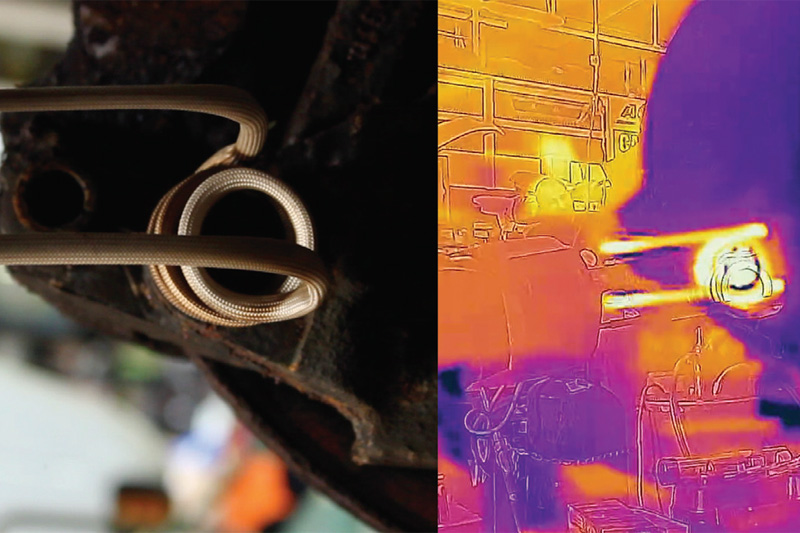
Induction Innovations makes the case for induction heat being a more precise, safe and reliable method than torch heating.
The tool of choice for removing a rusted or seized part from corrosion or thread lock compounds is an important one for any technician. Unfortunately, torches can be unreliable and unsafe to use, and more and more workshops are not allowing open flames. While some technicians still choose the torch, many are switching to induction heat.
How does induction work?
Induction heat is a flameless heat transferred from the unit to the application being heated via electromagnetic waves. The result is that the object being heated never comes into direct contact with any open flames and the coil itself does not get hot.
The coil is the transfer primary and the parts being heated become a short circuit secondary. When a metal part is placed in the induction coils and enters the magnetic field, circulating eddy currents are induced within the part. These eddy currents flow against the electrical resistivity of the metal, generating precise and localised heat without direct contact between part and coil.
Induction Innovations’ tools are designed to solve problems such as removing stuck or corroded parts and adhesives in a faster, safer and more precise way. President Tom Gough developed the first Inductor Series model in 2000. He was inspired to invent the tool after dealing with 28 years in collision repair and seeing the many time-consuming processes found in the vehicle and equipment repair industry.
Benefits
The most important reason to make the switch to induction heat over an oxyacetylene torch is that it is safer and more reliable. Torches can produce inconsistent results and uneven heating. Flames cover a larger surface area which, as a result, can cause more damage and catch plastics, wiring, fuel, or trim on fire.
Induction heat enhances workplace safety because of the precise, localised heat and no open flame. There is less potential to catch something on fire, damage the surrounding work areas or cause workplace injuries. When used properly by following the instruction manual, the results of induction heat are the same each time.
Induction heating tools allow users to salvage parts that otherwise might be discarded. When using a torch, consumables such as gas expenses can add up. You can reduce or eliminate those expenses by switching to induction heat. After purchasing the tool, additional costs may come from purchasing new coils. However, Induction Innovations’ coils are designed to last around 200 uses if taking the proper precautions.
Note: when they start to look worn or the insulation starts to tear, that is when you should replace them.
Save Time
The Mini-Ductor product line series is many professionals’ first choice of handheld flameless torch and the original handheld induction heater.
The tool aims to save time by reaching tight-fitting areas where a flame cannot go. Whether you want an inline, cylinder design with the Mini-Ductor II or an angled, pistol grip with the Mini-Ductor Venom, each tool will help you fit those hard-to-reach areas. Flexible coils also allow users to fit tight areas by bending and shaping them to each application.
With induction heat, there is no need to cover or remove flammable parts nearby either. The Mini-Ductor tools allow you to work quickly and efficiently. For instance, a Mini-Ductor tool can turn . in. nuts red hot in just a matter of seconds.