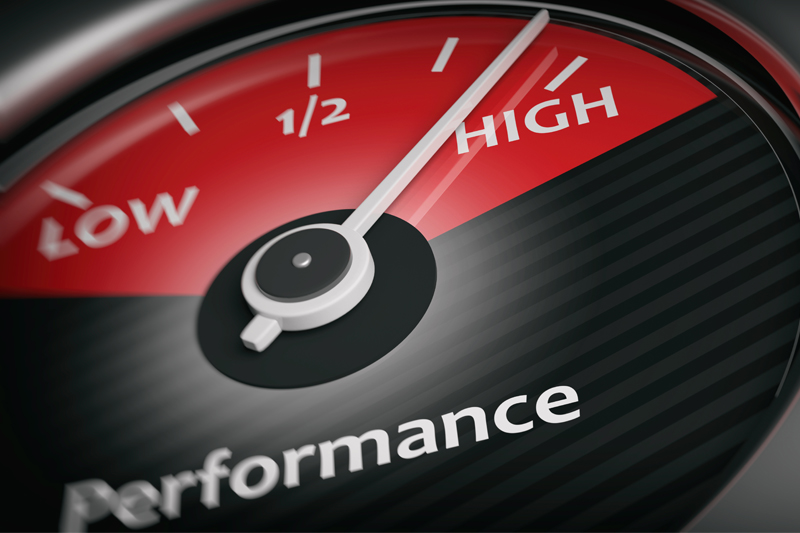
Restrictions imposed through legislation on brake manufacturers have created the need for the make-up of discs and pads to be significantly altered. In order to stay ahead of the market shift, Delphi Automotive has made a number of changes to its parts offering. PMM finds out more.
Recently introduced legislation is continuing to influence the braking aftermarket. Legislation is already in place to reduce copper in brake pads, with the aim to completely remove the substance by 2025. Copper is generally used as a performance enhancer in braking, so it can’t be easily replaced.
As a result of these changes, manufacturers have to re-engineer entirely different friction materials. Delphi has launched an OE-quality, copper-free brake pad range eight years ahead of time, reducing copper materials in braking components to less than 0.5%. The new formula provides a more stable friction coefficient over varying conditions. Delphi’s copper-free pads also reduce brake pad wear by more than 30% in some cases, increasing safety while continuing to offer excellent feel and refinement.
For brake discs, the extension of ECE R90 legislation to discs and drums for new vehicles less than 3.5 tonnes will have significant implications for the aftermarket. As with pads, each disc manufactured and sold across Europe will have to pass a series of rigorous tests to perform within a prescribed tolerance of the OE part it is intended to replace. This will make it increasingly more difficult for lower quality alternatives to reach the market and compromise safety. Delphi’s brake discs have been fully compliant with R90 quality standards for many years, and its discs for new vehicles launched after 1st November 2016 will also be R90 homologated and certified, alongside a range of popular discs fitted to older vehicle applications. The company expects over two thirds of its range will be certified by the second half of 2017.
Besides legislation, the market is seeing a shift towards higher performance braking products. Delphi has recently launched an extended range of OE-quality, fully coated brake discs. A special zinc-flake, anti- corrosive coating offers protection against corrosion. The range also offers a more cosmetically appealing finish, which is vital as the use of alloy wheels continues to increasingly expose brake discs. The new coated discs have no oil to clean off, meaning they are much quicker and easier to fit, saving garages valuable labour and service time.
High-carbon and cross-drilled discs are also available to the aftermarket. High carbon discs contain twice the amount of carbon, for improved thermal behaviour and greater stability. This helps to reduce the risk of thermal cracking under high-temperature loads, and allows the discs to operate at a cooler temperature, for a more consistent braking performance. The added carbon also increases a brake’s resistance to distortion or warping for added durability.
The holes in the cross-drilled discs dissipate heat, and eliminate any brake dust or gas generated when the pads come into contact with them. This helps to keep the pad surface both cool and clean and reduce thermal distortion and warping. These same holes also prevent a film of water forming during wet conditions for improved braking response.
Delphi offers a range of high-carbon and cross-drilled brakes, allowing garages to offer their customers a longer-lasting, high- performing braking product.
Common challenges for technicians
One of the biggest challenges facing today’s technicians is the increase in electrical content. Once purely mechanical, modern braking systems are now also controlled by electronics, be it the vehicle’s anti-lock braking system, traction control or electronic handbrake. Electronics are also revolutionising the way these systems are serviced and repaired. A good working knowledge of the system is no longer enough; technicians need both an in- depth knowledge of the entire system and a powerful diagnostic tool. Without these, a service could take much longer, be unsafe or even impossible to perform.
Many modern vehicles now have electronic parking handbrakes. A specialised diagnostic tool is required to place the rear brake calipers into ‘service mode’ to be able to remove the rear brake pads. On completion of the job, the handbrake module then recalibrates the pressure required to apply the handbrake.
Working on ABS ECUs can sometimes affect other systems. For instance, take the 2013 Volkswagen Golf Mk6 – when the ABS ECU is replaced, recoded or completely reflashed, a diagnostic tool is required to realign the CAN installation information within the DSG ECU. Until this is done, the dashboard will display errors relating to the automatic gearbox, along with fault codes.
Delphi offers a solution to help diagnose any braking fault through its DS diagnostics tool. The device also allows a technician to control systems during maintenance, protecting both the brake system components and the workshop technician. The company also offers full training, in-field support and access to a technical hotline, supporting technicians on all braking-related issues.