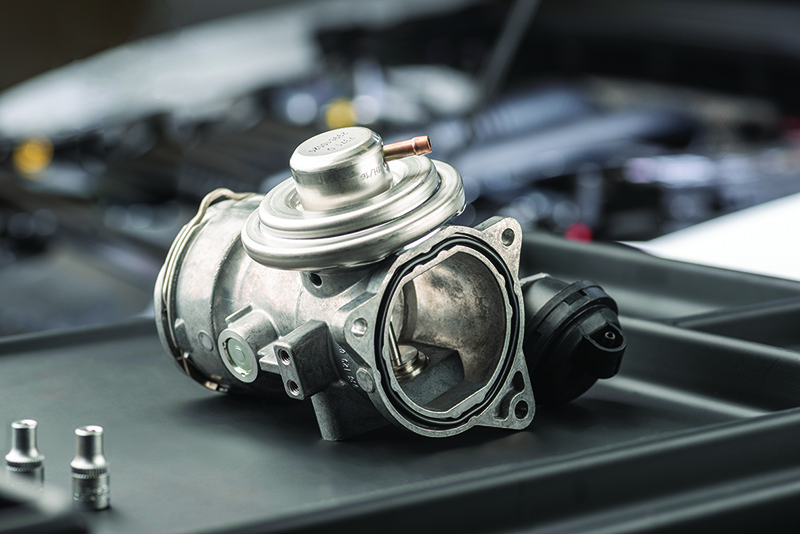
NGK has introduced a range of EGR valves to its NTK Vehicle Electronics portfolio. Here, the company explains the function of the valves and why they are so important when it comes to reducing harmful emissions.
NGK argues its latest addition to its NTK portfolio, a range of EGR valves are equivalent to their original equipment counterparts. Phase one of the launch in March saw the introduction of 45 references to sit alongside the company’s range of NTK Lambda sensors. The principal function of the EGR system is to reduce the amount of harmful nitrogen oxides (NOx) that are produced during the combustion process.
NOx is created when high combustion temperatures enable the nitrogen and oxygen present in the air-fuel mixture to combine. NOx formulates when the combustion peak temperature is high, so the target is to reduce this temperature.
The higher the oxygen content is of the charge entering the combustion chamber, the higher the burn temperature. Recirculating some of the exhaust gasses into the inlet side of the engine has the effect of reducing the amount of O2, which lowers combustion temperatures and reduces NOx emissions.
There can be a compromise between the reduction of NOx emissions and engine efficiency. Too much exhaust gas in the intake charge when the engine is cold would make combustion very unstable and the engine would not run smoothly. At high engine loads too much exhaust gas in the intake charge would cause a reduction in power output. Diesel engines can suffer with excessive black smoke. So, the valve needs to be controlled accurately to maintain decent drivability throughout all operating conditions.
The valve’s function is to control the amount of exhaust gas which flows into the inlet side of the engine.
How do they work?
Early units were purely pneumatic (vacuum operated). Since then, electronically operated units were introduced, some both vacuum and electronic. Modern units have grown in complexity and are an integral part of the engine management system, and the Engine Control Unit (ECU) monitors all areas, e.g. speed, load, boost pressure, mass air flow rate and temperatures to control the valve to allow the correct amount of exhaust gas through for all operating conditions.
Many EGR valves utilise a system to reduce the temperature of the exhaust gas. This is because it is undesirable to pass hotter than required exhaust gas into the system, to maintain combustion efficiency and prevent component damage. Some do this with either a separate or integral (water cooled) heat exchanger to reduce the exhaust gas temperature.
Where to find them
Originally developed at the beginning of the 1970s, EGR valves first started to be used in Europe in the 1990s in order to meet the ‘Euro 1’ emission standards. Today, 100 per cent of diesel cars are equipped with EGR valves and 30% to 50% of petrol cars. Many new models will even be equipped with two EGR types (low pressure and high pressure), which means that the replacement part market for these types of valves is likely to grow, corresponding to the level of demand.