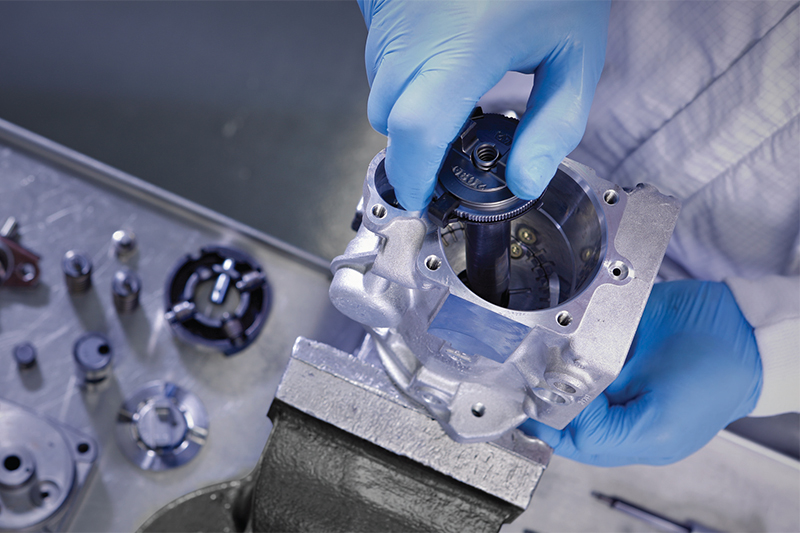
OE-approved remanufacturer, Carwood, explains why and how its sustainable products are the perfect solution to the cost of living crisis.
Carwood has more than 50 years expertise in the car, commercial vehicle, off-highway, motorsport and defence industries. Today, its remanufactured portfolio spans OEM- approved diesel fuel injectors and pumps, turbochargers, DPF cleaning, engines, hydraulics, starters, alternators and other coil wound electrical components, such as electric motors for the latest hybrid and electric vehicles. The company supplies these parts to leading vehicle manufacturers, OEMs, factory-owned race teams and distributors across the globe – its customers including Jaguar Land Rover, Mitsubishi, Perkins, CAT, Isuzu, Agco and the Ministry of Defence.
Remanufacturing: built-in quality at every stage
“Whilst we’re proud to have a wide-ranging and established customer base, including many of the industries’ biggest names, who it’s for, or what it is, is largely irrelevant. Every one of our remanufactured parts goes through the same stringent inspection, cleaning, rebuild, calibration and test procedures,” explains Simon Quantrell, deputy managing director, Carwood.
“Although the process itself may sound simple, the level at which this is done, and the know-how and equipment needed to do it, is more akin to the production of the original component – the only real difference being that we return a used part to its original condition, instead of producing a brand new one.”
The old part, otherwise known as the core, is critical to reman, and is why Carwood has a dedicated core team, managing stock of up to 10,000 pumps, 60,000 injectors and 10,000 turbochargers for both its own, and leading vehicle and engine manufacturer’s ranges.
On receipt, each core unit is carefully inspected against strict acceptance criteria to ensure its suitability for remanufacturing. Those that pass the test, the first of many, are individually sorted, labeled, and stored in a dedicated core warehouse.
Once selected, the unit is stripped down – any products with cracks, corrosion or faulty connectors are rejected. Reusable components are then thoroughly cleaned to remove dirt, debris and any contaminants, and inspected once again to ensure they meet the original specification and tolerances.
“We then start the process of putting them back together, replacing all wearable parts with like-for-like OE” adds Quantrell. “As an OE- approved remanufacturer for Bosch, Delphi Technologies, Denso and VDO, we also mirror their standards and processes. Our ISO14644 Class-7 certified clean room, for example, can filter down to as little as 0.5 microns, ensuring OE levels of cleanliness throughout the build.”
“Of course, no product will leave our factory, until it has gone through the same demanding test schedule as the OE product. For the latest common rail injectors, that can require some 700 test points just to recalibrate it – a critical step which allows the ECU to adjust fuel delivery and engine performance when the injector is installed back into the vehicle.”
For its turbos – covering OEMs such as BorgWarner, Garrett, IHI and Mitsubishi – all units are either fitted with a new CHRA, or are repaired and balanced using a VSR (vibration sorting rig), to ensure every moving part performs to the exact specification. Variable vane turbos are then calibrated on either a Turbo Technics VTR or G3 Power rig where the min and max flow rates are set to OEM standards.
“Through this process, we can be confident that every Carwood reman part has been returned to the vehicle manufacturer’s original factory specification,” continues Quantrell. “It’s a far cry from a reconditioned unit that has simply been disassembled, cleaned, and may or may not, have some damaged components replaced. Our products are just as good-as-new. Sometimes even better than new.”
He explains this last point: “By working closely with the OEMs, we are able to bring the very latest technology changes to older remanufactured parts. We can also engineer out any design defects, so more often than not, our reman part will outperform the original.”
Better for the environment
But that’s not the only benefit. In retaining both the material and value added from the original product, remanufacturing can save up to 70 per cent of the resources, and use around 85 per cent less energy than new.
“We’re not extracting new raw materials,” says Quantrell. “We’re using the part in its final form, so the processes aren’t anywhere nearly as intensive. Plus, we’re stopping waste from going to landfill. It’s a positive story about harnessing the circular economy, and one that we’re excited to be part of, ensuring our company continues to thrive, as does the environment we live in.”
Affordable solution
While environmentally conscious consumers are contributing to the growing demand, the inflation-beating power of remanufacturing is the biggest driver.
“Fuel, energy and food costs are going up like we’ve never seen before, so the end user – the vehicle owner – is looking for more economical solutions,” says Quantrell. “Because we reuse the core, it’s a lot more cost-effective than buying new. You’re getting the same performance as new OE, but it’s at least 25 per cent cheaper. Plus, you’re doing your bit for the planet.”
“We also know that the vehicle owner expects a quick fix, meaning garages are under increasing pressure to turn ramps faster. Which is why we’re committed to ensuring we have the right parts – old and late-model – in range, and together with our factor customers, can get them to you quickly. Similarly, we provide access to a technical hotline should you need on-the-job help with diagnosis, removal or refit.”
Quantrell concludes: “With an OE- approved brand like Carwood, you can access a wide range of premium quality, sustainable parts, at a competitive price. It’s what we call ‘Quality parts that don’t cost the Earth’. Simple as that.”