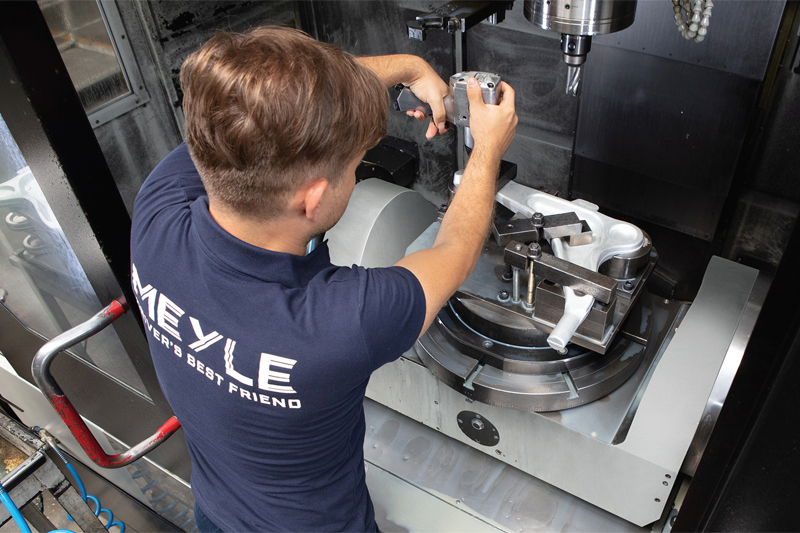
An increasing number of recalls, poorly conceived technology in the vehicle, and complicated installation and removal, often leads to frustration for garages. To improve product quality and make life easier for mechanics, Hamburg-based manufacturer MEYLE has a meticulous engineering process for its MEYLE-HD range, as PMM finds out.
There is a great deal of demand for spare parts optimisation, and there are a variety of reasons for this: greater volumes of traffic, higher vehicle mileages, more efficient engines, and increasing vehicle weights coupled with deteriorating road conditions. There is also an increasing cost pressure for the vehicle manufacturers – development and testing times are so short that many components no longer deliver the usual durability. The trend in the direction of lightweight construction and material savings, and also short model life cycles and increasing model diversity are likewise significantly shortening the service lives of various serial parts.
Multi-stage re-engineering
To ensure that MEYLE-HD parts fulfil the expectations of customers, garage businesses and drivers, MEYLE has established a multistage re-engineering process. The company’s engineers analyse OE parts, their weaknesses and potential for improvement, to then use their findings to develop better parts. These engineers are involved in the entire process, from development to manufacture, at the production facilities or at those of its international production partners.
The product experts know the market requirements and the daily routines in the workshop very well, and therefore focus product development on solutions that are tailored to the needs of the garage technician, including a four-year warranty on its MEYLE-HD parts (for more information on this warranty, click here).
Manufacturing expansion
In recent years, MEYLE has significantly expanded its research and development, and has further enhanced its manufacturing output with its own production facilities in Turkey.
The company has plants that manufacture steering and suspension, and rubber-to-metal parts. In the areas in which MEYLE is unable to manufacture, the company works with an international network of development and production partners, including OE suppliers, all of which manufacture parts in accordance with MEYLE’s specifications and standards.
All of the company’s production partners are regularly audited by quality engineers to ensure that standards are maintained and can be relied on.
Kit creation
One example of how to improve on OE solutions that has been developed by the company’s engineers is the MEYLE-HD slot bushing kit with matching installation tool.
The experts controlled the entire process – from the initial idea, through development, to production and comprehensive quality tests.
The idea for the product came from the analysis of the repair on the BMW control arm. In contrast to the OE version, defective bushings on the BMW rear control arm can be replaced separately in pairs with the MEYLE kit – a repair solution that is not yet available from the OE side with the appropriate tool, and previously had to be solved by the cost-intensive replacement of the complete control arm.
MEYLE developed a specialised tool to ensure easy installation and removal of the bushing. The bushings are already pre-compressed to installation size and enclosed in an installation sleeve. Because the installation sleeve is longer than the bushing, the tool is guided during insertion, preventing the tool from slipping off.
The environment benefits, too. Produced with high energy, the aluminium body of the control arm can be used again, with any waste associated with the use of the repair solution limited to a few rubber and aluminium parts. What’s more the solution is lighter: at 600g, the two MEYLE bushings are lighter than the OE control arm, which weighs nearly 4kg.
Aftersales support and technical advice
MEYLE makes a concerted effort to ensure that the garage businesses using its components can rely on solid aftersales support. The technical services team is available for questions and the technical trainer team advises on usage and tips for numerous products. To make access to training and tips easier, the company is offering a series of online technical training courses, as well as the tips and tricks you can find on the MEYLE YouTube channel.