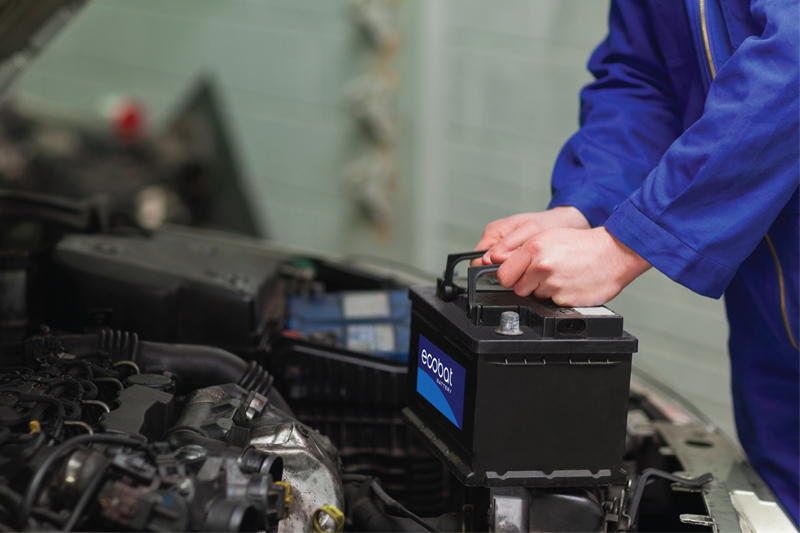
Lead acid, GEL, SLI, AGM or EFB, whatever the battery, they all have one thing in common – they need to be tested, according to Ecobat.
First, a bit of background. Under the surface, or perhaps more appropriately, inside the case, the basic chemistry of a 12-volt battery remains the same today as when it first became a standard feature on the typical motor vehicle more than a century ago. Another interesting fact is that despite the common misconception, a battery does not ‘contain’ electricity, rather it is a chemical reaction between the four materials held within the battery – hydrogen, oxygen, lead and sulphur – that produces an electrical current when a load, such as a light bulb, is applied to it.
Each battery contains six, nominally two-volt cells, which when they are fully charged hold 2.11 volts and 1.95 when completely discharged, so the operational window is actually very narrow, between 12.7 volts for a fully charged battery and 12.4, at which point it needs to be charged as soon as possible because prolonged periods at this level of discharge will causes damage due to sulphation.
In simple terms, each cell consists of positive and negative plates made from lead alloy and pure lead respectively, separated by non-conductive dividers, immersed in electrolyte, which is a mixture of sulphuric acid and distilled water. Although electrolyte was traditionally liquid – hence the ‘wet lead acid’ terminology – nowadays it can be as a gel or bound in glass mat, as in an absorbent glass mat or AGM battery, for example.
As a general principle, the larger the surface area of the plates, the greater the cold start power (CCA) the battery can provide. So, a conventional SLI (starter, lights and ignition) battery will benefit from containing more plates in a cell, whereas fewer thicker plates increase the battery’s cyclic (charge, discharge, charge) capacity, which is a key requirement for a battery fitted to a vehicle with a start/stop function that is not continuously being charged when the engine is running.
Under a load, which is what starts the chemical reaction that produces an electrical current, the electrolyte breaks down into positively charged hydrogen ions and negatively charged sulphur ions. At the same time, electrons travel from the positive to the negative battery terminals, providing the power for the vehicle’s electrical systems.
To compensate for this flow of electrons, the sulphate ions in the electrolyte react with the lead plates to produce lead sulphate, which uses up the sulphuric acid in the electrolyte, making it less concentrate. When this concentration falls below a certain level, the efficiency of the chemical reaction that produces the electrical current reduces, so the battery needs to be recharged.
During charging, these chemical processes are reversed, although there are always associated losses, so a battery will only ever be able to withstand a certain number of charging cycles, meaning its usable life will inevitably come to an end.
However, this natural process is accelerated if the vehicle is only run for a limited period or undertakes very short journeys, the weather is particularly hot, the alternator output is incorrect or if it remains unused for a long period without a recharge, such as during the first Covid 19 national lock down in spring 2020.
The importance of testing
As now more than ever, the performance of the battery is a key factor for the correct function of many of a vehicle’s systems, assessing its condition is a best practice principle that should be adopted by every technician when a vehicle enters the workshop. Therefore, both the state of charge (SOC) and state of health (SOH) need to be assessed.
While the SOC can be simply determined with a voltage measurement, to make a reliable statement about the SOH requires a complex test procedure, which among other things, considers the CCA, the residual capacity (Ah) and the charge acceptance (CA).
Just as vehicle technology has continued to develop over the years, batteries such as AGM and EFB (enhanced flooded battery) have also developed. Therefore, to obtain reliable test results, especially in regard to the SOH, it is essential to use modern test devices that are adapted for these new battery technologies.
As well as detailing the finer points, a good quality tool, such as the EBT 780, supplied by Ecobat Battery, will provide the user with a headline result to allow them to decide the correct way to proceed.
Additional advice
When fitting a replacement battery in a start/stop equipped vehicle, another important factor is the need for technicians to use a battery validation tool, such as Ecobat Battery’s EBT 420, to ensure the new AGM/EFB battery is correctly assimilated into the vehicle’s battery management system (BMS). This vital element is an important step that is often overlooked and means that even if the battery is of the appropriate technology and correct specification, incorrect validation will result in the wrong charge algorithms being applied to the new battery via the BMS, which will considerably reduce its service life. In addition, the vehicle’s ECU will also need to be reset, otherwise the replacement battery could be under charged, leading to its premature failure.
There is also a significant additional benefit to fitting start/stop replacements, which helps both the workshop and their supplying wholesaler, and that is the fact that with each installation they are selling a more expensive battery, with a greater profit margin. On top of this, because they are fitting a battery of the correct specification for the application, rather than a familiar, but ultimately inappropriate SLI version, customer satisfaction increases and warranty claims are reduced accordingly.
As the UK’s largest independent automotive battery distributor, supplying prominent brands such as Exide, Varta, Lucas and Numax, Ecobat Battery has the unrivalled ability to supply the batteries that are needed, when their customers require them.