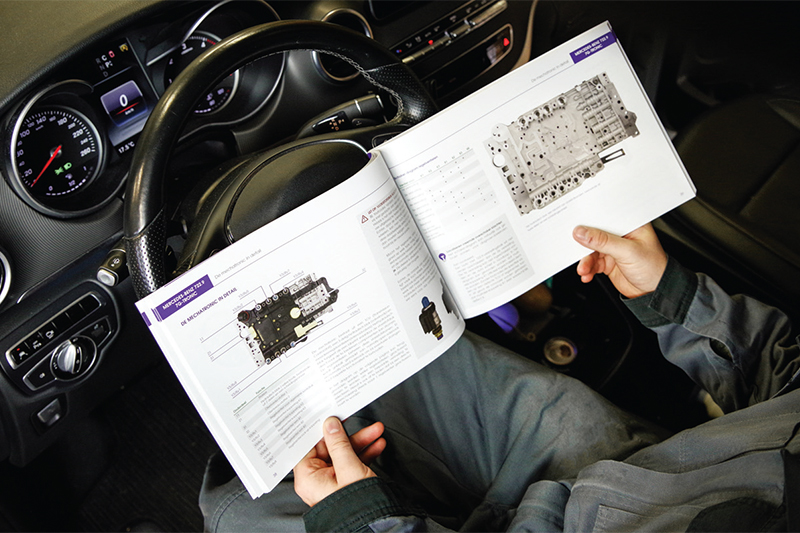
Remanufacturing expert ACtronics’ COO Thijs Jasink explains what goes into every remanufactured part.
The complexity of modern vehicles makes it increasingly difficult for car mechanics to determine the cause of a technical problem. That’s why at ACtronics remanufacturing is seen not as a product but as a service, whereby we gladly support the entire process from diagnosis to test drive. We are happy to share our knowledge in the form of technical advice from our product specialists, but also by publishing various supporting documents. So, with this concept in mind, let’s walk through our remanufacturing process.
Diagnosis and removal
As mentioned above, modern vehicle technology can be quite complex. While training options are endless, you just can’t know every little detail. So, when things get difficult, wouldn’t it be useful to have a specialist like ACtronics as a partner, who can help you both diagnose and solve the problem?
It was precisely this thought that prompted us to start making technical documentation. Besides the countless online articles and fault code lists on our website, we’ve also launched two diagnostic guides: a 120+ page book about transmission control units and a 150+ page one about the ABS/ESP braking system. It contains technical information, diagnosis tips and instructions how to remove and re-install the part properly. Our customers can download or order a copy in their online account. This initiative has been so well received that we are developing other editions as well.
Of course, when documentation isn’t sufficient, you can always call customer service. Our product specialists will help you out.
Packing and sending
Once it has been determined that the part is faulty, the next thing to do is pack it up and send it to us. Because our process is largely automated, this is a very important part of the process. It consists of four simple steps:
- Register the part for remanufacturing on our website
- Print out the Remanufacturing Order Form (ROF)
- Pack the part
- Send the package
Or alternatively to step 4:
Choose the pick-up service and we’ll have the package collected from your workshop.
Stay informed online
From here, everything is taken care of for you. The current status can be tracked in real time on ‘my account’ at our website and you will also receive status updates by email. Of course, we will always contact you should anything particular arise.
Testing, repairs and final inspection
Why would you limit to repair if there is a better alternative like remanufacturing? That’s quite the statement, but there are some major differences between the two. Where “repair” could be explained as a single action, “remanufacturing” is more like a whole process. At ACtronics remanufacturing consists of testing, all recommended repairs (not only the one that solves the current problem!) and a final inspection.
Testing
In general, any weaknesses in an electronic component do not always appear during the preproduction test period, but only after several years of everyday use. Because manufacturers have already shifted their focus to newer products by then, these weaknesses are often no longer corrected. This presents an opportunity for remanufacturing specialists like ACtronics, because we can analyse these weaknesses in detail and improve the product where necessary. In many instances, a remanufactured product is therefore even more reliable than a new one. This is also the main reason why we have a testing phase at ACtronics, where a part performs an automated script (simulation) that will expose any problems. Any underlying issues will certainly be noticed.
All recommended repairs
At ACtronics quality is top priority. This is reflected in the way we perform our repairs as well. Each remanufacturing solution has its own protocols and where possible improvements are made. We’ve even launched two fully automated remanufacturing lines last year, using vapor phase soldering, pick and place machines and glue robots. We are very proud to have come this far, but of course we’ll keep on improving.
Final inspection
No part will be shipped back to the customer unless a successful final inspection is completed. It uses the same automated script as entry testing, but the part must also pass a visual quality control.
Back into the car: plug-and-play?
And that’s it, just put the part back into the car and the job is done. But is it?
Encrypted components
For various reasons, car manufacturers are increasingly encrypting electronic components. This is making it increasingly difficult to replace these parts. Programming a new component often requires special (expensive) equipment as well as specialist knowledge of the procedures to be carried out. In these cases, it is therefore much easier to have the defective part remanufactured because it preserves existing configurations and minimises the need for re-learning. This saves valuable time as well. So yes, in most cases putting back a remanufactured part is really plug-and-play.
Software updates
As is the case with PCs and mobile phones, the electronics used in the automotive sector are also increasingly provided with software updates. This is common practice to ensure the existing functionality, but also for tightening up on environmental requirements or solving any problems found. Unfortunately, you will lose these updates as soon as a new component has to be installed. Of course, it’s possible to update these parts, but the procedures for doing so can be cumbersome. All of which makes remanufacturing a very interesting option.
Installation instructions
However, even putting back a part without programming and updating can be a complex process. To help you further and provide you with information after the remanufacture has been completed, we will supply you an installation instruction if necessary. And of course, you can also use our diagnostic guides.