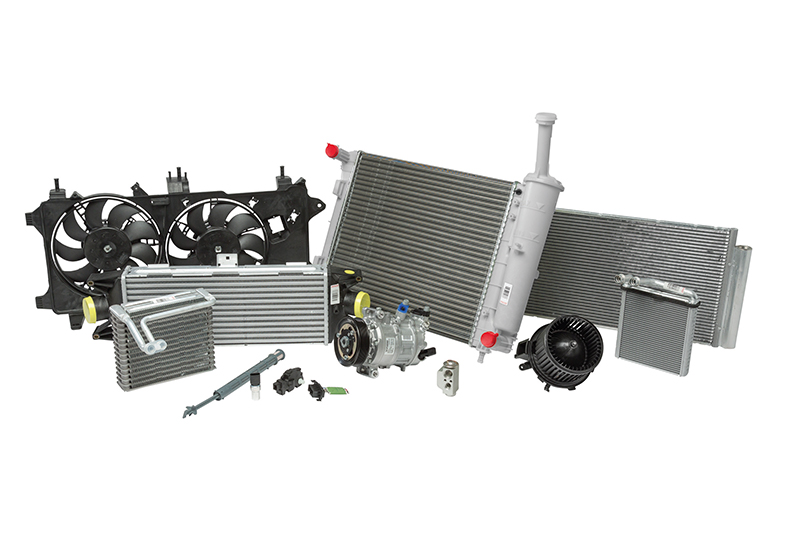
Although there are many elements within an air conditioning system, its entire efficiency relies on the compressor working properly and circulating the correctly proportioned mixture of oil and refrigerant around its sealed circuit and through the rest of its associated components. Denso explains.
To keep the air conditioning system working efficiently, not only does the owner need to use it regularly, but it also needs to be serviced, by a competent technician, in accordance with the vehicle manufacturers’ schedules. Over time however, even the best maintained systems can suffer from some sort of failure, which will require the replacement of one, or several, of its components.
As indicated, the A/C compressor is central and so will often be the part that is subject to the greatest pressure if there is a problem within the system. So, if it is found to require replacement, what best practice principles does VM original equipment supply partner and A/C specialist, Denso, say technicians need to follow?
Compressor replacement
Before removing the compressor from the vehicle, check if it can be rotated by hand because if it’s found to be locked, it usually indicates a lack of lubrication, which will result in metal debris in the A/C system. This means it will need to be correctly flushed before fitting the new compressor.
After removing it, perform a visual inspection of the faulty compressor, and write down the results, as these will provide a clear understanding of its condition. Check the suction and discharge ports, as this will help in the process. A dirty discharge port, for example, indicates dirt in the A/C system, and a dry suction port suggests a blockage, which is preventing the oil from circulating back to the compressor.
The compressor also needs to be drained of oil, so check its colour and the amount collected, and once these steps are done, the visual inspection is complete and the results will determine the necessary replacement procedure using the compressor installation guide, supplied with the new compressor.
If the oil is clean, the correct type of oil is inside the circuit, the right amount and type of UV-Dye is used and there are no other additives inside the A/C system, then flushing with refrigerant is not required, and the new compressor can be fitted following the steps in the guide. However, the oil in the circuit still has to be correctly proportioned, which requires the oil balancing procedure highlighted later.
On the other hand, if wrong oil or additives are found, or the system contains too much oil, but the refrigerant circuit is clean and no black or metal particles are found, or no oil drain plug is fitted, then flushing the system with refrigerant is required before fitting the new compressor. However, if black sludge, metal particles or a leak stop is found in the refrigerant circuit, flushing with refrigerant is not possible and a more fundamental overhaul of the A/C is required.
After installing a new compressor, it is essential to ‘run it in’, the purpose of which is to correctly distribute the oil to prevent damage immediately after the new component is fitted.
Balancing the oil
Without oil in the A/C system, the compressor will seize, which makes the oil essential. Just as modern engines require oils with specific formulations, A/C systems must also have the correct specification of compressor oil to make sure the compressor will operate under all circumstances.
There are three formulations of premium quality oil in Denso’s A/C lubricant range and these are specifically designed to suit the requirements of its various compressors, all of which are pre-filled with the correct specification of oil before their shipment, and is the only oil that will not invalidate their warranty.
Looking at the three oils individually is important because, despite opinions to the contrary, not all oils and refrigerants can mix, which casts doubt on the efficacy of an ‘universal’ A/C oil. At this point, it is worth reminding technicians that refrigerants must also not be mixed. Denso ND-oil 8 is a PAG 46 (this indicates its base oil type and viscosity) formulation and is designed for mechanical compressors using R134a refrigerant.
ND-oil 11 is a POE formulation, which is specifically designed for electrically driven compressors using either R134a or R1234yf refrigerant. ND-oil 12 is another PAG 46 formulation, but with specific additives and is for mechanical compressors using either R134a or R1234yf refrigerant.
In addition to the correct formulation of oil, when installing a replacement compressor, it is vital to have the right amount of oil in the A/C system.
If, when the old compressor was removed, the system has been flushed, the new compressor can be installed directly, but don’t forget to check if the pre-fill quantity matches with the VM’s data.
If, however, flushing is not required, technicians should use the following calculation to determine the correct amount of oil to drain from the new compressor:
A = Total oil amount in the new compressor
B = Amount of oil drained from the old compressor
C = Amount of oil to remove from the new compressor
As an example, if the total amount of oil in the new compressor is 120cc (A), and the total amount drained from the old compressor is 50cc (B), then the amount of oil to remove from the new compressor is AB (120-50), in this case 70cc (C).
However, for some applications it is necessary to add oil; for example, where there is one and the same part number for single and dual evaporator, or when the oil quantity of the new compressor differs from the VMs specification. If this is the case, technicians should check the VM data to confirm the correct oil amount. However, oil should never be added to the compressor; instead, it should always go into the condenser, receiver drier or evaporator.