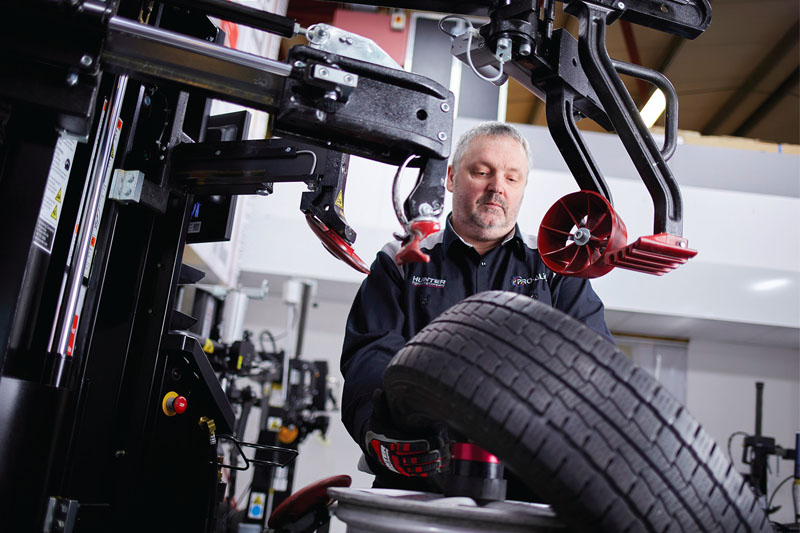
Craig Welch of workshop equipment supplier Pro-Align, outlines some key solutions to the most common problems associated with tyre changing.
The process of changing tyres is often overlooked by many. However, industry experts estimate that more than 30 million replacement car tyres are fitted in the UK each year, meaning it’s an area that deserves significant attention.
After all, even the slightest of improvements in efficiency could save workshops thousands of hours of combined labour. What’s more, if not performed correctly, a simple tyre change is likely to significantly reduce customer satisfaction and can even result in unnecessary and totally avoidable costs for workshops themselves.
Avoiding damage
One of the biggest challenges when changing tyres is ensuring that wheel rims and any TPMS sensors are not damaged in any way. This is particularly important for diamond cut alloy wheel rims where replacement costs can easily run into several hundreds, if not thousands, of pounds. The challenge, and potential cost, is made worse with many vehicles running on a combination of large diameter rims and ultra-low-profile tyres which can be difficult to remove.
Other than taking particular care when working on these type of wheel and tyre assemblies, workshops can take steps with their equipment to avoid such problems. Centre clamping tyre changers can help reduce the risk, or nowadays, there are even fully automated tyre changers, like the Hunter Revolution, which completely removes the potential of such damage.
Another major benefit for workshops using systems such as the Revolution is that many workshops have a master technician, who is often the only person authorised to work on the most expensive assemblies, for fear of costly damage claims. However, the fully automated system removes this worry, meaning that more junior or inexperienced technicians can carry out the work to exactly the same standard, helping to improve workshop flexibility and potentially reduce staff costs.
Planning ahead
When changing a high volume of tyres, certainty about how long each job will take allows customer appointments to be better scheduled, as can staffing levels, helping to optimise workshop profitability.
Another key benefit of a fully automated tyre changer, is that it takes the same amount of time, every time, to change a tyre regardless of whether it’s a common 205/55R16 or a more challenging 35 series, 23” tyre. This repeatable tyre change time means that workshops managers can plan both jobs and staff in a much more organised and efficient manner.
Health and safety
As wheel sizes on cars continue to increase, lifting just one wheel and tyre assembly onto a tyre changer can be a strenuous activity. However, when you multiply this operation by the dozens of times that may be needed over the course of a single day, this can lead to a potentially significant manual handling or health and safety hazard.
To look after your wellbeing and avoid any potential absences or additional costs in sick pay or even health and safety compensation claims, workshops should consider adding a wheel lift to their tyre changers.
Often designed as an optional extra by equipment manufacturers, wheel lifts can lighten the load when removing any potential problems associated with repeated lifting of heavy objects. Indeed, the Hunter Maverick tyre changer is being offered by Pro-Align with a complimentary tyre lift as part of its launch to UK workshops this spring.
Training
With the speed of development of modern motorcars, you should not be a stranger to the prospect of ongoing learning and development to ensure your knowledge and skills are up to date. While the humble wheel and tyre assembly doesn’t include anywhere near as many technological advances as the rest of a modern motorcar, it’s still important to keep your knowledge and skills up to date. Tyre changing technology itself does not stand still, and advances in tyre construction methods and TPMS sensor technology, mean that ongoing education is important.
Many tyre and equipment manufacturers now host a number of online learning modules and instructional videos, some tyre changers, including the Hunter Revolution, utilise their touchscreen interface for learning purposes. Here, technicians can access a number of training videos, giving them access to live, on-the-job training.
So, when your workshop is considering its next investment into a tyre changer, it’s important to consider your options carefully. A more premium solution perhaps is not only built to a better quality, but they often deliver significant added value, helping your workshop and its technicians work more safely, efficiently and to a higher standard.