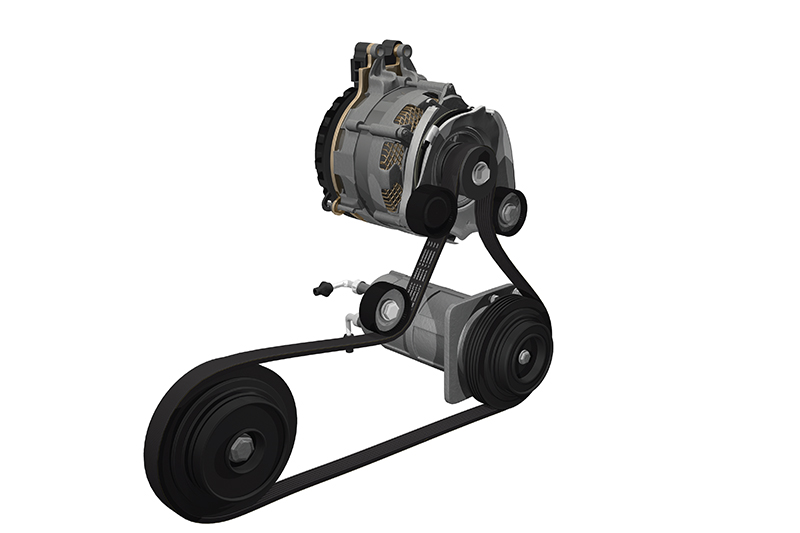
Parts specialist febi brings you a comprehensive overview of an essential component in ICE and mild-hybrid vehicles.
The traditional purpose of the auxiliary drive belt was to transmit the power of the engine to drive the alternator, radiator cooling fan, water pump, air-conditioning compressor and the power steering pump. This type of drive system had pulleys for each component and relied on one, two or three single V-belts to join them together and power each one. This method of driving the auxiliary components was inefficient and drained the engine of power – decreasing fuel efficiency and increasing exhaust emissions.
The friction losses of the original system had to evolve to release some of the power of the engine to drive the transmission. In addition, it also needed to improve noise, vibration and harshness characteristics and be more compact.
In the 1990s belt technology moved forward from the traditional single V-belt to the multi V-belt, which could drive all auxiliary components. The structure of the multi V-belt featured several adjacent ribs, which had a greater contact area than a conventional V-belt. This ensured maximum power transmission, outstanding flexibility, optimal dimensional stability, a longer service life and a smoother running performance. As a result, this allowed full flexibility throughout the belt’s operational life (even in serpentine drives which placed a greater strain on the belt with frequent bending cycles).
Another belt variant is the elastic multi Vbelt. These belts make additional tensioning pulleys unnecessary as they maintain the tension themselves, which places great demands on the structure and material of the belt. In addition, they also require special tools to stretch the new belt onto the auxiliary drive pulleys.
Pulleys and tensioners
Pulleys and sprung-loaded tensioners were also developed to reduce friction and vibration. This included the torsion vibration damper which was applied to crankshafts, particularly on engines that had high torque characteristics. This reduced vibration from the crankshaft as it rotated during the fourstroke cycle of the engine.
An alternator reacts more slowly than the engine. The high inertia level combined with a solid belt pulley prevents a rapid reduction in engine speed. As a result, when engine revolutions are reduced quickly, the slow-moving alternator must also be slowed down via the belt and then sped-up once more when the engine accelerates. This leads to irregular running and wear and tear within the entire drive belt system – increasing energy consumption.
The solution is an alternator fitted with an overrunning pulley which transmits torque in a single direction. This enables a quicker reduction of engine speed, whilst the alternator runs unobstructed for a short while. This reduces the strain on the entire auxiliary drive system during braking and gear changes – enabling a more efficient acceleration.
Stop-start
All the time an internal combustion engine is running it is using fuel and creating exhaust emissions from the combustion process, even when the car is not moving. A solution for this was to equip an existing car model with stop-start technology. As a result, a vehicle manufacturer did not incur the large development costs of a new engine or other emission reducing devices. This development required a strengthened starter motor, alternator and a battery that could withstand frequent cycles of being discharged and recharged, which was all monitored and controlled by the engine management control unit.
This technology further developed with alternators as they could be used as a motor to drive the crankshaft to start the engine when warm, as well as powering the vehicle’s 12-volt electrical system. As a result, the transition from a stopped engine, waiting at the traffic lights, to a running engine was even smoother and quicker. However, this repetitive process put a high strain on the auxiliary drive belt, leading to increased wear rates of the belt and tensioners.
Mild-hybrid
To reduce exhaust emissions, further stopstart technology had to evolve to reduce the load on the internal combustion engine and to meet the new upper limit of 95g of carbon dioxide per kilometre applied to new vehicles.
This system is known as a mild-hybrid and can save up to 15 per cent in fuel consumption, whilst reducing exhaust emissions. This technology significantly increases the vehicle’s efficiency as the combustion engine is only used when it’s required.
The system consists of a 48-volt intelligent starter-generator, which provides additional torque to the engine during acceleration and recovers kinetic energy during deceleration. It also helps to start the engine and generate electricity to power the many electrical demands of the vehicle.
A 48-volt Lithium-ion battery provides power to the starter motor, which can assist the engine during acceleration and reduce the load on the engine during cruising. It also powers the air conditioning when the engine is not running.
DC/DC Converter – converts the high voltage of the lithium-ion battery to 12- volts, which is required by sections of the vehicle‘s electrical system.
Essential parts of the mild-hybrid system are the drive belt and the tensioner. The belt required for a starter-generator is constantly exposed to a high amount of stress as a result of frequent load direction changes and tractive forces. This occurs when switching from driving the belt (for starting the engine) to generating electricity to maintain the load on the electrical system.
A strengthened multi-V belt is used to withstand up to ten times the amount of force than a standard belt in order to achieve and maintain the auxiliary belt performance. febi’s replacement auxiliary belts for starter-generators are designed, specified and manufactured to be OE-matching quality. All products deliver an optimised power transmission, a wear-resistant belt surface and excellent noise behaviour even under extreme conditions. The high strength aramid cords moulded within the belt withstand frequent load direction changes under high loads and tractive forces from the starter-generator. The superior static and dynamic load carrying capacity of the drive belt is also essential during the instantaneous restart of the internal combustion engine using the starter-generator after the vehicle has stopped.
These strengthened belts – using a reinforced elastomeric compound with a high fibre content can be quickly and easily identified. As an example, febi part no. 181286 also has a general service number of 5PK1166 EST. ‘’EST’’, which stands for electric start, defines that this belt is suitable for cars equipped with stop-start or a starter-generator for vehicles with a mild-hybrid drive.
Service replacement
febi’s range of high-performance auxiliary belts for intelligent starter-generators and auxiliary belt kits, which include tensioners and idler pulleys, meet the individual service replacement requirements of mild-hybrid vehicles. Many vehicle manufacturers advise replacing all the components of the auxiliary belt drive system at the same time as the recommended service interval.
Note: Conventional standard multi-V belts should not be used as a replacement for vehicles requiring strengthened belts as there is a high risk of increased belt wear and elevated noise levels. This can cause the belt to snap – damaging the auxiliary belt drive.