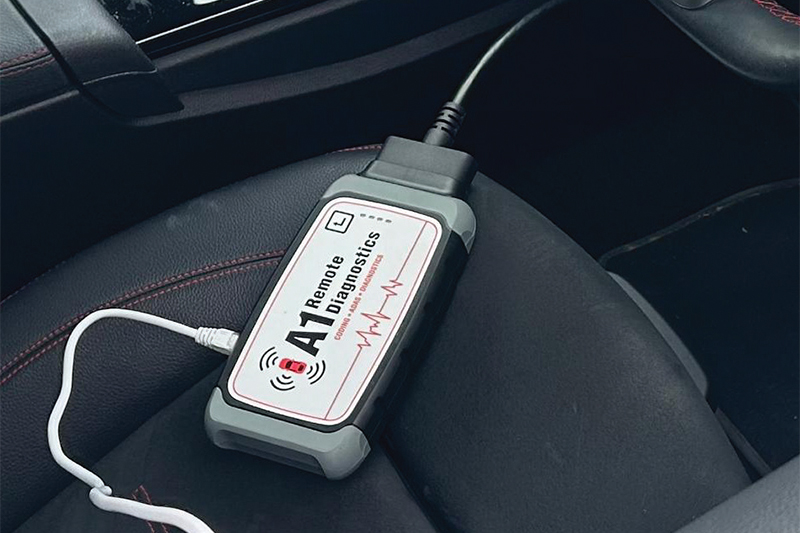
Despite their impending demise, diesel vehicles will become more complex in the next five years. Now, replacing a failed component is no longer the end of the job, says Iain Molloy, managing director at A1 ADAS Group. In many cases, it’s just the beginning.
Whether it’s a new NOx sensor, AdBlue injector, or even an AdBlue tank, today’s emissions-related parts often require specific coding, resets, or software updates to fully integrate with the vehicle. One of the key trends we’re noticing at A1 ADAS Group is just how often modern diesel systems rely on dealerlevel tools to finalise a repair.
These systems are highly integrated, with a constant feedback loop between sensors, modules, and ECUs. If that loop is broken, even temporarily, the vehicle may not recognise that the fault has been fixed. The result? Warning lights remain, vehicles go into limp mode, or worse, fail to restart.
AdBlue systems
AdBlue systems are a prime example. We’re seeing a surge in vehicles, particularly from manufacturers like Mercedes-Benz, that go into ‘countdown’ mode when a fault is detected. Even after parts are replaced, the problem can persist unless a procedure is performed via OEM diagnostics.
This can put independent garages in a difficult position. Whilst they can mechanically complete the job, without access to manufacturer-level software, they find themselves unable to code or program the new component. Many believe, wrongly, that their only option is to send the vehicle to the main dealer.
It’s not a problem that’s going away any time soon. Even though the production of diesel vehicles is set to cease in 2030, they’ll continue to make up a substantial portion of the UK car parc for the next few decades. Garages need to be thinking ahead about how they’ll support these vehicles, especially as emissions systems become increasingly locked down behind secure gateways.
One solution is to use a remote diagnostic service. At A1 Remote Diagnostics, its dealer-trained technicians have been supporting workshops for the last five years.
The service has been a game-changer for garages, especially those now feeling the financial constraint of keeping up with the investment required to access every OEM’s software and updates. For them, dialling in a remote technician is not just cost-effective, it adds another revenue stream and is very profitable. Additionally, the increased efficiency in vehicle throughput directly impacts the bottom line.
It works like this: using the A1 Remote interface, the garage technician securely dials in the vehicle – from anywhere in the UK – to a technician at A1’s HQ. The ‘call’ is generally answered immediately and certainly within two minutes. A1 then carries out the necessary coding, programming or software updates, and helps to finalise the job.
Essentially, it means garages can have virtually every OEM at their beck and call.
We’re regularly involved in scenarios where a job that would take 10-15 days via a main dealer, is completed in under an hour. The job is cleared, the customer gets their vehicle back sooner, and the invoice is cleared quickly.
Thankfully, the reality for independent garages is this: with the right remote diagnostic partner, there’s hardly any reason to send a vehicle out to the main dealer.
Using software
The bigger picture is that diagnostic software is now an essential and routine part of most repair procedures. It’s no longer a question of if software intervention is needed, but when and how.
For independent workshops, that means diagnostics and emissions-related component coding will stay relevant well into the future. The important thing is to be prepared and know that if you don’t have the right tools in-house, expert remote support is ready and waiting to help complete the job quickly and correctly.