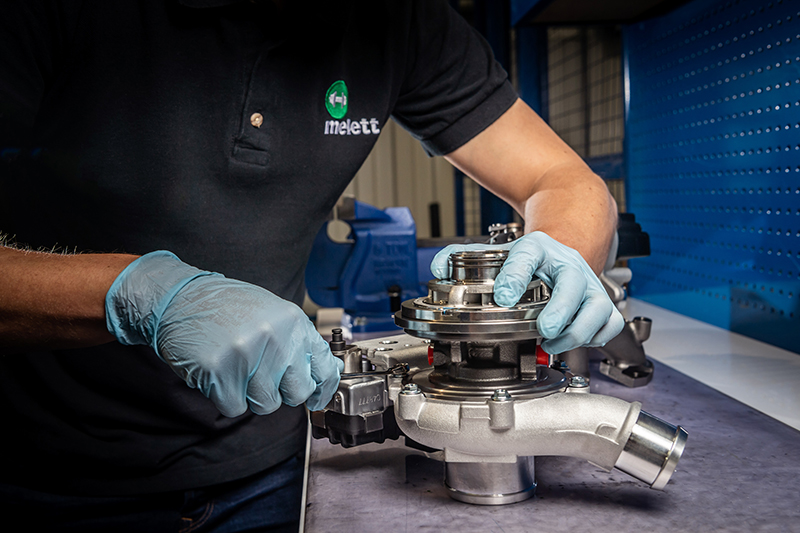
Tom Wright, Product Manager at Melett, outlines the core purpose of oil in relation to the turbocharger.
There are many ways in which oil-related issues can damage the components, and in that respect, oil is the lifeblood of a turbocharger.
Lubrication is a key element to ensuring a turbocharger is doing its job correctly. It is essential, therefore, to check that a vehicle’s oil is the correct grade. When fitting a replacement turbo, it is important that the oil system has been primed and is in full working order. If this is not the case, it can lead to premature failure.
Oil contamination
Causes
Dirty oil, often referred to as ‘oil contamination’, is one of the top killers of a turbocharger and can happen in a multitude of ways. When repairing the vehicle, if the oil system is not emptied, purged and changed correctly, it can leave debris from the previous failure, which can contaminate the new oil and cause premature failure.
If a damaged, or poor-quality oil filter is used, this is another way debris can pass through the filters and into the oil system. In addition, liquid contaminants can lead to premature oil degradation, and increased corrosion and wear, while oil degrading can also be caused by excessive temperatures or extended service intervals.
Prevention
If a turbo has failed, it’s important to ensure that all the oil systems are purged and free from any foreign objects.
A simple way of preventing dirty oil from affecting the turbocharger is by taking extra care when changing the oil during servicing to prevent accidental contamination, adds Tom.
It is also key to check for engine wear that could leave swarf deposits.
Something that must be done is to replace or clean the oil inlet pipes and in-line micro filters, as this helps to prevent carbon deposits entering the oil flow to the bearings.
Tom concludes: It is important to get a vehicle serviced every year or every 10,000 miles, as well as changing the oil in accordance with the vehicle manual, as it gives a turbo the best chance of having a longer life cycle.
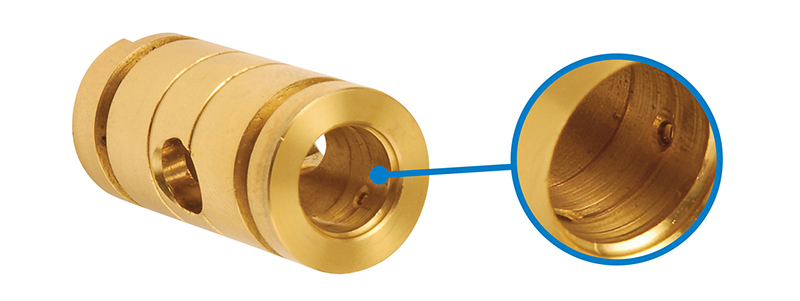
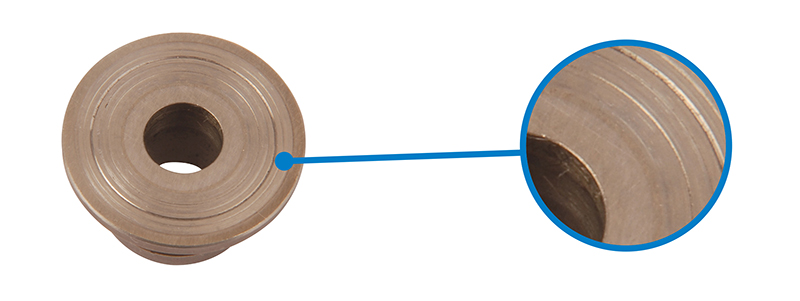
Insufficient lubrication
Causes
Insufficient lubrication is also known as oil starvation or lack of lubrication.
It is often caused by blockages in the oil feed pipe and micro filters within, damaged or bent oil feed pipes, a lack of priming of the new turbo, as well as a damaged or worn oil pump, or sludge and coke build up in the bearing housing from hot shutdowns, says Tom.
Prevention
Using the correct grade of engine oil specified by the OEM engine manufacturer is essential to give the turbocharger a long-lasting life cycle. If the incorrect grade is used this can lead to overheating or insufficient lubrication.
Equally, oil supply is critical to the turbo, so it is important that a technician ensures the oil flow is correct. Priming the turbocharger and oil systems can stop the turbo from instant failure. Oil inlet pipes should also be cleaned or replaced to remove carbon deposits or sludge that could restrict oil flow to the bearing systems.
Perhaps more crucially, Tom goes on to share a little-known fact that many vehicle owners are unaware of: It is important that drivers are aware that they need to allow time for the engine to warm up at the start of each journey and cool down at the end.
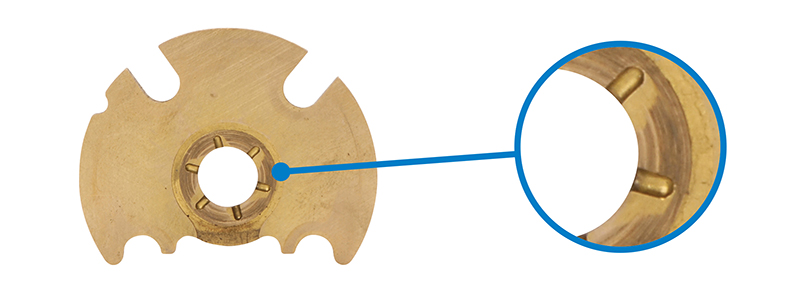
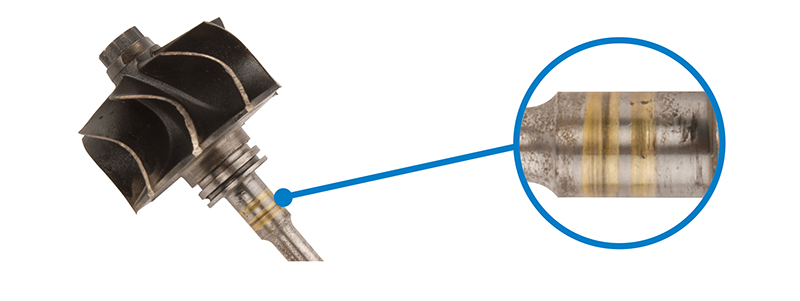
Oil leaks
Causes
Oil leaks are somewhat of a myth when it comes to the turbo being at fault, comments Tom. The biggest cause of oil leaks comes from the environment that the turbo is situated in. There are very few cases where an oil leak happens because of a component or manufacturing issue.
Oil leaks can occur when an engine is running on idle. This is because the pressure within the housings is lower, which in turn can lead to a vacuum being created, causing the oil to leak into the turbine housing. Once the engine starts to run at normal speeds the pressures will be restored, and the leak will stop.
Tom adds: Other things to consider are ‘engine blow by’ and ‘crank case blow by,’ both of which cause the same effect, as they increase the pressure in the crank case. This affects the oil flowing to the turbo at the correct rate, which acts as a restriction to the oil return pipe, causing the turbo to leak oil at either the turbine or compressor end.
Oil leaks can occur on VSR (high speed) balancing machines, as the ambient pressures required to create the seal are not present as no housings are used. This can then force out oil from both the compressor and turbine ends, giving the impression of a leak. This is unlikely to occur when the replacement turbo is fitted to the engine.
Prevention
When it comes to oil leaks, it is imperative that the vehicle technician ensures air, exhaust, and oil drain systems are clear from blockages or restrictions, before moving on to check there are no leaks present in the exhaust system.
The use of silicone on oil gaskets is not advised as both can easily become detached and block oil passages. Similarly, technicians should ensure the diesel particulate filter (DPF) and catalytic converter are free of blockages.
The correct gaskets and o-rings should always be used, and only the correct standard of turbine housings and compressor housings should be fitted.
Lastly, technicians should always check for correct oil levels and pressure.