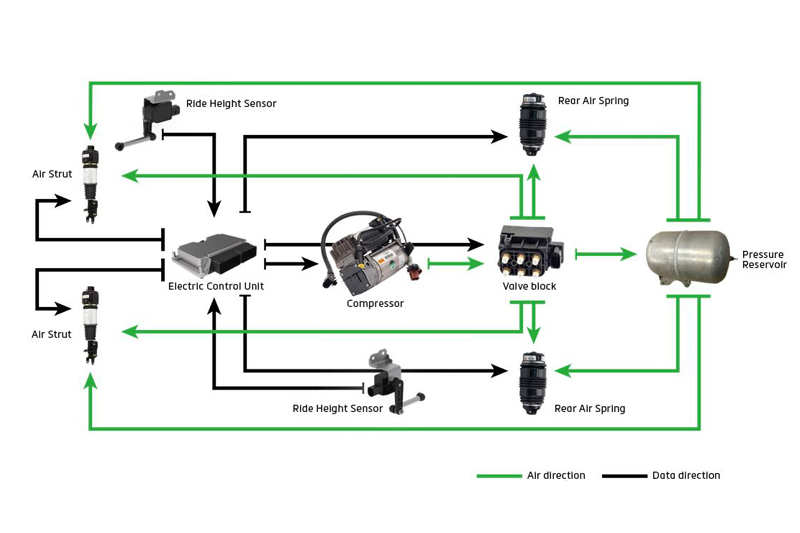
Here, Arnott Europe takes a deeper look into the role of the compressor in air suspension systems.
When you look at an air suspension system, the ECU (Electronic Control Unit) is often considered to be the brain of the system.
Following this line of thought, the compressor can be considered the beating heart of the system. Even though a compressor does not continuously run, when it no longer functions properly, the system will perform poorly and eventually shut down. This makes the compressor a vital component within the air suspension system!
A compressor provides the system pressure for the air suspension system and consists of an electromotor that drives the cylinder piston via a connecting rod. The air that is sucked in is compressed by the movement of the piston. The valve block then sends this compressed air through the air lines to the air springs or the pressure reservoir. The compressor is switched on and off by a relay that is controlled by the ECU.
The compressor also contains a dryer/filter element that keeps out any debris and absorbs moisture. The moisture is temporarily stored and will evaporate due to the heat of the compressor. The water vapour is then released back into the open air. In general, this component of the compressor is maintenance-free.
Most compressors are only designed for short-term pressure build-up. If the temperature rises above 100 degrees Celsius, the compressor will eventually get damaged. This is, for example, the case when a compressor is running too often or continuously due to a system leak.
An external pressure reservoir is often in place to manage the system pressure most efficiently, thereby shortening the compressor activation time.
Product quality
Although optically most compressors look identical, there are a lot of internal differences between the various compressor manufacturer offerings. In addition to OEM compressors, Arnott also develops its own compressors that meet strict requirements:
- The rotor and piston are balanced to prevent vibration and premature wear and tear of the piston rings and bearings
- The windings of the electromotor have a special varnish coating that is heat resistant and protects against internal short circuits. Additionally, the quality of the carbon brushes and windings are important for proper and smooth operation
- The ultra-smooth surface of the cylinder wall is finished using a CNC machine to prevent piston ring wear and tear. And, the aluminium undergoes a special heat treatment to obtain the correct hardness
- The surfaces of the bearings and shafts have a maximum tolerance of only 0,01 mm to guarantee a tight fit. This prevents vibrations and premature wear and tear of the electromotor’s bearing and shaft
Consequential damage
A defective compressor is almost always the result of a failure in another part of the air suspension system. It is, therefore, recommended that the entire air suspension system be checked for leaking components and seals after replacing a compressor.
Verify the air tightness of the seal between spring and strut, check the valve block connectors, Voss fittings but also the condition of the air lines themselves.
A water and soap solution usually works well in detecting a leak. Look for holes or tears in the air springs and stay alert, not all leaks are easily found. A leak can also be located on the unfolding edge of the air spring, which stays hidden at normal system height!
Symptoms
There are several symptoms of a malfunctioning compressor. Increased time required to change the vehicle’s ride height, continuous running and, in the worst case, not operating at all.
There are a several clear indicators of when a compressor is burned out: discoloration of the labels on the compressor, melted air lines/connectors and/or the presence of a burning smell when disassembling the unit.
Always replace the relay when replacing a compressor. This is a wear and tear part that can get sticky over time. When there is a leak in the system, the relay will continuously keep switching the compressor on. In the long run this is harmful not just for the compressor, but for the relay as well.