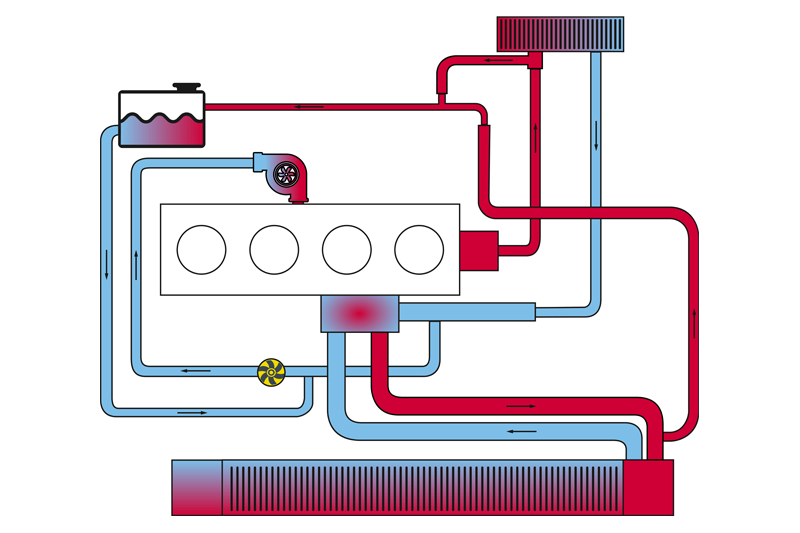
Febi explores what technological changes are occurring within the thermal management system and gives advice to workshops on maintaining these systems.
For many decades, 99.9 per cent of internal combustion engines have relied upon water (coolant) being pumped around the engine block and cylinder head to prevent overheating and thermal distortion, caused by heat of the combustion process. As the coolant is pumped through the engine casing it absorbs heat. It then circulates through a radiator to be cooled, before returning to the casing again for the cycle to be repeated. The heating/cooling process is controlled by a thermostat to maintain a constant temperature.
The water pump, like many other auxiliary components (e.g. PAS pump, alternator and A/C compressor), has traditionally been driven mechanically off of the engine crankshaft (or camshaft) via a belt. The trouble with this method is power is continually sapped from the engine which negatively affects vehicle performance and fuel economy/emissions.
Vehicle manufacturers have been developing alternative ways to drive and control these components to improve efficiency and economy, with many vehicles now fitted with electric power steering, and more beginning to use electric air conditioning compressors.
Electronically controlled and powered water pumps were introduced by BMW back in 2004. These have several advantages over the engine-driven pumps being used previously, as the electric water pump is totally controllable under all conditions. The advantages include:
Completely variable speed – the pump can run at any speed depending on what the ECU requests.
- It can provide a low flow rate when the engine is cold to allow a faster warm-up.
- It can provide a faster flow rate to cool a hot engine quickly.
The pump can run without the engine.
- This allows the engine to cool evenly, reducing ‘hot spots’ in the engine
- Especially useful for vehicles equipped with stop-start or on hybrid vehicles.
These advantages mean greater efficiency and help to reduce a vehicle’s emissions.
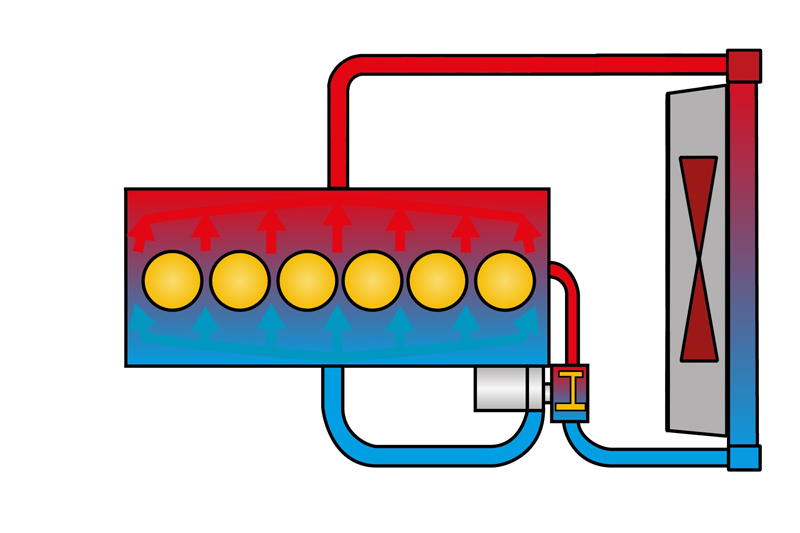
Another major advantage is that an electric pump can be positioned almost anywhere within the engine bay, allowing much greater flexibility and better use of space. The water inlet can be positioned on the side of the engine for cross-flow cooling which helps avoid ‘hot spots’ and provides more efficient cooling across all cylinders (Fig.1).
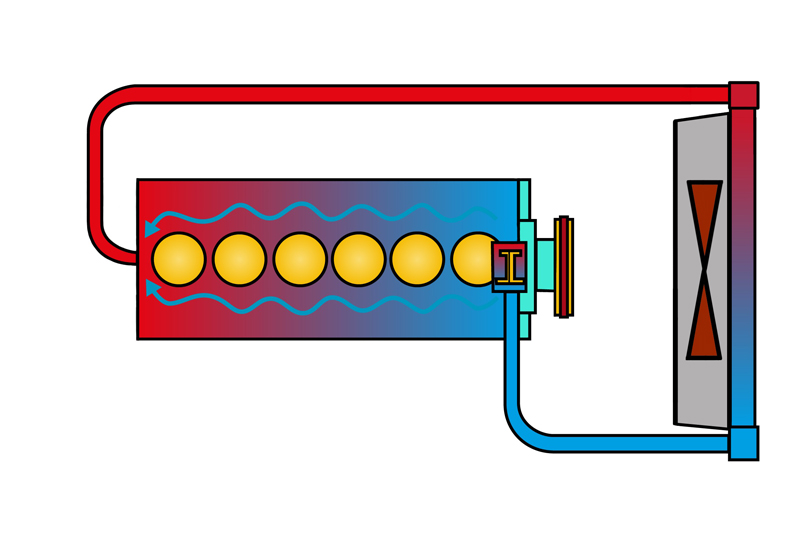
This is not possible with a belt driven water pump as it has to be positioned at one end of the engine, meaning the coolant is always circulated from one end to the other, resulting in some cylinders running hotter than others (Fig.2).
Intelligent water pump
The electric water pump is controlled by the engine management. It can determine the necessary cooling requirements by watching engine load, operating mode and the data from the temperature sensors. With this information it can determine the correct coolant pump operation and speed, and send the corresponding instruction to the pump’s control unit.
The electric pump also has self-diagnosing capabilities to aid with fault finding, with fault codes and live data available to read via the vehicle’s serial diagnostic port using a suitable tool. Data for speed, current and temperature can be found in the serial data to assist with diagnosis, as well as a function to actuate the pump to check whether it’s operating correctly.
Codes for incorrect pump speed, excessive temperature, over and under voltage, system blockage, coolant loss and air in the system are examples of the codes that can be generated.
The pump has a four wire connector: power, earth, Local Area Network (LAN) communication, and control from the engine management using pulse width modulation (PWM). The output of the wet-rotor brushless electric motor is controlled electronically by the electronic module, which is located under a cover in the water pump unit.
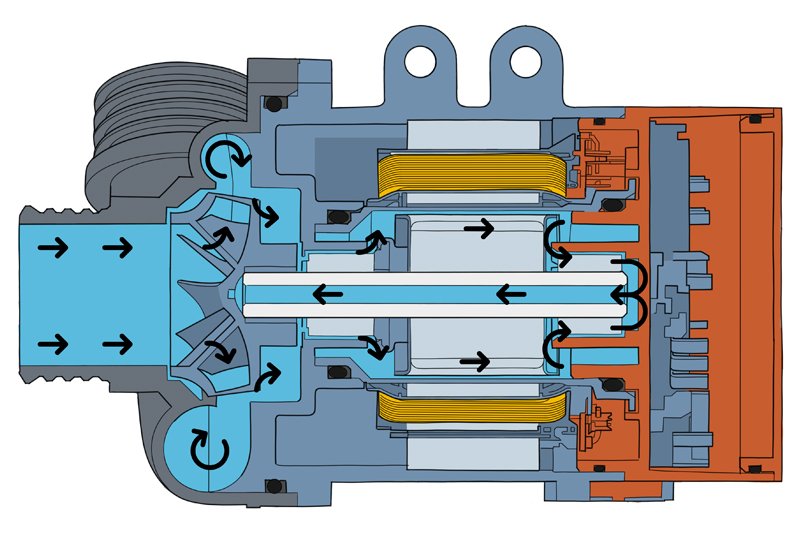
Maintenance tip
Care must be taken when carrying out maintenance (such as a coolant change) to ensure that the pump does not run dry. If the pump is removed and it is intended to be reused, it should be stored filled with coolant. If stored empty the pump could seize which would lead to overheating and potential engine damage. If the pump should ever become dry, the pump impeller should be turned by hand before connecting the coolant hoses to ensure it hasn’t seized. The system should then be immediately filled with coolant. Care should be taken during assembly to ensure that the electrical connector is clean and dry and that the connections are undamaged. When replacing or refitting the water pump the aluminium fixing bolts must be replaced and correctly tightened to the vehicle manufacturer’s specification.
When refilling the cooling system after replacing the water pump, it is essential that the cooling system is bled of air. First, vent the air via the bleed screws on the cooling system until bubble-free coolant can be seen, and then close the bleed screws. Close the coolant expansion tank cap, and then carry out the following procedure.
- Connect a battery support unit to the vehicle’s battery.
- Switch on the vehicle’s ignition.
- Set the heater to maximum temperature and turn heater fan down to its lowest speed.
- Fully depress the accelerator pedal for 10 seconds. The engine must not be started.
- The electric water pump is activated when the accelerator pedal is pressed which indicates the air bleeding procedure has started. It takes approximately 12 minutes during which time the engine should not be started.
- Once the procedure is completed the water pump will automatically stop.
- Top up the coolant in the expansion tank to 100ml above max.
- Check the cooling system for leaks. If the system needs to be re-bled (e.g. if the cooling system is leaking), allow the engine management system to completely shut down by turning the ignition off and removing the ignition key for approx. 3 minutes. Then repeat the procedure.