The majority of models in the range include infinitely variable synergic controls for 1-dial control, providing a smooth, stepless output adjustment which ensures a higher-quality weld and better temperature control.
Restoring a classic car requires skill, patience, and the right equipment. With SIP’s new range, you can achieve precision, strength and efficiency in every weld. Whether tackling corroded panels, delicate bodywork, or structural repairs, the right welding solutions make all the difference.
So, are you ready to bring a classic back to life? With SIP backing you with the right tools for each welding process, the challenge is yours to take on…