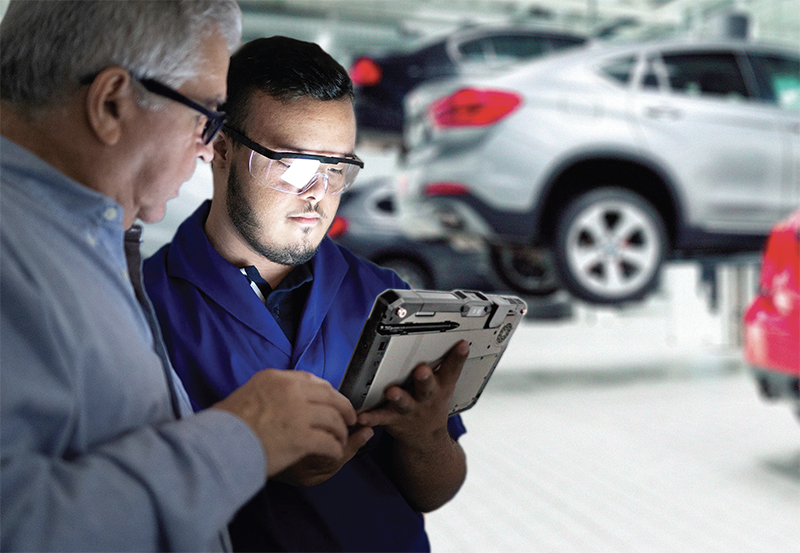
Sophie Silk, Business Development Manager at Getac, explores six ways rugged digital solutions are changing the way workshops work.
When it comes to modern workshop operations, the days of the humble penand- paper are numbered. Sure, it’s quick and easy to collect data this way, but as the automotive industry becomes increasingly digitised, the drawbacks of sticking with manual processes are becoming impossible to ignore. Today’s customers want better service, faster resolutions to issues, and to be kept informed every step of the way. This can only be achieved through digital information gathering and data sharing.
That being said, busy workshops can be physical and sometimes chaotic environments, with equipment frequently knocked off surfaces, dropped, and subjected to all kinds of dust, fumes, and spillages. Many consumer-grade laptops and tablets simply aren’t built for this kind of use case and even a small drop or spillage can result in a hefty repair bill, or even total device failure, leading to costly unexpected downtime.
Fortunately, not all devices are created equal. Rugged solutions are purpose build to thrive in environments like workshops and garages, with special certifications like MILSTD- 810H, MIL-STD-461G and IP66, to protect them from knocks, drops, spillages, vibrations and more. What’s more, they pack a serious technological punch, with powerful processors, extensive connectivity options and versatile touchscreen technology that enables businesses of all sizes to embrace the latest and greatest innovations in the industry. Below are six ways rugged solutions will help save time and money, reduce unexpected downtime, and provide an all-important edge over the competition:
1. Optimise your workforce
Picture the scenario – a technician heads out to help a stranded customer at the roadside, but the repair is trickier than first anticipated and they need extra support to get it done. If they are equipped with a rugged mobile computing solution, expert assistance is just a click away. The technician at the roadside can share real-time video with an expert back in the workshop and if necessary, get stepby- step instructions on how to solve the issue, avoiding unnecessary physical travel.
2. See the whole picture
By equipping teams with connected rugged solutions, businesses immediately get better visibility and transparency across all their operations, which can be invaluable if operating across multiple sites. Data is registered on digital databases, not on paper notebooks and team members can be easily reached without needing to look for them. Real-time updates can be sent to everyone at once and important customer/operational data is always on hand, meaning no more trips back and forth to the office all the time.
3. Comply with ever-changing processes and standards
With a rugged solution to hand, technicians and mechanics can quickly access everchanging rules, processes, and guidelines whenever they need to, straight through the device. Gone are the days of hefty workshop manuals that quickly get chewed up or lost, leaving team members to rely on memory or outdated documents. This approach helps to improve the speed and quality of workshop processes while simultaneously maximising health and safety and ensuring compliance with applicable regulations.
4. Save money
As mentioned, non-rugged devices simply aren’t built for busy workshop environments and unexpected accidents or failure can require significant time and money to rectify. Rugged solutions can significantly minimise this issue, resulting in much lower total cost of ownership (TCO) over their lifespan versus a non-rugged alternative. Furthermore, the added peace of mind they provide means team members can stay focussed on the task at hand, resulting in faster repairs and more jobs completed each day.
5. Improve customer service
Modern day automotive repair work is all about keeping customers in the loop and informed at all times. By utilising rugged solutions in the workshop, technicians can easily capture videos and images of ongoing repairs, record voice memos, or request customer approval to carry out unforeseen maintenance tasks. They can then send them straight to the customer directly from the device, significantly streamlining the whole process and speeding up time to job completion.
6. Stay ahead of the curve
By adopting rugged solutions, workshops are perfectly placed to benefit from new applications and technologies as soon as they become available. Examples include the growing popularity of augmented reality and mixed reality automotive applications, as well as advancements in digital diagnostics for both standard and electric vehicles. Rugged solution allows workshops to quickly adopt these technologies, potentially gaining a major advantage over the competition.
Like many other sectors, digital transformation is steadily transforming the way the automotive industry fundamentally operates. Those who embrace it are likely to gain many benefits in key areas like customer service, job completion times and day to day business operations. However, like every aspect of automotive repair work, having the right tool for the job is key. Unlike consumer laptops and tablets, rugged solutions are built to thrive in workshop environments, letting technicians focus on getting the job done.