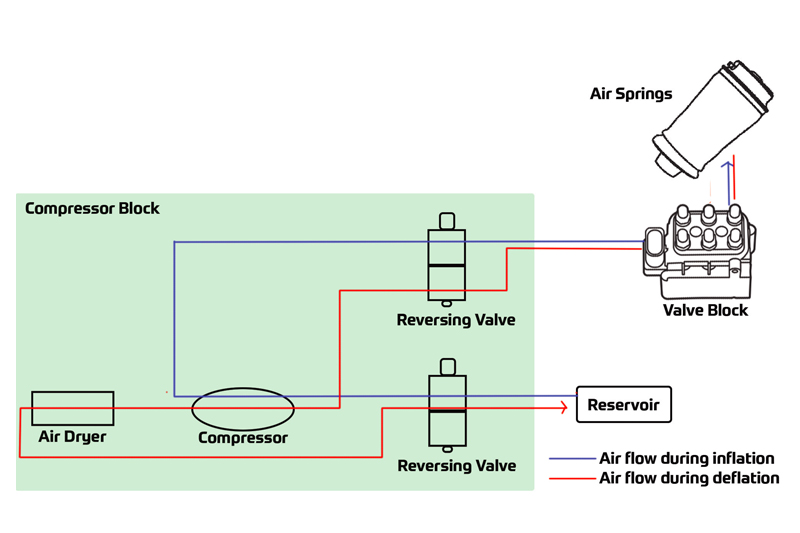
Air suspension specialist Arnott offers an insight into closed loop systems, an alternative to the conventional open air suspension system.
Not all automotive air suspension systems use the same working principle and so it is important for a professional workshop to know what system they are working on: a conventional open system or a so-called ‘closed loop’ air suspension system. The technical know-how for properly diagnosing possible system errors or defects, ensuring the correct working procedure is followed, correctly installing new air suspension components, and checking the system and making it operational again after an air spring leak is different from the conventional open air suspension system.
Inflation and deflation processes
Now that we know that specific technical knowledge and understanding is required, we can look at the general differences between the two systems’ working principles before diving deeper into the subject.
Looking at the graph above, it shows that the workings of the compressor are quite different in a closed loop system. Whereas in an open system the compressor compresses ambient air to fill the reservoir and/or air bellows, a closed loop compressor uses the pressurised nitrogen that is already existing in the system. Additionally, in a traditional air suspension system excessive air is released into the open but for a closed loop system the nitrogen stays inside the system and excessive pressure is led back to the reservoir. This is an important aspect to keep in mind when working on this system.
For inflation/additional pressure, the closed loop system uses two reversing valves that will open towards the valve block. Then the solenoid valve for the appropriate air spring opens and the additional pressure is transferred. When deflating, the excessive pressure is not discarded but cleverly routed back to the reservoir by opening the two reversing valves in the other direction. The excessive pressure is now transferred back into the reservoir. The pressure flow diagram below gives an indication of how the pressurised nitrogen is routed when an air spring is inflated or deflated.
The twist
Although it is called a ‘closed loop’ system and the diagram above shows how the compressed nitrogen is transferred from one area to another to inflate/deflate the system, a closed loop system does have the capability to make up for small amounts of nitrogen loss by drawing in and compressing atmospheric air. When the system has a leak, it will try to retain its required operating pressure by opening the (ambient) air intake.
However, it can only compensate for a small loss of nitrogen and when the compressed nitrogen mass gets too low the system will stop functioning.
Indicators
Just like a conventional air suspension system, the system pressure will gradually drop when there is a big air leak present. Therefore, a symptom of an under-charged system is lack of operation. However, in a closed loop system, the ECU (electronic control unit) continuously calculates the ‘nitrogen mass’ as an indication of normal operation. If too low, error messages like “max payload exceeded” might appear on the dashboard (depending on the car manufacturer).
An indicator of an overcharged system is audible discharging of excess pressure. This only occurs when a mechanic has not followed the correct procedure when recharging the system after a leak repair. It goes without saying that an overcharged system can lead to damaged and defective components, alongside serious safety consequences.
Tips and tricks
Now that Arnott has explained some of the basic working principles of a closed loop air suspension system, here is some key guidelines to obey when a vehicle needs repair or replacement on a closed loop air suspension system:
- The air springs/struts must be replaced if the vehicle has been driven/moved with one or more empty air bellows.
- The appropriate car manufacturer’s installation instructions must always be followed. If the instructions and specifications are not followed correctly, the system will continue to produce errors and malfunction.
- A vehicle raised with an empty air suspension system may not be lowered down onto its wheels or be driven. When the air springs/struts are empty and the vehicle is lifted, a vacuum is created in the air bellows. If the vehicle is then lowered afterwards, creases might develop in the bellows resulting in premature failure of the part.
- Follow the correct inflation procedure. Failure to adhere to these procedures could lead to shearing of the electrical connection, or other additional damage to the part. Not following the correct inflation process can even cause the air spring to explode due to pressure in the wrong component or over pressurising a component part.
- The nitrogen used to pressurise the air springs needs to be inside the system for the compressor to do its job. A closed loop compressor can only partially compensate for a pressure difference. If the system pressure gets below a certain value, the system needs to be recharged.
- In general, the output pressure in the system must be 17 bar after replacement of any spare part like air spring, air strut, compressor, and valve. Verify the manufacturer’s specification for the exact output pressure needed and always follow the recharging procedure as described by the manufacturer. Not following the correct inflation and recharging process can cause the air bellow to explode due to excessive pressure in the wrong component or over pressurising a component part.