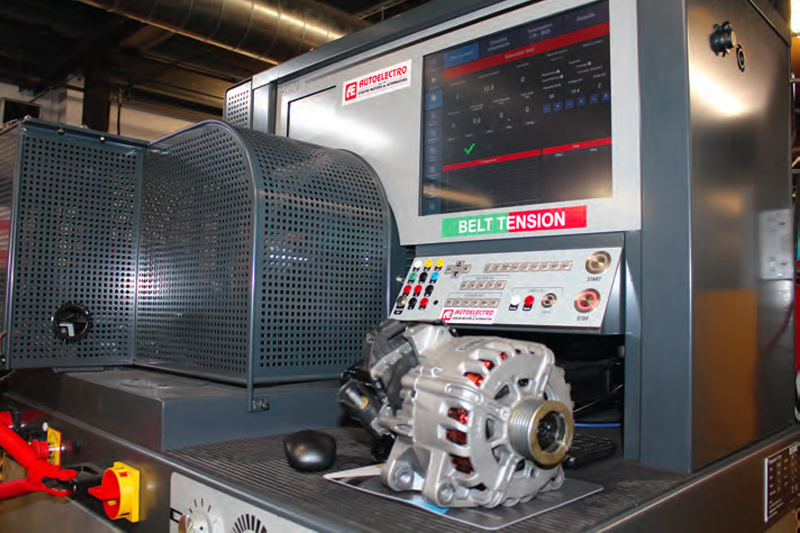
Autoelectro is advising technicians to check vehicle software and ECU communication to avoid alternator misdiagnosis.
With nearly four decades of experience as a remanufacturer and specialist in starter motors and alternators, Autoelectro is trusted to identify and communicate new trends, technologies, and challenges to its customers. Ironically, it is the communication between modern alternators and a vehicle’s ECU and software that has come to the forefront.
Each and every one of Autoelectro’s starter motors and alternators, of which there are more than 5,000 part numbers in stock, is built and tested to meet or exceed OE specifications. During this rigorous process, the team has identified that newer alternators, which communicate with the vehicle’s ECU to determine charge rate and warning light controls, can encounter communication issues if the vehicle’s software is outdated. This may lead to misdiagnosed charging faults, where the alternator is wrongly blamed when the real issue is simply a communication problem.
Autoelectro’s Harnek Bhogal said: “We have identified several ECU-controlled – and even 48V – part numbers for new Ford, Range Rover and Audi models, of which the technical support is exclusive to us in the aftermarket. Our first piece of technical advice for these parts is to ensure that the vehicle software is up to date before conducting any diagnostic or repair work. This step is crucial to avoid misdiagnosis and unnecessary replacement of functioning alternators.”
Identifying trends
Autoelectro is the largest remanufacturer of starter motors and alternators in the UK and it has complete control over its manufacturing processes, which allows it to identify and share emerging trends in the industry. The company’s ISO 9001 certification is another important part of Autoelectro’s credentials. Its commitment to exceptional product quality and adherence to international standards for quality management systems is another confidence booster for customers.
Harnek added: “Our ISO 9001 certification reaffirms our dedication to continuous process improvement. This strengthens customer confidence and guarantees that we deliver reliable and premium starter motors and alternators for the aftermarket. Additionally, we use many OE components in our units, and every starter motor and alternator we sell is fully benchtested on the latest OE-specification test equipment, under load to simulate real-world scenarios.”
To support Autoelectro’s customers, technicians receive part-specific technical notes in the box. They can also find these via Autoelectro’s 1986 dashboard, which, once an account holder, will also provide access to an extensive library of online resources, including common faults, troubleshooting tips, and industry updates. This comprehensive support system ensures that technicians have all the tools they need to effectively diagnose and resolve issues.
Harnek concluded: “It’s crucial for technicians to review these notes before installing replacement parts to prevent issues. Our experience shows that these notes provide peace of mind for both technicians and motor factors. It builds trust.”